-
What happened?
Two events occurred at the same facility associated with small bore piping failures resulting in a loss of primary containment.
Event 1: An operator identified a gas leak from a bleed valve on a relief path from a natural gas booster compressor via visual observation during operator rounds.
A leak clamp was installed on the cracked location and additional bracing installed to support the small bore piping.
The adjacent natural gas booster relief valves with similar small bore piping were also braced.
Event 2: One month later, an operator identified cracking on a different small bore piping connection, adjacent to the supporting gusset fillet weld.
Work was stopped in the vicinity and plant rates reduced.
Upon identification of the leak, the cold end of the plant was safely depressurised.
Calculations confirmed the second event resulted in a Tier 2 gas release.
The associated spool was removed from the location and a weld repair performed.
Spool was installed with additional bracing.
-
Why did it happen?
Vibration is considered to be a contributing factor that led to cracking.
-
What did they learn?
Conduct vibration monitoring campaign surveys to identify equipment subjected to vibration amplitudes.
Assess equipment vibration response at full operational rates (~100% plant rates).
Maintain a stock of easy-brace to help efficiently and effectively mitigate ad-hoc vibration threats when identified.
Develop a process for reporting, assessing and responding to concerns about potential vibration of equipment.
-
Ask yourself or your crew
Does your facility have small bore piping that could be subjected to vibration?
How do you check if small bore piping integrity could be affected by vibration?
Do you check vibration response of small bore piping during changes in plant conditions?
How would you report any vibration concerns that you identified?
Add to homescreen
Content name
Select existing category:
Content name
New collection
Edit collection
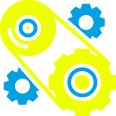
What happened?
Two events occurred at the same facility associated with small bore piping failures resulting in a loss of primary containment.
Event 1: An operator identified a gas leak from a bleed valve on a relief path from a natural gas booster compressor via visual observation during operator rounds.
A leak clamp was installed on the cracked location and additional bracing installed to support the small bore piping.
The adjacent natural gas booster relief valves with similar small bore piping were also braced.
Event 2: One month later, an operator identified cracking on a different small bore piping connection, adjacent to the supporting gusset fillet weld.
Work was stopped in the vicinity and plant rates reduced.
Upon identification of the leak, the cold end of the plant was safely depressurised.
Calculations confirmed the second event resulted in a Tier 2 gas release.
The associated spool was removed from the location and a weld repair performed.
Spool was installed with additional bracing.
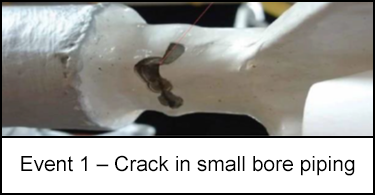
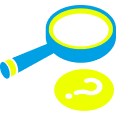
Why did it happen?
Vibration is considered to be a contributing factor that led to cracking.
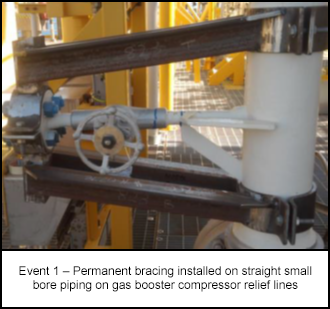
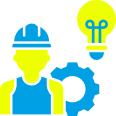
What did they learn?
Conduct vibration monitoring campaign surveys to identify equipment subjected to vibration amplitudes.
Assess equipment vibration response at full operational rates (~100% plant rates).
Maintain a stock of easy-brace to help efficiently and effectively mitigate ad-hoc vibration threats when identified.
Develop a process for reporting, assessing and responding to concerns about potential vibration of equipment.
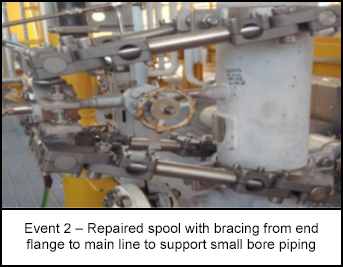
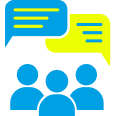
Ask yourself or your crew
Does your facility have small bore piping that could be subjected to vibration?
How do you check if small bore piping integrity could be affected by vibration?
Do you check vibration response of small bore piping during changes in plant conditions?
How would you report any vibration concerns that you identified?
Two small bore piping failures at a natural gas facility resulted in a loss of primary containment. The first incident involved a gas leak from a bleed valve, while the second, occurring a month later, involved cracking near a gusset fillet weld, leading to a Tier 2 gas release.
Original material courtesy of Safer Together (Australia)
To access the PDF and PowerPoint versions, please visit https://www.safertogether.com.au/resources/sharing-library/operating-process-equipment-loss-of-containment-leb-toolbox