-
What happened?
A coiled tubing crew was conducting pressure tests of the blowout preventer.
Following a successful low pressure test at 10 Megapascals (MPa) the line was bled down through two-inch diameter blowback piping to an open-top tank. This pressure was bled off without issue, confirming that the line was free of obstructions.
At this time, a high-pressure test was conducted at 55 MPa. When the valve was feathered open to bleed off the pressure, a loud bang was heard, and the piping parted.
Several workers were in the vicinity of the flying debris, but nobody was injured.
-
Why did it happen?
The blowback piping was over pressurized.
It was rated for 14 MPa and because it was vented to atmosphere, it was believed that the risk of an overpressure event was low.
-
What did they learn?
- The blow-down procedure was modified to step down the pressure from the high-pressure test before going to the blowback piping.
- A pressure transducer was installed on the blowback piping to monitor the line pressure. This has since indicated that overpressure events were likely occurring frequently.
- A pressure safety valve was installed on the blowback piping.
- Piping restraints were added to the blowback lines.
- Equipment layout was modified to shield the manifold operator from the blowback piping.
-
Ask yourself or your crew
- How can something like this happen here (e.g. on our site)?
- What safety measures (i.e. procedures, controls/barriers) do we have in place to mitigate the risk?
- How do we know the risk controls/barriers are working?
- What improvements or changes should we make to the procedures, controls/barriers or the way we work?
Add to homescreen
If you want to add this app to home screen tap and then ‘Add to Home Screen’.
Content name
Select existing category:
Content name
New collection
Edit collection
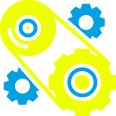
What happened?
A coiled tubing crew was conducting pressure tests of the blowout preventer.
Following a successful low pressure test at 10 Megapascals (MPa) the line was bled down through two-inch diameter blowback piping to an open-top tank. This pressure was bled off without issue, confirming that the line was free of obstructions.
At this time, a high-pressure test was conducted at 55 MPa. When the valve was feathered open to bleed off the pressure, a loud bang was heard, and the piping parted.
Several workers were in the vicinity of the flying debris, but nobody was injured.
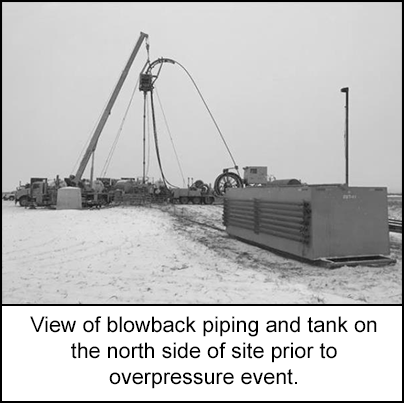
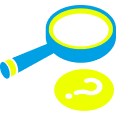
Why did it happen?
The blowback piping was over pressurized.
It was rated for 14 MPa and because it was vented to atmosphere, it was believed that the risk of an overpressure event was low.
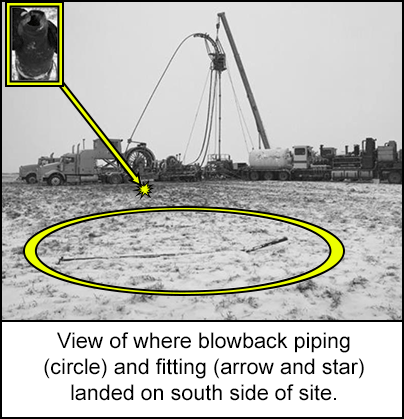
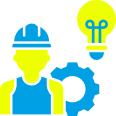
What did they learn?
- The blow-down procedure was modified to step down the pressure from the high-pressure test before going to the blowback piping.
- A pressure transducer was installed on the blowback piping to monitor the line pressure. This has since indicated that overpressure events were likely occurring frequently.
- A pressure safety valve was installed on the blowback piping.
- Piping restraints were added to the blowback lines.
- Equipment layout was modified to shield the manifold operator from the blowback piping.
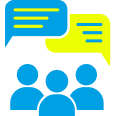
Ask yourself or your crew
- How can something like this happen here (e.g. on our site)?
- What safety measures (i.e. procedures, controls/barriers) do we have in place to mitigate the risk?
- How do we know the risk controls/barriers are working?
- What improvements or changes should we make to the procedures, controls/barriers or the way we work?
Published on 05/04/23
1579 Views
A coiled tubing crew was conducting pressure tests of the blowout preventer. Following a successful low-pressure test, the line was bled down through blowback piping and a high-pressure test was conducted. When the valve was feathered open to bleed off the pressure, a loud bang was heard, and the piping parted. Several workers were in the vicinity of the flying debris, but nobody was injured.
Original material courtesy of Energy Safety Canada
Other industry resources:
Potentially Serious Incidents Program
Process Safety: A Barrier Focused Approach Process
Safety Posters
IOGP Process Safety Fundamentals
Are You in the Line of Fire? Program
Life Saving Rules
DACC IRP Volume #21 - Coiled Tubing Operations