-
What happened?
A drill crew was in process of pulling out of hole and racking back the bottom-hole assembly.
As part of this task, the assistant driller utilised the tugger to break down the bottom-hole assembly components to ready them for laydown.
After completing this task, a floor hand secured the tugger to the starboard forward snubbing post, unknowingly catching the tugger wire in the aft HydraRacker guide jaw.
When the aft HydraRacker moved to complete the next job step, the tugger wire parted under tension, falling approximately 25 metres (83 feet) to the rig floor.
Operations were suspended and the tugger line inspected to verify there were no additional drops potential prior to securing the scene and reporting the incident.
-
Why did it happen?
The incident was triggered by the inadvertent interaction between the tugger wire and the aft HydraRacker guide jaw.
This unintended collision was a result of the rig floor equipment's design and positioning, which led to the tugger wire being caught, resulting in its breakage.
-
What did they learn?
The engineered design and location of equipment can introduce unintended interaction and potential for incident when in operation.
Revise and update the collision checklist to ensure it's actively used at suitable intervals.
Develop a 'No Parking' zone for the HydraRacker to prevent it being parked in the position where the tugger line is susceptible to being caught in the guide jaw.
Consider the installation of breakaway links between the tugger line hook and the securing point to mitigate potential event severity of a caught tugger wire.
-
Ask yourself or your crew
How can something like this happen on our site?
How often do you evaluate the potential risks of collisions when you're positioning equipment on the rig floor? What specific steps or methods do you use to carry out these risk assessments?
What measures do you currently take to prevent entanglement between equipment, especially during tasks involving wire lines like the tugger?
Can you recall an instance where equipment positioning led to a close call or potential hazard? What were the circumstances, and how was it addressed?
How do you communicate with fellow crew members to ensure the safe positioning and movement of equipment during drilling operations?
How can we improve the rig floor safety protocols to prevent similar accidents from happening?
Add to homescreen
Content name
Select existing category:
Content name
New collection
Edit collection
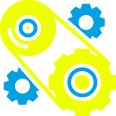
What happened?
A drill crew was in process of pulling out of hole and racking back the bottom-hole assembly.
As part of this task, the assistant driller utilised the tugger to break down the bottom-hole assembly components to ready them for laydown.
After completing this task, a floor hand secured the tugger to the starboard forward snubbing post, unknowingly catching the tugger wire in the aft HydraRacker guide jaw.
When the aft HydraRacker moved to complete the next job step, the tugger wire parted under tension, falling approximately 25 metres (83 feet) to the rig floor.
Operations were suspended and the tugger line inspected to verify there were no additional drops potential prior to securing the scene and reporting the incident.
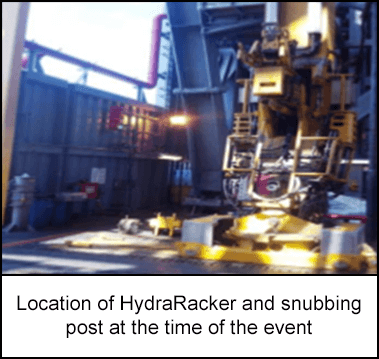
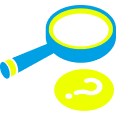
Why did it happen?
The incident was triggered by the inadvertent interaction between the tugger wire and the aft HydraRacker guide jaw.
This unintended collision was a result of the rig floor equipment's design and positioning, which led to the tugger wire being caught, resulting in its breakage.
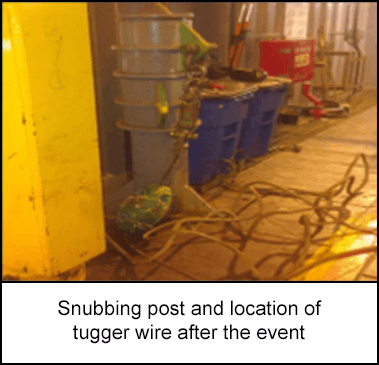
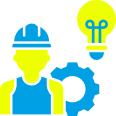
What did they learn?
The engineered design and location of equipment can introduce unintended interaction and potential for incident when in operation.
Revise and update the collision checklist to ensure it's actively used at suitable intervals.
Develop a 'No Parking' zone for the HydraRacker to prevent it being parked in the position where the tugger line is susceptible to being caught in the guide jaw.
Consider the installation of breakaway links between the tugger line hook and the securing point to mitigate potential event severity of a caught tugger wire.
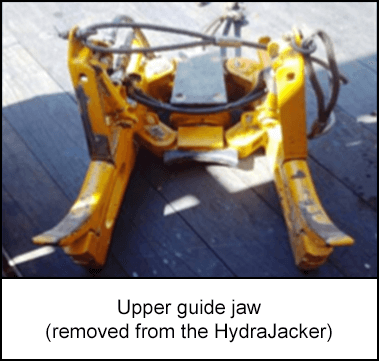
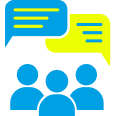
Ask yourself or your crew
How can something like this happen on our site?
How often do you evaluate the potential risks of collisions when you're positioning equipment on the rig floor? What specific steps or methods do you use to carry out these risk assessments?
What measures do you currently take to prevent entanglement between equipment, especially during tasks involving wire lines like the tugger?
Can you recall an instance where equipment positioning led to a close call or potential hazard? What were the circumstances, and how was it addressed?
How do you communicate with fellow crew members to ensure the safe positioning and movement of equipment during drilling operations?
How can we improve the rig floor safety protocols to prevent similar accidents from happening?
During drilling operations, as the crew pulled out of a wellbore and prepared the bottom-hole assembly for laydown, a tugger wire became entangled in the rig's equipment, causing it to snap under tension and fall to the rig floor.