-
What happened?
A well servicing crew finished pumping water down the casing side of the well and was preparing to conduct a stump test. They connected the Kelly hose to the stump testing apparatus and blowout preventor (BOP), which were mounted on a vehicle.
The casing vacuum had sucked all the water out of the line pipe and the pump, so the rig pump operator attempted to fill the BOP stack with water to conduct a pressure test. Both sets of rams were open and there was no pup joint in the BOP stack.
A low-pressure transfer pump was used to pump water to the stump testing apparatus; however, no water came out of the BOP stack. The crew believed the pump was not primed because the casing vacuum had sucked all the water out of the line pipe and pump and the rig tank was nearly empty.
Another crew member was positioned at the BOP to watch for water and looked down into the BOP when hydraulic fitting caps dislodged, fatally striking him in the head.
All hydraulic fitting caps for that rig were accounted for, and it is unknown how or when they got into the test stump apparatus and BOP.
-
Why did it happen?
- Crew members did not realize the pump was primed and that air was being compressed in the piping.
- The hydraulic fitting caps were lodged into the bottom of the test stump apparatus, creating trapped pressure.
- The worker did not realize he was positioned in the line of fire.
-
What did they learn?
- Educate crews that even a BOP installed on the test stump is a potential line of fire hazard.
- Recognize that even relatively low pressures, such as 45 psi (310 kPa), have the potential to store a lot of energy, especially when trapped gas is present.
- Keep a BOP hole cover installed when the BOP is not in use. Through the course of the investigation, it was verified that the caps could not have been pumped through the BOP stump and entered the stump from the top.
- Prior to use, conduct a visual inspection to verify there are no foreign objects inside the BOP.
- Consider the installation of bar-stock collars to prevent objects from falling into and becoming lodged in the test stump apparatus and the associated BOP.
-
Ask yourself or your crew
- How can something like this happen here (e.g. on our site)?
- What safety measures (i.e. procedures, controls/barriers) do we have in place to mitigate the risk?
- How do we know the risk controls/barriers are working?
- What improvements or changes should we make to the procedures, controls/barriers or the way we work?
Add to homescreen
Content name
Select existing category:
Content name
New collection
Edit collection
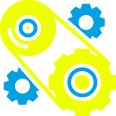
What happened?
A well servicing crew finished pumping water down the casing side of the well and was preparing to conduct a stump test. They connected the Kelly hose to the stump testing apparatus and blowout preventor (BOP), which were mounted on a vehicle.
The casing vacuum had sucked all the water out of the line pipe and the pump, so the rig pump operator attempted to fill the BOP stack with water to conduct a pressure test. Both sets of rams were open and there was no pup joint in the BOP stack.
A low-pressure transfer pump was used to pump water to the stump testing apparatus; however, no water came out of the BOP stack. The crew believed the pump was not primed because the casing vacuum had sucked all the water out of the line pipe and pump and the rig tank was nearly empty.
Another crew member was positioned at the BOP to watch for water and looked down into the BOP when hydraulic fitting caps dislodged, fatally striking him in the head.
All hydraulic fitting caps for that rig were accounted for, and it is unknown how or when they got into the test stump apparatus and BOP.
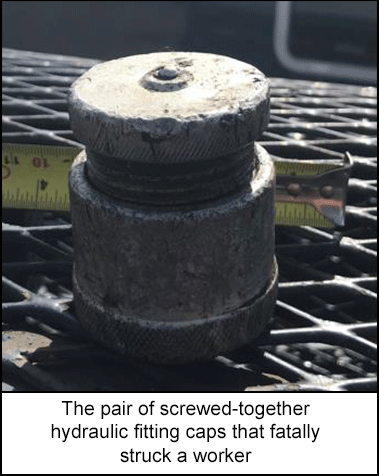
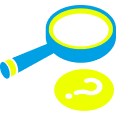
Why did it happen?
- Crew members did not realize the pump was primed and that air was being compressed in the piping.
- The hydraulic fitting caps were lodged into the bottom of the test stump apparatus, creating trapped pressure.
- The worker did not realize he was positioned in the line of fire.
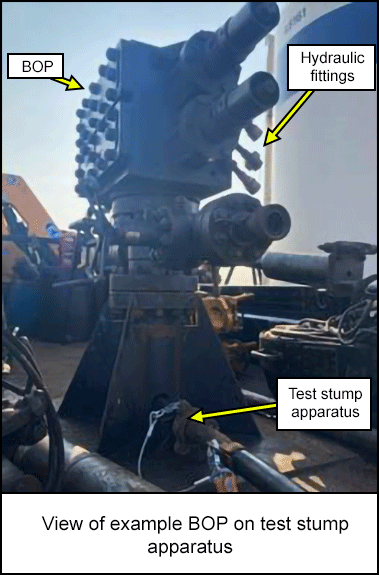
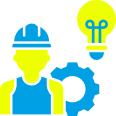
What did they learn?
- Educate crews that even a BOP installed on the test stump is a potential line of fire hazard.
- Recognize that even relatively low pressures, such as 45 psi (310 kPa), have the potential to store a lot of energy, especially when trapped gas is present.
- Keep a BOP hole cover installed when the BOP is not in use. Through the course of the investigation, it was verified that the caps could not have been pumped through the BOP stump and entered the stump from the top.
- Prior to use, conduct a visual inspection to verify there are no foreign objects inside the BOP.
- Consider the installation of bar-stock collars to prevent objects from falling into and becoming lodged in the test stump apparatus and the associated BOP.
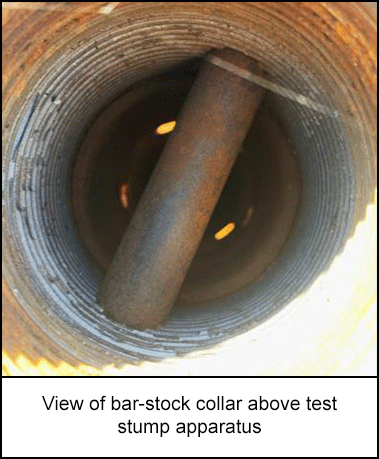
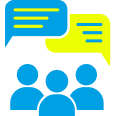
Ask yourself or your crew
- How can something like this happen here (e.g. on our site)?
- What safety measures (i.e. procedures, controls/barriers) do we have in place to mitigate the risk?
- How do we know the risk controls/barriers are working?
- What improvements or changes should we make to the procedures, controls/barriers or the way we work?
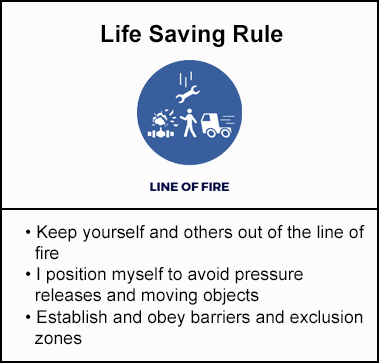
A well servicing crew finished pumping water down the casing side of the well and was preparing to conduct a stump test. A crew member was positioned at the blowout preventor (BOP) to watch for water and looked down into the BOP when hydraulic fitting caps dislodged, fatally striking him in the head.