-
What happened?
During a drilling operation, a reservoir section with an 8.5-inch (21.6 cm) diameter was drilled to a depth of 30,453 feet (9,282 metes) using 15.9 pounds per gallon (ppg) drilling, heavy emulsion mud weight (DHEMW), which is approximately 0.1198 metric tons per cubic meter (t/m³).
Due to an upcoming hurricane forecast, they decided to suspend operations using a storm packer.
Kick detection checks were performed, including a static one-hour flow check at the bottom.
The well was temporarily abandoned for the hurricane, and the rig was moved to safety.
An 18.5 ppg (2,217 kg/m³) riser cap was spotted.
After returning to the location, they ran the blowout preventer (BOP), displaced the riser to synthetic base mud (SBM), and confirmed the well’s static condition.
The kick was then circulated out using the driller’s method.
-
Why did it happen?
A swab kick occurred, affecting well stability.
Monitoring the mud weight was insufficient, leading to potential issues.
Fluid treatments introduced light spots in the active system, impacting well control.
The correlation between surface mud weights (measured manually) and bottom hole equivalent static densities (ESDs) was not consistently communicated to mud engineers and pit hands.
Post-kick investigation revealed varying surface mud weight values (ranging from 15.6 ppg to 15.4 ppg, which is approximately 0.1198 metric tons per cubic meter (t/m³)).
Later modular formation dynamics tester (MDT) measurements indicated a nearly balanced mud weight, possibly slightly underbalanced.
The tripping procedure was not properly implemented. Analysis highlighted early gains during flow checks that went unnoticed by the rig crew.
-
What did they learn?
For fluid system maintenance, oil / water ratio adjustments should be closely monitored and should be minimised as much as feasible when dealing with active treatments whilst drilling.
Reinforced mud weight measurements controls should be in place in critical intervals.
Rig mud engineers and pit hands should be periodically informed of ESD and mud weight in (MWin) / mud weight out (MWout) readings trends against requirements.
For rig tripping procedures, well displacement sheets should be regularly checked by drillers, mudlogging data analysts and drilling supervisors.
For well monitoring, MWin / MWout data should be added to the list of mudlogging data to be displayed and monitored by the mudlogging service, setting alarms accordingly to rapidly take corrective actions (±0.2ppg (±0.0024 t/m³)).
Pressure while drilling (PWD) alarms should be implemented indicating reduction / gain in hydrostatic pressure.
-
Ask yourself or your crew
How might better monitoring of mud weight have prevented potential issues and how can you ensure that effective levels of monitoring occur on our site?
What adjustments could be made to enhance communication between mud engineers and pit hands regarding ESDs and mud weight trends?
What specific aspects of the tripping procedure were not properly implemented in the incident? How can we learn from it?
What lessons can be learned from the early gains during flow checks that went unnoticed by the rig crew?
In our organisation, do we know what steps to take in the case of an extreme weather event, such as a hurricane, occurring during a procedure?
Add to homescreen
Content name
Select existing category:
Content name
New collection
Edit collection
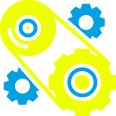
What happened?
During a drilling operation, a reservoir section with an 8.5-inch (21.6 cm) diameter was drilled to a depth of 30,453 feet (9,282 metes) using 15.9 pounds per gallon (ppg) drilling, heavy emulsion mud weight (DHEMW), which is approximately 0.1198 metric tons per cubic meter (t/m³).
Due to an upcoming hurricane forecast, they decided to suspend operations using a storm packer.
Kick detection checks were performed, including a static one-hour flow check at the bottom.
The well was temporarily abandoned for the hurricane, and the rig was moved to safety.
An 18.5 ppg (2,217 kg/m³) riser cap was spotted.
After returning to the location, they ran the blowout preventer (BOP), displaced the riser to synthetic base mud (SBM), and confirmed the well’s static condition.
The kick was then circulated out using the driller’s method.
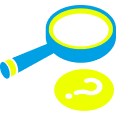
Why did it happen?
A swab kick occurred, affecting well stability.
Monitoring the mud weight was insufficient, leading to potential issues.
Fluid treatments introduced light spots in the active system, impacting well control.
The correlation between surface mud weights (measured manually) and bottom hole equivalent static densities (ESDs) was not consistently communicated to mud engineers and pit hands.
Post-kick investigation revealed varying surface mud weight values (ranging from 15.6 ppg to 15.4 ppg, which is approximately 0.1198 metric tons per cubic meter (t/m³)).
Later modular formation dynamics tester (MDT) measurements indicated a nearly balanced mud weight, possibly slightly underbalanced.
The tripping procedure was not properly implemented. Analysis highlighted early gains during flow checks that went unnoticed by the rig crew.
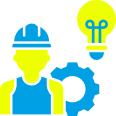
What did they learn?
For fluid system maintenance, oil / water ratio adjustments should be closely monitored and should be minimised as much as feasible when dealing with active treatments whilst drilling.
Reinforced mud weight measurements controls should be in place in critical intervals.
Rig mud engineers and pit hands should be periodically informed of ESD and mud weight in (MWin) / mud weight out (MWout) readings trends against requirements.
For rig tripping procedures, well displacement sheets should be regularly checked by drillers, mudlogging data analysts and drilling supervisors.
For well monitoring, MWin / MWout data should be added to the list of mudlogging data to be displayed and monitored by the mudlogging service, setting alarms accordingly to rapidly take corrective actions (±0.2ppg (±0.0024 t/m³)).
Pressure while drilling (PWD) alarms should be implemented indicating reduction / gain in hydrostatic pressure.
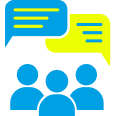
Ask yourself or your crew
How might better monitoring of mud weight have prevented potential issues and how can you ensure that effective levels of monitoring occur on our site?
What adjustments could be made to enhance communication between mud engineers and pit hands regarding ESDs and mud weight trends?
What specific aspects of the tripping procedure were not properly implemented in the incident? How can we learn from it?
What lessons can be learned from the early gains during flow checks that went unnoticed by the rig crew?
In our organisation, do we know what steps to take in the case of an extreme weather event, such as a hurricane, occurring during a procedure?
During a drilling operation, a reservoir section was drilled to a depth of 30,453 feet (9,282 meters) using 15.9 pounds per gallon (ppg) heavy emulsion mud weight (DHEMW), which is approximately 0.1198 metric tons per cubic meter (t/m³). Due to an upcoming hurricane forecast, operations were suspended using a storm packer. Kick detection checks were performed, and the well was temporarily abandoned for safety. An 18.5 ppg (2,217 kg/m³) riser cap was observed, and the kick was circulated out using the driller’s method.