-
What happened?
A site was placed on emergency shut down (ESD) due to a low flare pilot temperature.
When the site was reset, the well’s ESD valve did not open, blocking the flowline.
A worker saw the high tubing pressure (700 psig/4800 kPag) and began shutting the ratigans (rod blowout preventers (BOP)), to isolate the stuffing box, mitigating a spill.
The worker was alternating turns on the rams when the ratigan hammer cap failed.
The thread remained attached to the wellhead, but a damaged piece shot out and was found 20m from the wellhead.
The force of the release dislocated the worker’s right shoulder, but the worker was not in the line of fire of the damaged piece.
The tubing pressure bled off after 10 minutes releasing gas with trace amounts of oil.
-
Why did it happen?
Worker avoided being in the line of fire with correct body positioning.
Worker used correct technique for engaging the ratigans by alternating turns on the rams.
The ratigan hammer cap was made of cast iron – it would have been stronger if made of forged or cast steel.
-
What did they learn?
Identify why the ratigan hammer cap failed – work with technical experts and original equipment manufacturer.
Investigate the use of forged or cast steel instead of cast iron for future ratigan blowout preventers (BOPs).
Check the ratigans in use to make sure they are fit for purpose.
Confirm that all workers recognise the stored energy potential in hammer caps. Confirm workers are aware of the correct body positions and procedures.
Revisit the procedure guidelines for operating ratigan BOPs – how to recognise a stuck ram and what to do about it.
-
Ask yourself or your crew
Have you ever had experience of a ratigan hammer cap fail on your site?
What materials are our hammer caps made from?
How do you recognise a stuck ram?
What is the safe way to use a ratigan blowout preventer?
Add to homescreen
Content name
Select existing category:
Content name
New collection
Edit collection
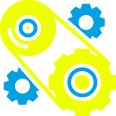
What happened?
A site was placed on emergency shut down (ESD) due to a low flare pilot temperature.
When the site was reset, the well’s ESD valve did not open, blocking the flowline.
A worker saw the high tubing pressure (700 psig/4800 kPag) and began shutting the ratigans (rod blowout preventers (BOP)), to isolate the stuffing box, mitigating a spill.
The worker was alternating turns on the rams when the ratigan hammer cap failed.
The thread remained attached to the wellhead, but a damaged piece shot out and was found 20m from the wellhead.
The force of the release dislocated the worker’s right shoulder, but the worker was not in the line of fire of the damaged piece.
The tubing pressure bled off after 10 minutes releasing gas with trace amounts of oil.
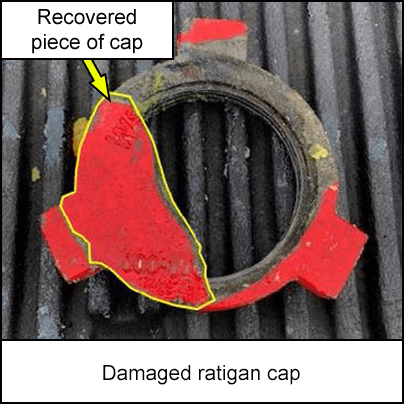
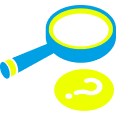
Why did it happen?
Worker avoided being in the line of fire with correct body positioning.
Worker used correct technique for engaging the ratigans by alternating turns on the rams.
The ratigan hammer cap was made of cast iron – it would have been stronger if made of forged or cast steel.
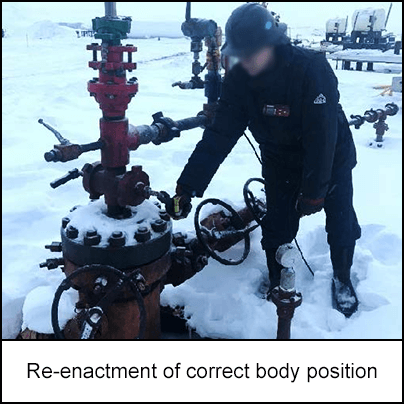
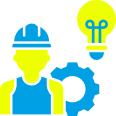
What did they learn?
Identify why the ratigan hammer cap failed – work with technical experts and original equipment manufacturer.
Investigate the use of forged or cast steel instead of cast iron for future ratigan blowout preventers (BOPs).
Check the ratigans in use to make sure they are fit for purpose.
Confirm that all workers recognise the stored energy potential in hammer caps. Confirm workers are aware of the correct body positions and procedures.
Revisit the procedure guidelines for operating ratigan BOPs – how to recognise a stuck ram and what to do about it.
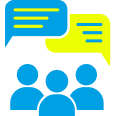
Ask yourself or your crew
Have you ever had experience of a ratigan hammer cap fail on your site?
What materials are our hammer caps made from?
How do you recognise a stuck ram?
What is the safe way to use a ratigan blowout preventer?
A worker on a well was shutting the rod ratigans when the ratigan hammer cap failed, and the pressure of the blowout dislocated their shoulder.