-
What happened?
Microbiologically influenced corrosion (MIC) is corrosion caused by the presence and activities of micro-organisms (a.k.a. “bugs”), which can facilitate, initiate or accelerate corrosion of metals and alloys.
This corrosion has resulted in potential and actual loss of containment in plant and equipment used to transport or store hydrocarbons.
-
Why did it happen?
It is not practical to prevent equipment from coming in contact with bacteria that can cause MIC.
Once present, bacteria are very difficult to eliminate and can lay dormant until a suitable environment exists.
- The “bugs” live in the water phase and are often anaerobic so don’t require oxygen to survive.
- Corrosion rates can be high (millimetres per year).
- Corrosion locations can be unpredictable and highly localised.
- Bugs thrive in many different conditions, but often have preferred habitats:
- pH 4-9
- Warmer temperature
- In the presence of water and nutrients
-
What did they learn?
Consider impact from MIC in design of plant and equipment (material selection, design-out dead-legs etc.) and do not rely on operate phase controls.
Review preservation strategy and select suitable inspection techniques to control MIC risk (particularly for temporary equipment integrity).
Assess MIC risk in risk based inspections (RBI) throughout the operating life of infrastructure and equipment, including known idle periods, and consider equipment general arrangement and piping isometrics.
As MIC may be highly localised, use inspection techniques that are most likely to detect the damage caused by this mechanism (i.e. ultrasonic testing is less effective, radiography is more effective). Use targeted radiography and API 579 Fitness for service assessments where applicable.
Pressure testing at working pressure prior to operation may mask an imminent pinhole leak. Consider testing at higher pressures.
-
Ask yourself or your crew
What factors contribute to your equipment’s susceptibility to microbiologically influenced corrosion (MIC)? In what ways does your maintenance and inspection program evaluate the risks associated with MIC?
What testing techniques do you use to detect damage caused by MIC?
How does your maintenance and inspection program ensure equipment integrity throughout all lifecycle stages, including periods of idleness or preservation?
Add to homescreen
Content name
Select existing category:
Content name
New collection
Edit collection
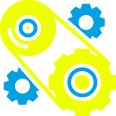
What happened?
Microbiologically influenced corrosion (MIC) is corrosion caused by the presence and activities of micro-organisms (a.k.a. “bugs”), which can facilitate, initiate or accelerate corrosion of metals and alloys.
This corrosion has resulted in potential and actual loss of containment in plant and equipment used to transport or store hydrocarbons.
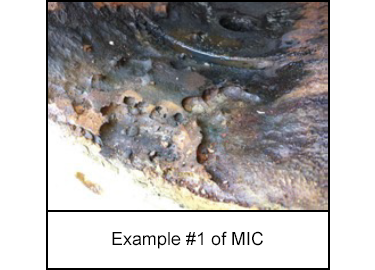
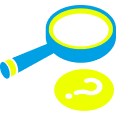
Why did it happen?
It is not practical to prevent equipment from coming in contact with bacteria that can cause MIC.
Once present, bacteria are very difficult to eliminate and can lay dormant until a suitable environment exists.
- The “bugs” live in the water phase and are often anaerobic so don’t require oxygen to survive.
- Corrosion rates can be high (millimetres per year).
- Corrosion locations can be unpredictable and highly localised.
- Bugs thrive in many different conditions, but often have preferred habitats:
- pH 4-9
- Warmer temperature
- In the presence of water and nutrients
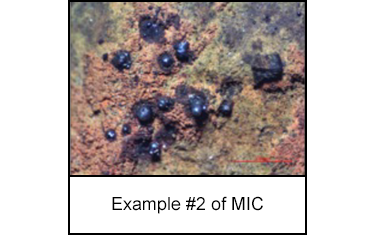
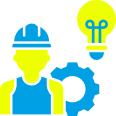
What did they learn?
Consider impact from MIC in design of plant and equipment (material selection, design-out dead-legs etc.) and do not rely on operate phase controls.
Review preservation strategy and select suitable inspection techniques to control MIC risk (particularly for temporary equipment integrity).
Assess MIC risk in risk based inspections (RBI) throughout the operating life of infrastructure and equipment, including known idle periods, and consider equipment general arrangement and piping isometrics.
As MIC may be highly localised, use inspection techniques that are most likely to detect the damage caused by this mechanism (i.e. ultrasonic testing is less effective, radiography is more effective). Use targeted radiography and API 579 Fitness for service assessments where applicable.
Pressure testing at working pressure prior to operation may mask an imminent pinhole leak. Consider testing at higher pressures.
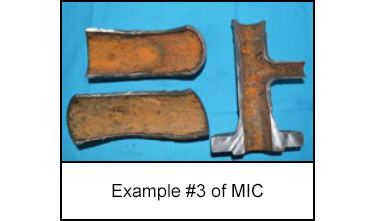
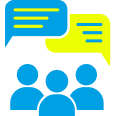
Ask yourself or your crew
What factors contribute to your equipment’s susceptibility to microbiologically influenced corrosion (MIC)? In what ways does your maintenance and inspection program evaluate the risks associated with MIC?
What testing techniques do you use to detect damage caused by MIC?
How does your maintenance and inspection program ensure equipment integrity throughout all lifecycle stages, including periods of idleness or preservation?
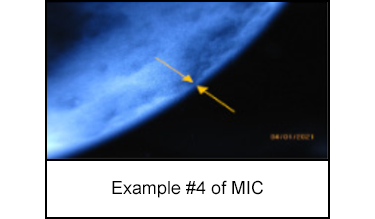
Microbiologically influenced corrosion (MIC) is caused by bacterial activity, leading to unpredictable and localized damage to hydrocarbon transport and storage equipment. This corrosion poses a significant risk of containment loss in industrial systems.
Original material courtesy of Safer Together (Australia)
To access the PDF and PowerPoint versions, please visit https://www.safertogether.com.au/resources/sharing-library/operating-process-equipment-loss-of-containment