-
What happened?
The nitrogenation of a tanker was being carried out on a loading platform to ensure that no water remained before loading propellant.
The nitrogen hose was attached to the tanker to perform a first removal of possible water from the lorry’s tanker.
When the remaining water was pumped out to the atmosphere, an aromatic compound smell was noticed.
This caused throat irritation and burning in the eyes of the operator performing the work, two operations personnel members who were in a booth nearby, and the lorry driver. All four inhaled aromatic compounds and were provided with first aid due to the unplanned hydrocarbon release.
-
Why did it happen?
There was a failure of a check valve, or a lack of this type of valve, during nitrogen intake in a prior operation. The nitrogen checks required by the design standard were still pending for some centres.
The service hose station check valve may have failed due to lack of maintenance. Its condition was unknown.
The contamination occurred when the nitrogen hose connections remained connected after completing inerting tasks.
Several days prior, an odour was noticed in the piping, but no action was taken.
The personnel inside the booth were not notified of the presence of hydrocarbon vapours, thus they were not evacuated.
-
What did they learn?
Analyse the conditions in your facilities and ensure they are in compliance with the design standard to minimise contamination risk.
Before making temporary connections to ancillary services, check that the connection diagram has all the necessary elements to prevent reverse flow.
Before using the nitrogen network, check for the absence of contamination (especially explosiveness).
Disconnect the equipment from the nitrogen network. Perform inspections prior to start-up and regularly to check that all the connections to the nitrogen network or other services, including hoses, have been disconnected.
Check during stops that the nitrogen network has not been contaminated by the permanent inertisation systems.
In pre-operational, identify revision times for the connections to the nitrogen networks by reversible blind flanges and make sure that they are in a position identified in the piping and instrumentation diagram (P&I).
Ensure that critical equipment such as nitrogen network check valves are maintained periodically.
Report any indications of contamination or a leak (odour, noises, etc.) to prevent incidents.
-
Ask yourself or your crew
How can something like this happen here? What can we do to prevent it from happening?
What should you do if you notice any odour, noises, indications of a leak or contamination on your equipment?
How often do we conduct checks and planned maintenance? How do we know that is sufficient?
Why is it important to be alert and check for potential risks while performing a task and not just prior to starting the task?
How can we improve the way we work?
Add to homescreen
Content name
Select existing category:
Content name
New collection
Edit collection
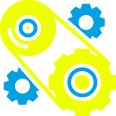
What happened?
The nitrogenation of a tanker was being carried out on a loading platform to ensure that no water remained before loading propellant.
The nitrogen hose was attached to the tanker to perform a first removal of possible water from the lorry’s tanker.
When the remaining water was pumped out to the atmosphere, an aromatic compound smell was noticed.
This caused throat irritation and burning in the eyes of the operator performing the work, two operations personnel members who were in a booth nearby, and the lorry driver. All four inhaled aromatic compounds and were provided with first aid due to the unplanned hydrocarbon release.
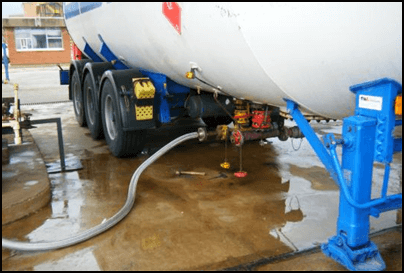
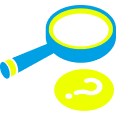
Why did it happen?
There was a failure of a check valve, or a lack of this type of valve, during nitrogen intake in a prior operation. The nitrogen checks required by the design standard were still pending for some centres.
The service hose station check valve may have failed due to lack of maintenance. Its condition was unknown.
The contamination occurred when the nitrogen hose connections remained connected after completing inerting tasks.
Several days prior, an odour was noticed in the piping, but no action was taken.
The personnel inside the booth were not notified of the presence of hydrocarbon vapours, thus they were not evacuated.
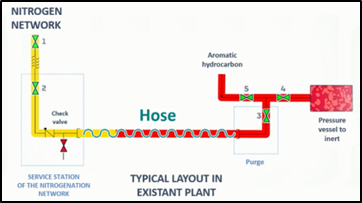
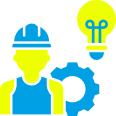
What did they learn?
Analyse the conditions in your facilities and ensure they are in compliance with the design standard to minimise contamination risk.
Before making temporary connections to ancillary services, check that the connection diagram has all the necessary elements to prevent reverse flow.
Before using the nitrogen network, check for the absence of contamination (especially explosiveness).
Disconnect the equipment from the nitrogen network. Perform inspections prior to start-up and regularly to check that all the connections to the nitrogen network or other services, including hoses, have been disconnected.
Check during stops that the nitrogen network has not been contaminated by the permanent inertisation systems.
In pre-operational, identify revision times for the connections to the nitrogen networks by reversible blind flanges and make sure that they are in a position identified in the piping and instrumentation diagram (P&I).
Ensure that critical equipment such as nitrogen network check valves are maintained periodically.
Report any indications of contamination or a leak (odour, noises, etc.) to prevent incidents.
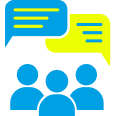
Ask yourself or your crew
How can something like this happen here? What can we do to prevent it from happening?
What should you do if you notice any odour, noises, indications of a leak or contamination on your equipment?
How often do we conduct checks and planned maintenance? How do we know that is sufficient?
Why is it important to be alert and check for potential risks while performing a task and not just prior to starting the task?
How can we improve the way we work?
The nitrogenation of a tanker was being carried out on a loading platform to ensure that no water remained before loading propellant. Four workers inhaled aromatic compounds and were provided with first aid due to an unplanned hydrocarbon release.