-
What happened?
There have been a number of incidents involving uninterruptible power supply (UPS) systems:
- Failure of UPS systems led to loss of power to industrial control systems, emergency shutdown systems and emergency mitigation systems.
- In one incident, there was a fire within the UPS system itself, with the smoke and excessive heat then damaging the static switch mechanism, leading to failure of the second backup UPS system to provide emergency power.
- Component failures and outdated firmware have led to the unplanned shutdown of a chemical processing plant. On start-up, there was an unplanned release of toxic substances into the environment, and additional demand placed upon other safety related systems.
Fortunately, no employees, contractors, or members of the public were injured in any of these incidents.
-
Why did it happen?
UPS systems were from a variety of original equipment manufacturers (OEMs), yet in all cases the operation and maintenance instructions provided by the OEM were inadequate. For example, not providing a suitable maintenance regime.
End users’ information was ‘out of date’ and didn’t reflect real world experience in operating the UPS systems. For example, some components had much shorter life expectancies than initially predicted.
End users were not made aware of design changes or limitations on use that have a safety implication. For example, firmware upgrades might become essential to ensure continued reliability.
Sales literature typically stated that the design life of the UPS systems is between 15 to 20 years, but in reality, many components will need to be replaced much sooner (such as batteries, filter capacitors, cooling fans, internal RAM batteries, power cards and control cards). Operating and maintenance instructions typically did not specify this, leading to inadequate maintenance schedules and a false sense of safety and reliability by end users.
-
What did they learn?
Where an industrial UPS system is installed to provide emergency power, a failure of the industrial UPS system could result in a serious risk to health and safety.
End users and specialist maintenance contractors:
- Ensure that you have access to the latest revision of information for maintenance from the OEM. Use this information to update existing maintenance arrangements and ensure that the UPS system is being maintained accordingly.
Designers, manufacturers, importers, and suppliers:
- Review the information for maintenance (including inspection) you provide to ensure that it satisfies legal requirements.
- Review information for maintenance provided historically to all end users and determine if you need to provide more up to date information (based on experience in use, design modifications, limitations on use or anything else that gives risk to a serious risk to health and safety).
- Following this review, take steps to ensure that all affected end users are provided with all revisions of information to assure safe and reliable continued operation.
-
Ask yourself or your crew
Do we have a UPS system?
What could happen if it failed?
How do we know if won’t fail?
How do we know that the information on operation and maintenance is up to date?
What changes can we make as a result of this discussion?
Add to homescreen
Content name
Select existing category:
Content name
New collection
Edit collection
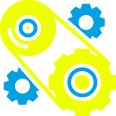
What happened?
There have been a number of incidents involving uninterruptible power supply (UPS) systems:
- Failure of UPS systems led to loss of power to industrial control systems, emergency shutdown systems and emergency mitigation systems.
- In one incident, there was a fire within the UPS system itself, with the smoke and excessive heat then damaging the static switch mechanism, leading to failure of the second backup UPS system to provide emergency power.
- Component failures and outdated firmware have led to the unplanned shutdown of a chemical processing plant. On start-up, there was an unplanned release of toxic substances into the environment, and additional demand placed upon other safety related systems.
Fortunately, no employees, contractors, or members of the public were injured in any of these incidents.
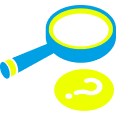
Why did it happen?
UPS systems were from a variety of original equipment manufacturers (OEMs), yet in all cases the operation and maintenance instructions provided by the OEM were inadequate. For example, not providing a suitable maintenance regime.
End users’ information was ‘out of date’ and didn’t reflect real world experience in operating the UPS systems. For example, some components had much shorter life expectancies than initially predicted.
End users were not made aware of design changes or limitations on use that have a safety implication. For example, firmware upgrades might become essential to ensure continued reliability.
Sales literature typically stated that the design life of the UPS systems is between 15 to 20 years, but in reality, many components will need to be replaced much sooner (such as batteries, filter capacitors, cooling fans, internal RAM batteries, power cards and control cards). Operating and maintenance instructions typically did not specify this, leading to inadequate maintenance schedules and a false sense of safety and reliability by end users.
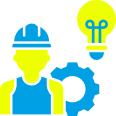
What did they learn?
Where an industrial UPS system is installed to provide emergency power, a failure of the industrial UPS system could result in a serious risk to health and safety.
End users and specialist maintenance contractors:
- Ensure that you have access to the latest revision of information for maintenance from the OEM. Use this information to update existing maintenance arrangements and ensure that the UPS system is being maintained accordingly.
Designers, manufacturers, importers, and suppliers:
- Review the information for maintenance (including inspection) you provide to ensure that it satisfies legal requirements.
- Review information for maintenance provided historically to all end users and determine if you need to provide more up to date information (based on experience in use, design modifications, limitations on use or anything else that gives risk to a serious risk to health and safety).
- Following this review, take steps to ensure that all affected end users are provided with all revisions of information to assure safe and reliable continued operation.
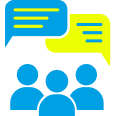
Ask yourself or your crew
Do we have a UPS system?
What could happen if it failed?
How do we know if won’t fail?
How do we know that the information on operation and maintenance is up to date?
What changes can we make as a result of this discussion?
Where an industrial uninterruptible power supply (UPS) system is installed to provide emergency power, a failure of the industrial UPS system could result in a serious risk to health and safety. In some instances, failure of UPS systems led to loss of power to industrial control systems, emergency shutdown systems and emergency mitigation systems.
Source: HSE Safety Alerts