-
What happened?
A company contracted services to clean out a production tank containing hydrocarbons.
Hydrocarbons are highly volatile and, under certain conditions such as agitation, can flash off-gases or fumes. In this case, fumes were ignited by the operating vac truck equipment and a flash fire occurred.
-
Why did it happen?
- Not all hazards were adequately controlled, allowing migration of hydrocarbons in the work space.
- Inadequate air movement at the production tank.
- High temperature alarm on vac truck was ignored.
Contributing factors:
- The worker did not report the hydrocarbon hazard to the site supervisor or the
employer, and hand-held gas detection equipment was not used.
-
What did they learn?
- Ensure a Safe Work Permit or Work Authorization Permit is in place. These documents detail the nature, and scope of the work, and identify site hazards in the area of the intended work. Safe Work Permits specify the precautions in place and/or to be implemented to mitigate risk to workers.
- Understand the potential travel path of any vapours discharged during loading. Before starting operations, consider atmospheric and wind conditions; topography of the surrounding area, including low spots where vapours may collect; and potential ignition sources. Exercise caution as vapours may reach the flammable range during low flow periods.
- Review product safety information including, but not limited to: toxicity, corrosiveness, flammability, reactivity and combustibility. When the material being transferred is a mixture of many products, a contaminated product or a waste product, additional information may be required such as Safety Data Sheet for blended product. Keep in mind that under vacuum the risk of higher flashpoint can be realized dependent upon the product.
- Before starting any operations, workers should conduct a job hazard analysis to: identify additional hazards not already controlled; ensure suitable PPE is used, and confirm procedures and plans are in place to mitigate risks associated with the identified hazard(s).
- Workers may refuse to do work they believe (on reasonable grounds) is dangerous to them or others. Worker must promptly report the refusal to the supervisor or employer.
- If the supervisor or employer cannot remedy the hazard immediately, work is to be stopped and re-assessed, and controls must be put in place.
-
Ask yourself or your crew
How can we prevent something like this from happening here?
What are other risks are associated with forklift operations? How can you mitigate those risks at your work site?
What safety recommendations should be included in the operational instructions?
How can we, as a company, implement a practical training plan that focuses on the job position, and make sure pedestrians are safer from forklifts in the future?
Add to homescreen
If you want to add this app to home screen tap and then ‘Add to Home Screen’.
Content name
Select existing category:
Content name
New collection
Edit collection
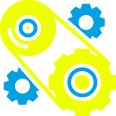
What happened?
A company contracted services to clean out a production tank containing hydrocarbons.
Hydrocarbons are highly volatile and, under certain conditions such as agitation, can flash off-gases or fumes. In this case, fumes were ignited by the operating vac truck equipment and a flash fire occurred.
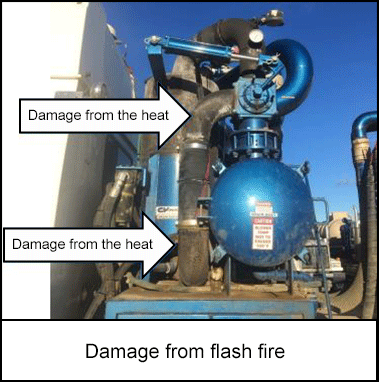
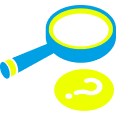
Why did it happen?
- Not all hazards were adequately controlled, allowing migration of hydrocarbons in the work space.
- Inadequate air movement at the production tank.
- High temperature alarm on vac truck was ignored.
Contributing factors:
- The worker did not report the hydrocarbon hazard to the site supervisor or the
employer, and hand-held gas detection equipment was not used.
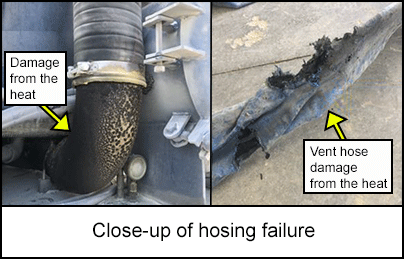
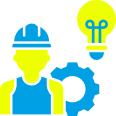
What did they learn?
- Ensure a Safe Work Permit or Work Authorization Permit is in place. These documents detail the nature, and scope of the work, and identify site hazards in the area of the intended work. Safe Work Permits specify the precautions in place and/or to be implemented to mitigate risk to workers.
- Understand the potential travel path of any vapours discharged during loading. Before starting operations, consider atmospheric and wind conditions; topography of the surrounding area, including low spots where vapours may collect; and potential ignition sources. Exercise caution as vapours may reach the flammable range during low flow periods.
- Review product safety information including, but not limited to: toxicity, corrosiveness, flammability, reactivity and combustibility. When the material being transferred is a mixture of many products, a contaminated product or a waste product, additional information may be required such as Safety Data Sheet for blended product. Keep in mind that under vacuum the risk of higher flashpoint can be realized dependent upon the product.
- Before starting any operations, workers should conduct a job hazard analysis to: identify additional hazards not already controlled; ensure suitable PPE is used, and confirm procedures and plans are in place to mitigate risks associated with the identified hazard(s).
- Workers may refuse to do work they believe (on reasonable grounds) is dangerous to them or others. Worker must promptly report the refusal to the supervisor or employer.
- If the supervisor or employer cannot remedy the hazard immediately, work is to be stopped and re-assessed, and controls must be put in place.
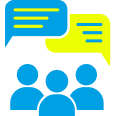
Ask yourself or your crew
How can we prevent something like this from happening here?
What are other risks are associated with forklift operations? How can you mitigate those risks at your work site?
What safety recommendations should be included in the operational instructions?
How can we, as a company, implement a practical training plan that focuses on the job position, and make sure pedestrians are safer from forklifts in the future?
Published on 31/03/23
1504 Views
A production tank containing hydrocarbons was being cleaned. Hydrocarbons are highly volatile and, under certain conditions such as agitation, can flash off-gases or fumes. In this case, fumes were ignited by the operating vac truck equipment and a flash fire occurred.
Original material courtesy of Energy Safety Canada