-
What happened?
During the process of lifting a gas cylinder cage from the forward machinery area of the floating storage and offloading (FSO) using the main deck hatch, one of the two 'G' size nitrogen gas cylinders accidentally slipped from the lower back section of the cage, falling 17 metres (55 feet) to the third deck in the forward machinery space.
The impact ruptured the neck of the cylinder, causing the pressurised contents to release and propelling the cylinder within the confines of the lifting zone on the third deck.
Fortunately, no injuries were sustained.
-
Why did it happen?
The cage design has been identified as flawed due to the potential for inadequately secured cylinders of “G”, “D”, and “E” size to move through the cage opening on the sides and the rear.
The gas cylinder cages were vendor supplied and approved cages for use with their cylinders. However, the internal lashing configuration does not support various size cylinders.
A 415mm (16 inch) gap from the floor of the cage to the first rail was high enough to allow a cylinder to slip through.
Due to vessel movement and narrow deck openings on the FSO, lifts can contact deck hatches when being lifted by the crane.
There were two previous near miss incidents that emphasised the use of administrative controls. These controls included a safety stand down and a safety alert. After the first incident occurred, the supply base investigated the possibility of redesigning the cage. However, the vendor's response to address the issues was limited.
-
What did they learn?
If you are using this type of cage, discontinue usage and seek out new cages for trial that are engineered to ensure cylinders can’t slip out if rigging becomes loose during lifting/transportation.
Share lessons learned with vendor to make them aware of the hazards with their cage design.
Share lessons learned internally and externally to help prevent similar incidents.
-
Ask yourself or your crew
How can this, or a similar situation, happen in your workplace?
How robust are your critical controls around lifting i.e. barricading to prevent someone walking under a suspended load? Exemplify.
Which of your lifting operations could potentially benefit from replacing any existing administrative controls with engineered controls?
What measures do we have in place to prevent something like this happening here? How can we improve our processes to minimise risk?
Add to homescreen
Content name
Select existing category:
Content name
New collection
Edit collection
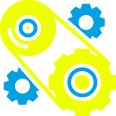
What happened?
During the process of lifting a gas cylinder cage from the forward machinery area of the floating storage and offloading (FSO) using the main deck hatch, one of the two 'G' size nitrogen gas cylinders accidentally slipped from the lower back section of the cage, falling 17 metres (55 feet) to the third deck in the forward machinery space.
The impact ruptured the neck of the cylinder, causing the pressurised contents to release and propelling the cylinder within the confines of the lifting zone on the third deck.
Fortunately, no injuries were sustained.
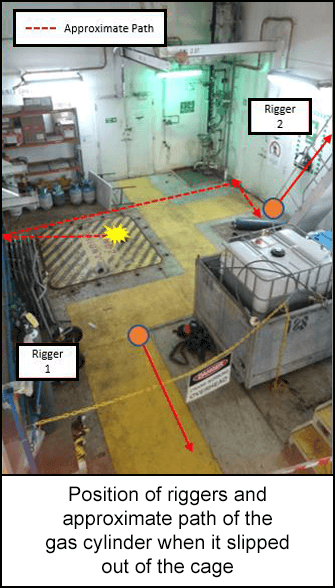
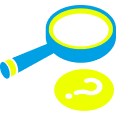
Why did it happen?
The cage design has been identified as flawed due to the potential for inadequately secured cylinders of “G”, “D”, and “E” size to move through the cage opening on the sides and the rear.
The gas cylinder cages were vendor supplied and approved cages for use with their cylinders. However, the internal lashing configuration does not support various size cylinders.
A 415mm (16 inch) gap from the floor of the cage to the first rail was high enough to allow a cylinder to slip through.
Due to vessel movement and narrow deck openings on the FSO, lifts can contact deck hatches when being lifted by the crane.
There were two previous near miss incidents that emphasised the use of administrative controls. These controls included a safety stand down and a safety alert. After the first incident occurred, the supply base investigated the possibility of redesigning the cage. However, the vendor's response to address the issues was limited.
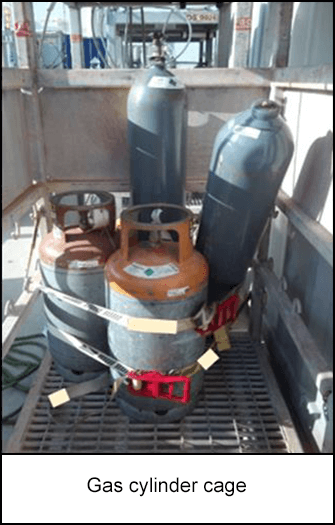
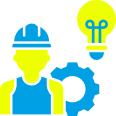
What did they learn?
If you are using this type of cage, discontinue usage and seek out new cages for trial that are engineered to ensure cylinders can’t slip out if rigging becomes loose during lifting/transportation.
Share lessons learned with vendor to make them aware of the hazards with their cage design.
Share lessons learned internally and externally to help prevent similar incidents.
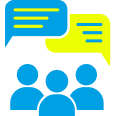
Ask yourself or your crew
How can this, or a similar situation, happen in your workplace?
How robust are your critical controls around lifting i.e. barricading to prevent someone walking under a suspended load? Exemplify.
Which of your lifting operations could potentially benefit from replacing any existing administrative controls with engineered controls?
What measures do we have in place to prevent something like this happening here? How can we improve our processes to minimise risk?
During the process of lifting a gas cylinder cage from the forward machinery area of the floating storage and offloading (FSO) using the main deck hatch, one of the two nitrogen gas cylinders accidentally slipped from the lower back section of the cage, falling 17 metres (55 feet) to the third deck in the forward machinery space. Fortunately, no injuries were sustained.