-
What happened?
A pressure safety valve (PSV) located at the injection compressor discharge and connected to the flare was observed leaking.
An operator decided to reseat it by closing the upstream isolation valve (this would avoid the need to dismantle it).
He mistakenly closed the downstream instead of the upstream valve. This led to over pressurisation and a failure of the pipe network. The subsequent burst killed the operator.
The flare network was damaged, and an unknown volume of gas was released to atmosphere.
-
Why did it happen?
The operator closed the downstream block valve before closing upstream block valve.
The pressure safety valve was passing, which allowed 300 barg gas into a system rated for 36 barg. System burst at approximately 120 barg.
PSVs were not physically locked open (which would prevent movement). There was no locked open/locked closed (LO/LC) system implemented on-site, allowing operator to move valves without warning.
Valve movement was conducted without formal work authorisation and procedure.
Lack of awareness of operator on high pressure/low pressure (HP/LP) pipe interface.
There was a desire to keep the leaking PSV in operation to avoid a compressor shutdown.
-
What did they learn?
Check and replace all leaking PSVs on-site.
All valves LO/LC defined on piping and instrumentation diagrams (PIDs) should be clearly identified on site. Locking devices should be installed.
Consistency between locking positions on site and PIDs should be checked at least every 3 months and after major site interventions.
Each operating site should ensure it has a procedure detailing all steps to swap on-line PSVs, and a procedure to isolate PSVs fully for intervention scope.
Check and validate upstream isolation valve tightness before closing downstream isolation valve.
Each isolation valve installed downstream of a PSV should be kept locked open except when maintenance or inspection activity has been authorised.
-
Ask yourself or your crew
How can something like this happen here?
Have you observed any systems or equipment not working properly (leaking etc.)? What is the process for reporting and replacing it?
Do we have a locked open/locked closed (LO/LC) system in place?
- Have we installed locking devices on all the valves defined in the piping and instrumentation diagrams (PIDs)?
- How can we make sure the system is effective?
What procedures do you have to follow when working on pressure safety valves? How can we improve these to make your work safer?
Add to homescreen
Content name
Select existing category:
Content name
New collection
Edit collection
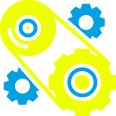
What happened?
A pressure safety valve (PSV) located at the injection compressor discharge and connected to the flare was observed leaking.
An operator decided to reseat it by closing the upstream isolation valve (this would avoid the need to dismantle it).
He mistakenly closed the downstream instead of the upstream valve. This led to over pressurisation and a failure of the pipe network. The subsequent burst killed the operator.
The flare network was damaged, and an unknown volume of gas was released to atmosphere.
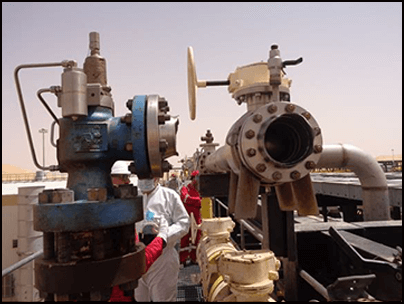
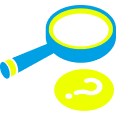
Why did it happen?
The operator closed the downstream block valve before closing upstream block valve.
The pressure safety valve was passing, which allowed 300 barg gas into a system rated for 36 barg. System burst at approximately 120 barg.
PSVs were not physically locked open (which would prevent movement). There was no locked open/locked closed (LO/LC) system implemented on-site, allowing operator to move valves without warning.
Valve movement was conducted without formal work authorisation and procedure.
Lack of awareness of operator on high pressure/low pressure (HP/LP) pipe interface.
There was a desire to keep the leaking PSV in operation to avoid a compressor shutdown.
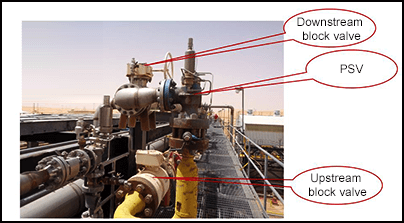
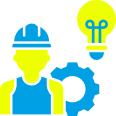
What did they learn?
Check and replace all leaking PSVs on-site.
All valves LO/LC defined on piping and instrumentation diagrams (PIDs) should be clearly identified on site. Locking devices should be installed.
Consistency between locking positions on site and PIDs should be checked at least every 3 months and after major site interventions.
Each operating site should ensure it has a procedure detailing all steps to swap on-line PSVs, and a procedure to isolate PSVs fully for intervention scope.
Check and validate upstream isolation valve tightness before closing downstream isolation valve.
Each isolation valve installed downstream of a PSV should be kept locked open except when maintenance or inspection activity has been authorised.
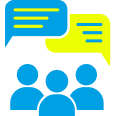
Ask yourself or your crew
How can something like this happen here?
Have you observed any systems or equipment not working properly (leaking etc.)? What is the process for reporting and replacing it?
Do we have a locked open/locked closed (LO/LC) system in place?
- Have we installed locking devices on all the valves defined in the piping and instrumentation diagrams (PIDs)?
- How can we make sure the system is effective?
What procedures do you have to follow when working on pressure safety valves? How can we improve these to make your work safer?
An operator mistakenly closed the downstream instead of the upstream valve when working on a system. This led to over pressurisation and a failure of the pipe network. The subsequent burst killed the operator.