-
What happened?
During a routine start of shift orientation, a central processing plant operator heard a loud hissing noise near a reciprocating compressor discharge bottle.
A methane gas leak was detected, originating from around the tube fitting of the pressure transmitter’s impulse line.
The unit was shut down and tubing removed for replacement.
-
Why did it happen?
The failure mode of the stainless-steel tubing was vibration-induced fatigue.
A few weeks prior to failure, the vibration was assessed by a vibration monitoring contractor and the tubing vibration levels were not deemed to be severe based on the classification from industry good practice guidelines.
The investigation revealed several key causal / contributing factors:
Small bore tube routing did not comply with optimised tube routing as per industry good practice guidelines followed. The routing that existed was susceptible to high vibration.
The guidelines for tubing provide a qualitative visual approach for vibration risk assessment (unlike for process piping). There are no known industry standards that provide vibration limits for instrument tubing.
The thickness of the tubing used was less than the minimum allowable thickness for impulse lines.
There was a notable increase in frequency of the reciprocating compressor operating at lower speeds in the 6 – 12 months prior to failure. The compressor historically operated at fixed speeds for most of the time. Change of speeds resulted in a change of vibration driving forces.
-
What did they learn?
The routing and thin wall of the tubing increased the susceptibility of the impulse line to fatigue failure.
The vibration risk was not fully captured during routine vibration surveys because tubing vibration is only visually assessed.
The vibration risk of package piping and tubing needed to be assessed at lower speeds.
-
Ask yourself or your crew
How do you ensure that tubing installations, especially for impulse lines, are routed according to industry good practice guidelines to minimise vibration risks?
What steps do you take to verify that the tubing and fittings used meet minimum allowable thickness requirements?
How do you check if small bore tubing and piping integrity could be affected by vibration?
How do you account for variable operating speeds of equipment, like reciprocating compressors, when assessing vibration risks?
How would you report any vibration concerns that you identified?
Add to homescreen
Content name
Select existing category:
Content name
New collection
Edit collection
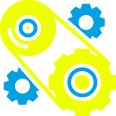
What happened?
During a routine start of shift orientation, a central processing plant operator heard a loud hissing noise near a reciprocating compressor discharge bottle.
A methane gas leak was detected, originating from around the tube fitting of the pressure transmitter’s impulse line.
The unit was shut down and tubing removed for replacement.
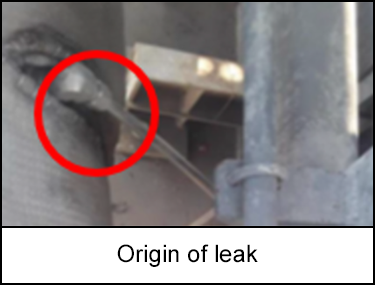
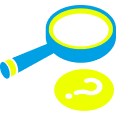
Why did it happen?
The failure mode of the stainless-steel tubing was vibration-induced fatigue.
A few weeks prior to failure, the vibration was assessed by a vibration monitoring contractor and the tubing vibration levels were not deemed to be severe based on the classification from industry good practice guidelines.
The investigation revealed several key causal / contributing factors:
Small bore tube routing did not comply with optimised tube routing as per industry good practice guidelines followed. The routing that existed was susceptible to high vibration.
The guidelines for tubing provide a qualitative visual approach for vibration risk assessment (unlike for process piping). There are no known industry standards that provide vibration limits for instrument tubing.
The thickness of the tubing used was less than the minimum allowable thickness for impulse lines.
There was a notable increase in frequency of the reciprocating compressor operating at lower speeds in the 6 – 12 months prior to failure. The compressor historically operated at fixed speeds for most of the time. Change of speeds resulted in a change of vibration driving forces.
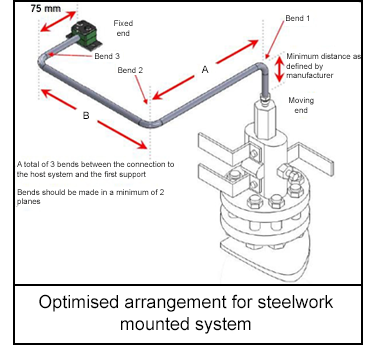
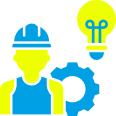
What did they learn?
The routing and thin wall of the tubing increased the susceptibility of the impulse line to fatigue failure.
The vibration risk was not fully captured during routine vibration surveys because tubing vibration is only visually assessed.
The vibration risk of package piping and tubing needed to be assessed at lower speeds.
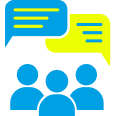
Ask yourself or your crew
How do you ensure that tubing installations, especially for impulse lines, are routed according to industry good practice guidelines to minimise vibration risks?
What steps do you take to verify that the tubing and fittings used meet minimum allowable thickness requirements?
How do you check if small bore tubing and piping integrity could be affected by vibration?
How do you account for variable operating speeds of equipment, like reciprocating compressors, when assessing vibration risks?
How would you report any vibration concerns that you identified?
During a routine shift orientation, a central processing plant operator detected a methane gas leak from a tube fitting near a compressor. The unit was promptly shut down, and the faulty tubing was replaced to prevent any hazards.
Original material courtesy of Safer Together (Australia)
To access the PDF and PowerPoint versions, please visit https://www.safertogether.com.au/resources/sharing-library/operating-process-equipment-loss-of-containment-apr-2023