-
What happened?
A worker was investigating a known below ground air leak in a pump assembly at an oily water detention pond.
The pump assembly is located in close proximity to the pond and is used to skim oil from the edge of the pond.
The worker was clearing some surface rock and soil from around pipework to identify the leak.
The steel working air pipe parted from the poly clamp and the pipe ejected past the worker’s face, striking their hard hat, and landed 7 metres (23 feet) away.
The worker sustained minor gravel rash to their wrist, requiring first aid.
At the time of the incident, the worker was alone.
The pond is located downhill from the main gas plant, out of sight from other parts of the plant.
-
Why did it happen?
The oil skimming system was built in 2007 to a standard that did not ensure sufficient piping support. Pipe supports and restraints were not installed and the overall design of the pump assembly did not minimise stresses at joints. Over time, the routine operation of the valving created a fatigue failure of the poly to steel coupling.
The system contained plant air. The process fluid is not hazardous. The equipment was not subject to preventative maintenance / routine inspection because it was considered non-critical and non-hazardous. However, the operating pressure is a hazard.
-
What did they learn?
Review maintenance / inspection strategies for plant air systems to ensure the risks posed by operating pressures are addressed.
Review the design of plant air piping assemblies to ensure that stresses on joints are minimised. Pay particular attention to ageing assets and high-density polyethylene (HDPE)/steel connections.
If the worker had been incapacitated, they would have been out of sight of other personnel at the main gas plant. It is not uncommon that there is only one worker at the plant. Consider application of Lone and Remote Worker processes.
-
Ask yourself or your crew
Do you have equipment / systems (including plant air) that are on a ‘run to failure maintenance strategy’ because they are considered non-critical / non-hazardous? Have the risks posed by operating pressures been adequately addressed? Should these systems have some level of inspection / maintenance to ensure their integrity?
Do you work alone? Are you aware of Lone and Remote Worker procedures that apply to your work? Do you make use of the lone worker functionality on radios or take other precautions when working alone?
Add to homescreen
Content name
Select existing category:
Content name
New collection
Edit collection
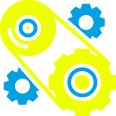
What happened?
A worker was investigating a known below ground air leak in a pump assembly at an oily water detention pond.
The pump assembly is located in close proximity to the pond and is used to skim oil from the edge of the pond.
The worker was clearing some surface rock and soil from around pipework to identify the leak.
The steel working air pipe parted from the poly clamp and the pipe ejected past the worker’s face, striking their hard hat, and landed 7 metres (23 feet) away.
The worker sustained minor gravel rash to their wrist, requiring first aid.
At the time of the incident, the worker was alone.
The pond is located downhill from the main gas plant, out of sight from other parts of the plant.
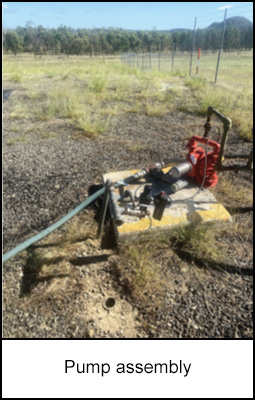
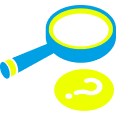
Why did it happen?
The oil skimming system was built in 2007 to a standard that did not ensure sufficient piping support. Pipe supports and restraints were not installed and the overall design of the pump assembly did not minimise stresses at joints. Over time, the routine operation of the valving created a fatigue failure of the poly to steel coupling.
The system contained plant air. The process fluid is not hazardous. The equipment was not subject to preventative maintenance / routine inspection because it was considered non-critical and non-hazardous. However, the operating pressure is a hazard.
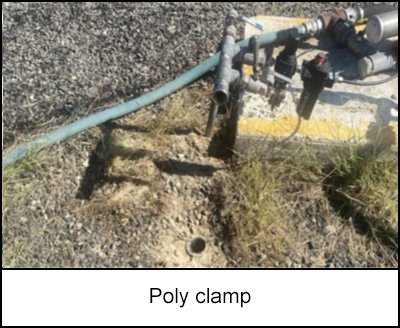
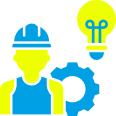
What did they learn?
Review maintenance / inspection strategies for plant air systems to ensure the risks posed by operating pressures are addressed.
Review the design of plant air piping assemblies to ensure that stresses on joints are minimised. Pay particular attention to ageing assets and high-density polyethylene (HDPE)/steel connections.
If the worker had been incapacitated, they would have been out of sight of other personnel at the main gas plant. It is not uncommon that there is only one worker at the plant. Consider application of Lone and Remote Worker processes.
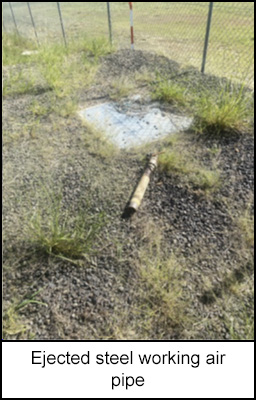
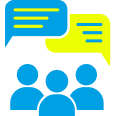
Ask yourself or your crew
Do you have equipment / systems (including plant air) that are on a ‘run to failure maintenance strategy’ because they are considered non-critical / non-hazardous? Have the risks posed by operating pressures been adequately addressed? Should these systems have some level of inspection / maintenance to ensure their integrity?
Do you work alone? Are you aware of Lone and Remote Worker procedures that apply to your work? Do you make use of the lone worker functionality on radios or take other precautions when working alone?
While investigating an underground air leak at an oily water detention pond, a worker was struck by a dislodged air pipe, sustaining minor injuries. The incident occurred while the worker was alone and out of sight from the main gas plant.
Original material courtesy of Safer Together (Australia)
To access the PDF and PowerPoint versions, please visit https://www.safertogether.com.au/resources/sharing-library/working-with-near-pressurised-systems-person-in-line-of-fire-leb-toolbox