-
What happened?
A worker was cleaning a tank, which involved entering the tank and using an external air supply.
While in the tank, the air supply stopped, and the reserve tank ran out of air without being detected.
The person immediately got out and there were no injuries.
The alarm was triggered but the guards did not hear it due to high noise levels in the area.
-
Why did it happen?
A fault caused an air compressor to stop and switch to backup air.
The alarm signal could not be distinguished from the noise in the area and was not heard. This was not identified as a risk.
The alarm panel on the air compressor was not continuously monitored, as it was trusted that the sound signal was sufficient.
There were no established requirements for documented training.
The unit did not have the opportunity to test that the alarm worked, and there was no secondary independent barrier.
-
What did they learn?
Clarify requirements in governing documentation for monitoring air compressors.
Consider speaking to the manufacturer to improve design or use another model that provides a light signal in addition to the audio signal.
Ensure that personnel are trained and understand the risks associated with their activities. Contractors should ensure they are trained for use of third-party equipment and understand the risks.
Review procedures and design for use for all fixed and removable air compressors in use.
-
Ask yourself or your crew
How can something like this happen here (e.g. at our site)?
What measures can we implement to improve the effectiveness of alarms in high-noise environments, considering the challenges faced in detecting the alarm signal during the incident?
What specific training protocols should be established to ensure all personnel, including contractors, are adequately trained to operate equipment and understand associated risks?
How can we enhance our procedures and design for the use of fixed and removable air compressors to mitigate the risk of similar incidents occurring in the future?
What other risks are associated with cleaning activities in confined spaces?
Add to homescreen
Content name
Select existing category:
Content name
New collection
Edit collection
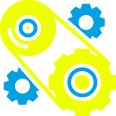
What happened?
A worker was cleaning a tank, which involved entering the tank and using an external air supply.
While in the tank, the air supply stopped, and the reserve tank ran out of air without being detected.
The person immediately got out and there were no injuries.
The alarm was triggered but the guards did not hear it due to high noise levels in the area.
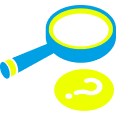
Why did it happen?
A fault caused an air compressor to stop and switch to backup air.
The alarm signal could not be distinguished from the noise in the area and was not heard. This was not identified as a risk.
The alarm panel on the air compressor was not continuously monitored, as it was trusted that the sound signal was sufficient.
There were no established requirements for documented training.
The unit did not have the opportunity to test that the alarm worked, and there was no secondary independent barrier.
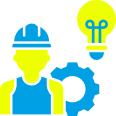
What did they learn?
Clarify requirements in governing documentation for monitoring air compressors.
Consider speaking to the manufacturer to improve design or use another model that provides a light signal in addition to the audio signal.
Ensure that personnel are trained and understand the risks associated with their activities. Contractors should ensure they are trained for use of third-party equipment and understand the risks.
Review procedures and design for use for all fixed and removable air compressors in use.
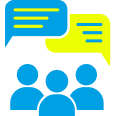
Ask yourself or your crew
How can something like this happen here (e.g. at our site)?
What measures can we implement to improve the effectiveness of alarms in high-noise environments, considering the challenges faced in detecting the alarm signal during the incident?
What specific training protocols should be established to ensure all personnel, including contractors, are adequately trained to operate equipment and understand associated risks?
How can we enhance our procedures and design for the use of fixed and removable air compressors to mitigate the risk of similar incidents occurring in the future?
What other risks are associated with cleaning activities in confined spaces?
A worker was cleaning a tank, which involved entering the tank and using an external air supply. While in the tank, the air supply stopped, and the reserve tank ran out of air without being detected. The person immediately got out and there were no injuries. The alarm was triggered but the guards did not hear it due to high noise levels in the area.