-
What happened?
A welder was injured when the set screw on a heavy-duty tripod pipe jack failed causing the pipe jack to collapse.
The 10-inch pipe spool being worked on rolled off the V-head, forcing all the remaining pipe jacks to shift. The pipe rolled onto the welder, pushing him to the ground and crushing his upper body.
The welder sustained a broken right shoulder, left arm, and broken ribs.
-
Why did it happen?
- The set screw (securement pin) on the pipe jack was not adequately secured.
- The rolling pipe forced the remaining pipe jacks to topple towards the worker.
- Pipe jacks were not inspected before work began.
- Set screws were not inspected before work began.
Contributing factors:
The pipe jack did not allow the set screw or the secondary pin to be properly secured because it had been painted over and corroded by use. The secondary pin was not properly secured. In addition, the pipe jacks were set up on uneven ground.
-
What did they learn?
- Inspect the equipment. Before using pipe jacks, check all parts to ensure they are in good operating condition and have not been modified. Inspect pipe jack and legs for bends, breaks or metal deformation.
- Only use pipe jacks on smooth, level surfaces to reduce the risk of them tipping over.
- Ensure pipe jacks are not overloaded; know the load rating for each pipe jack and the head.
- Position jacks 5 to 12 feet (1.5 to 3.5 m) apart, depending on length and weight of load (check manufacturer’s instructions for pipe weight and diameter). For longer segments of pipe, it is recommended to have at least four jacks spread evenly under the load.
- Adjust the spanner nut beneath the V-head, so at least 2 to 3 inches (50 to 75 mm) of adjustment screw is visible coming out of the I.D. barrel.
- Tighten the set screw so the head cannot come out of the I.D. barrel.
- Do not store pipe on pipe jacks.
-
Ask yourself or your crew
- How can something like this happen here (e.g. on our site)?
- What safety measures (i.e. procedures, controls/barriers) do we have in place to mitigate the risk?
- How do we know the risk controls/barriers are working?
- What improvements or changes should we make to the procedures, controls/barriers or the way we work?
Add to homescreen
If you want to add this app to home screen tap and then ‘Add to Home Screen’.
Content name
Select existing category:
Content name
New collection
Edit collection
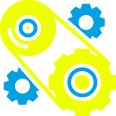
What happened?
A welder was injured when the set screw on a heavy-duty tripod pipe jack failed causing the pipe jack to collapse.
The 10-inch pipe spool being worked on rolled off the V-head, forcing all the remaining pipe jacks to shift. The pipe rolled onto the welder, pushing him to the ground and crushing his upper body.
The welder sustained a broken right shoulder, left arm, and broken ribs.
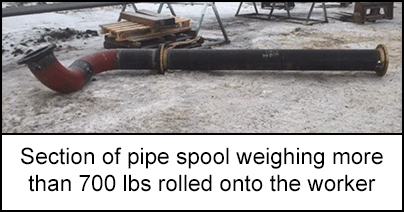
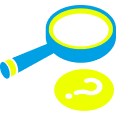
Why did it happen?
- The set screw (securement pin) on the pipe jack was not adequately secured.
- The rolling pipe forced the remaining pipe jacks to topple towards the worker.
- Pipe jacks were not inspected before work began.
- Set screws were not inspected before work began.
Contributing factors:
The pipe jack did not allow the set screw or the secondary pin to be properly secured because it had been painted over and corroded by use. The secondary pin was not properly secured. In addition, the pipe jacks were set up on uneven ground.
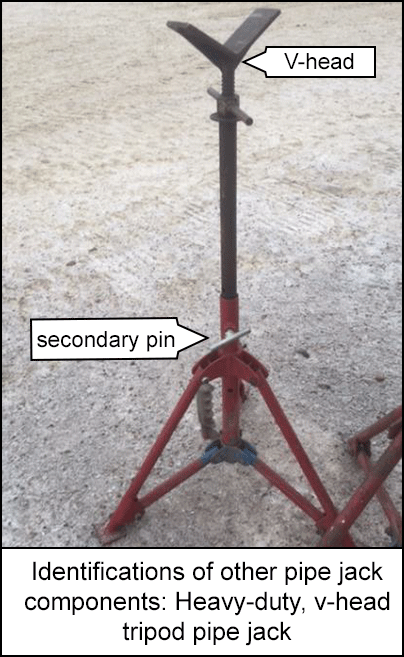
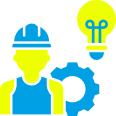
What did they learn?
- Inspect the equipment. Before using pipe jacks, check all parts to ensure they are in good operating condition and have not been modified. Inspect pipe jack and legs for bends, breaks or metal deformation.
- Only use pipe jacks on smooth, level surfaces to reduce the risk of them tipping over.
- Ensure pipe jacks are not overloaded; know the load rating for each pipe jack and the head.
- Position jacks 5 to 12 feet (1.5 to 3.5 m) apart, depending on length and weight of load (check manufacturer’s instructions for pipe weight and diameter). For longer segments of pipe, it is recommended to have at least four jacks spread evenly under the load.
- Adjust the spanner nut beneath the V-head, so at least 2 to 3 inches (50 to 75 mm) of adjustment screw is visible coming out of the I.D. barrel.
- Tighten the set screw so the head cannot come out of the I.D. barrel.
- Do not store pipe on pipe jacks.
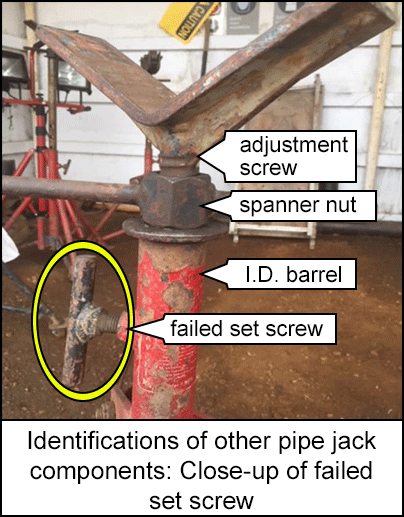
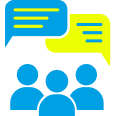
Ask yourself or your crew
- How can something like this happen here (e.g. on our site)?
- What safety measures (i.e. procedures, controls/barriers) do we have in place to mitigate the risk?
- How do we know the risk controls/barriers are working?
- What improvements or changes should we make to the procedures, controls/barriers or the way we work?
Published on 05/06/23
1193 Views
A welder was injured when the set screw on a heavy-duty tripod pipe jack failed causing the pipe jack to collapse. The welder sustained a broken right shoulder, left arm and broken ribs.
Original material courtesy of Energy Safety Canada