-
What happened?
A pipeline crew welding together a pipeline segment was using an excavator to make minor adjustments to the alignment of the pipe.
The machine's controls were locked-out while the pipeline welder was working on the pipe. When an adjustment to the pipe's alignment was required, the welder stepped back from the pipe and the excavator operator was signalled to make the adjustment.
The excavator operator sat down in the operator's seat and did not notice that his jacket caught on the control stick and engaged it. The excavator operator proceeded to disengage the lockout lever and the boom of the excavator immediately went into motion, pulling the pipe segment in towards the bank of the excavation. This caused the welder to be crushed between the pipe and the bank of the excavation.
The welder suffered serious injuries, including broken ribs, a punctured lung and a fractured jaw.
-
Why did it happen?
Lockout failure: The controls of the excavator were supposed to be locked out while the pipeline welder was working on the pipe.
Jacket entanglement: The excavator operator's jacket caught on the control stick, which led to the unintentional engagement of the controls when he sat down in the operator's seat.
Failure to notice: The excavator operator did not notice that his jacket had engaged the control stick.
Unintended movement: When the lockout lever was disengaged, the boom of the excavator moved unexpectedly, pulling the pipeline segment towards the excavation bank.
-
What did they learn?
The design of the lockout on the excavator does not include a failsafe to prevent movement of the boom upon release of the lockout if the controls are pre-engaged.
As recommendation, the standard operating procedures need to:
- Define when the lockout needs to be engaged.
- Ensure the operator confirms all controls are in the neutral position and all personnel are clear of the hazard zone (swing area) before the lockout is disengaged.
It is recommended to communicate this risk potential with industry including heavy equipment manufacturers.
-
Ask yourself or your crew
- How can something like this happen here (e.g. on our site)?
- What safety measures (i.e. procedures, controls/barriers) do we have in place to mitigate the risk?
- How do we know the risk controls/barriers are working?
- What improvements or changes should we make to the procedures, controls/barriers or the way we work?
Add to homescreen
Content name
Select existing category:
Content name
New collection
Edit collection
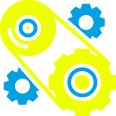
What happened?
A pipeline crew welding together a pipeline segment was using an excavator to make minor adjustments to the alignment of the pipe.
The machine's controls were locked-out while the pipeline welder was working on the pipe. When an adjustment to the pipe's alignment was required, the welder stepped back from the pipe and the excavator operator was signalled to make the adjustment.
The excavator operator sat down in the operator's seat and did not notice that his jacket caught on the control stick and engaged it. The excavator operator proceeded to disengage the lockout lever and the boom of the excavator immediately went into motion, pulling the pipe segment in towards the bank of the excavation. This caused the welder to be crushed between the pipe and the bank of the excavation.
The welder suffered serious injuries, including broken ribs, a punctured lung and a fractured jaw.
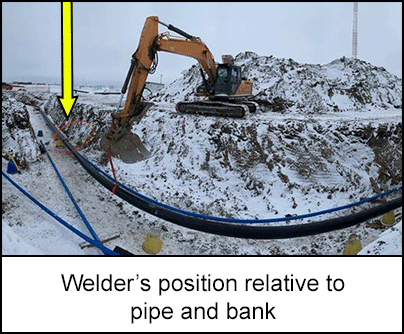
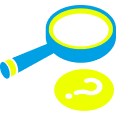
Why did it happen?
Lockout failure: The controls of the excavator were supposed to be locked out while the pipeline welder was working on the pipe.
Jacket entanglement: The excavator operator's jacket caught on the control stick, which led to the unintentional engagement of the controls when he sat down in the operator's seat.
Failure to notice: The excavator operator did not notice that his jacket had engaged the control stick.
Unintended movement: When the lockout lever was disengaged, the boom of the excavator moved unexpectedly, pulling the pipeline segment towards the excavation bank.
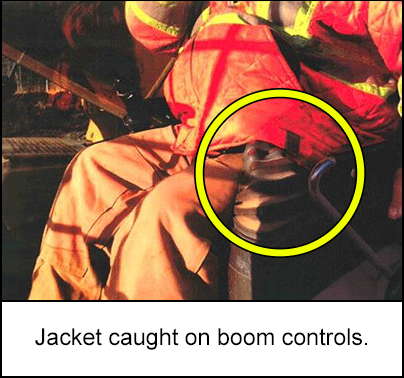
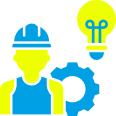
What did they learn?
The design of the lockout on the excavator does not include a failsafe to prevent movement of the boom upon release of the lockout if the controls are pre-engaged.
As recommendation, the standard operating procedures need to:
- Define when the lockout needs to be engaged.
- Ensure the operator confirms all controls are in the neutral position and all personnel are clear of the hazard zone (swing area) before the lockout is disengaged.
It is recommended to communicate this risk potential with industry including heavy equipment manufacturers.
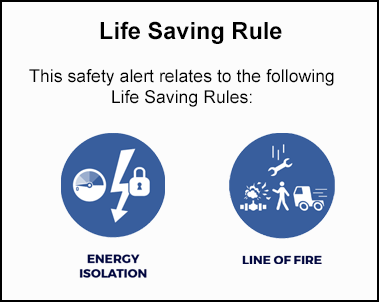
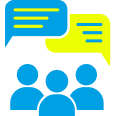
Ask yourself or your crew
- How can something like this happen here (e.g. on our site)?
- What safety measures (i.e. procedures, controls/barriers) do we have in place to mitigate the risk?
- How do we know the risk controls/barriers are working?
- What improvements or changes should we make to the procedures, controls/barriers or the way we work?
Pipeline crew were conducting welding activities using an excavator to make minor adjustments to the alignment of the pipe. An adjustment was required so the welder stepped back and signalled to the operator. The excavator operator sat down not realising his jacket had caught on the control stick and engaged it. The welder suffered serious injuries, including broken ribs, a punctured lung and a fractured jaw.