-
What happened?
A truck carrying a load of cardboard cartons arrived at a regional supply base.
Each carton weighed about 22kg (49lbs). The total load weighed approximately 470kg (1,036lbs).
Upon arrival at the supply base it was noticed that the load had shifted during transit, with cartons partially spread across the deck of the trailer.
No cartons fell from the trailer.
-
Why did it happen?
Goods were not adequately restrained onto the pallets with strapping.
This could not be seen due to the use of black plastic wrap. The wrap failed in transit.
Gates to provide additional containment on the truck were not used.
The quality of the pallets was poor.
The angle of lashing delivered poor clamping force.
High centre of gravity.
-
What did they learn?
Ensure that packaging complies with local packaging, handling and movement of materials specifications.
Use clear shrink wrap so that constraints can be seen.
Reduce the height of the load to achieve a lower centre of gravity.
Ensure the load is positioned central to the trailer deck or next to pallets the same height, so that adequate clamping force can be applied with lashings.
Carry out load restraint checks at the point of load.
Consult with all parties involved in the chain of responsibility to ensure that robust means of securing loads are used. Source pallets that are suitable for recirculating through the supply chain.
-
Ask yourself or your crew
Are you involved in securing or transporting loads via road?
Are you aware of local packaging, handling and movement of materials specifications? Do you understand its requirements?
How do you assess the suitability of load restraints?
What is your role in the chain of responsibility?
Add to homescreen
Content name
Select existing category:
Content name
New collection
Edit collection
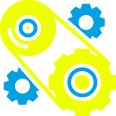
What happened?
A truck carrying a load of cardboard cartons arrived at a regional supply base.
Each carton weighed about 22kg (49lbs). The total load weighed approximately 470kg (1,036lbs).
Upon arrival at the supply base it was noticed that the load had shifted during transit, with cartons partially spread across the deck of the trailer.
No cartons fell from the trailer.
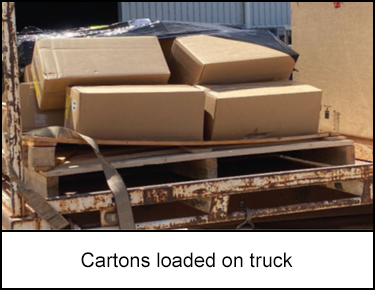
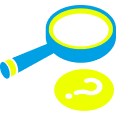
Why did it happen?
Goods were not adequately restrained onto the pallets with strapping.
This could not be seen due to the use of black plastic wrap. The wrap failed in transit.
Gates to provide additional containment on the truck were not used.
The quality of the pallets was poor.
The angle of lashing delivered poor clamping force.
High centre of gravity.
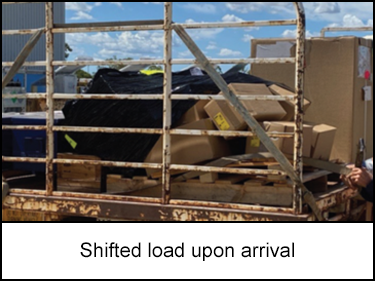
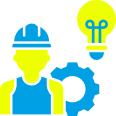
What did they learn?
Ensure that packaging complies with local packaging, handling and movement of materials specifications.
Use clear shrink wrap so that constraints can be seen.
Reduce the height of the load to achieve a lower centre of gravity.
Ensure the load is positioned central to the trailer deck or next to pallets the same height, so that adequate clamping force can be applied with lashings.
Carry out load restraint checks at the point of load.
Consult with all parties involved in the chain of responsibility to ensure that robust means of securing loads are used. Source pallets that are suitable for recirculating through the supply chain.
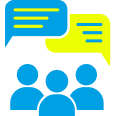
Ask yourself or your crew
Are you involved in securing or transporting loads via road?
Are you aware of local packaging, handling and movement of materials specifications? Do you understand its requirements?
How do you assess the suitability of load restraints?
What is your role in the chain of responsibility?
A truck carrying 470kg (1,036lbs) of cardboard cartons arrived with the load shifted due to failed strapping and plastic wrap. No cartons fell off, but poor pallet quality and lack of containment gates were issues.
Original material courtesy of Safer Together (Australia)
To access the PDF and PowerPoint versions, please visit https://www.safertogether.com.au/resources/sharing-library/driving-loss-of-load-leb-toolbox