-
What happened?
A fracturing (“frac”)/ wellhead assembly was lifted approximately half an inch to adjust a support (levelling jack) stand.
The lift was conducted using the horizontally-attached shouldered eyebolts on the equipment. The orientation of the eyebolts required an angular lift.
The lift took place and the eyebolt shanks sheared off. The wellhead equipment was secured and no other damage occurred.
-
Why did it happen?
The lift exceeded the angle load capacity which caused excessive strain on the eyebolts resulting in failure.
Angular lift significantly reduces lifting rated capacities.
-
What did they learn?
- Pre-plan each lift and understand engineering limitations of each component, including eyebolts.
- Before lifting, check with manufacturer specifications for rated load capacities and guidelines of eyebolt angle. Investigate appropriate methodology if using angled lifts. ie. safety swivel hoist rings.
- Shoulder eyebolts should not be used for angular lifts greater than 45o
- Before use, inspect eyebolts for damage or alterations (grinding, nicks, gouges, distortions, worn, bent, etc.).
- Check that eyebolts are stamped with name or trademark of manufacturer, size or capacity and grade. All information should be legible.
- Eyebolts should not be painted or otherwise coated when used for lifting; such coatings make it difficult to inspect for defects or wear indicators.
- Do not shock load eyebolts; use a gradual lift.
- No greater load should be applied to an eyebolt than the rated capacity.
-
Ask yourself or your crew
- How can we ensure that we are not exceeding the angle load capacity of the eyebolts when we lift?
- Are we ensuring that eyebolts are stamped with the name or trademark of the manufacturer, size or capacity, and grade?
- Are we using the correct type of eyebolt for the lifts we are performing?
- How do we inspect eyebolts for damage or alterations before use?
- What are some of the challenges you face in ensuring safe equipment lifting? What improvements or changes should we make?
Add to homescreen
If you want to add this app to home screen tap and then ‘Add to Home Screen’.
Content name
Select existing category:
Content name
New collection
Edit collection
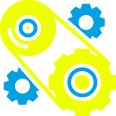
What happened?
A fracturing (“frac”)/ wellhead assembly was lifted approximately half an inch to adjust a support (levelling jack) stand.
The lift was conducted using the horizontally-attached shouldered eyebolts on the equipment. The orientation of the eyebolts required an angular lift.
The lift took place and the eyebolt shanks sheared off. The wellhead equipment was secured and no other damage occurred.

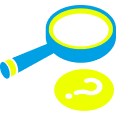
Why did it happen?
The lift exceeded the angle load capacity which caused excessive strain on the eyebolts resulting in failure.
Angular lift significantly reduces lifting rated capacities.
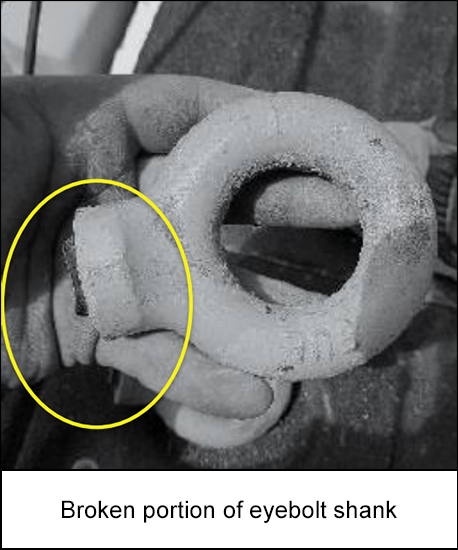
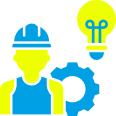
What did they learn?
- Pre-plan each lift and understand engineering limitations of each component, including eyebolts.
- Before lifting, check with manufacturer specifications for rated load capacities and guidelines of eyebolt angle. Investigate appropriate methodology if using angled lifts. ie. safety swivel hoist rings.
- Shoulder eyebolts should not be used for angular lifts greater than 45o
- Before use, inspect eyebolts for damage or alterations (grinding, nicks, gouges, distortions, worn, bent, etc.).
- Check that eyebolts are stamped with name or trademark of manufacturer, size or capacity and grade. All information should be legible.
- Eyebolts should not be painted or otherwise coated when used for lifting; such coatings make it difficult to inspect for defects or wear indicators.
- Do not shock load eyebolts; use a gradual lift.
- No greater load should be applied to an eyebolt than the rated capacity.
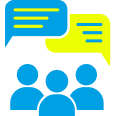
Ask yourself or your crew
- How can we ensure that we are not exceeding the angle load capacity of the eyebolts when we lift?
- Are we ensuring that eyebolts are stamped with the name or trademark of the manufacturer, size or capacity, and grade?
- Are we using the correct type of eyebolt for the lifts we are performing?
- How do we inspect eyebolts for damage or alterations before use?
- What are some of the challenges you face in ensuring safe equipment lifting? What improvements or changes should we make?
Published on 16/06/23
1204 Views
A fracturing/wellhead assembly was lifted to adjust a levelling jack stand. The lift was conducted using the horizontally attached shouldered eyebolts on the equipment. The orientation of the eyebolts required an angular lift. The lift took place and the eyebolt shanks sheared off.
Original material courtesy of Energy Safety Canada