-
What happened?
During routine rounds, an operator observed a hydrocarbon leak from the fuel gas system pipeline, downstream from a condensate flash vessel (40 bar).
While investigating the leak, the operator’s personal gas monitor alarmed.
The operator immediately left the area and informed their supervisor.
All work was suspended, and the workforce was mustered in living quarters behind the blast wall until the risk could be further understood.
The leak response protocol (LRP) was applied, and the decision was made to commence a controlled shutdown of the facility.
-
Why did it happen?
By performing routine operator duties diligently, an operator detected a pinhole leak early.
A personal gas monitor was an effective safeguard to alert an operator of a hazard in the work area.
Implementation of the Leak response and loss prevention process provided the Operations team with a risk-based framework to assess and respond to the leak.
Good operational excellence leadership and culture provided the foundation for open engagement to understand potential risk escalation and support an aligned decision to initiate a controlled shutdown.
Stand-up of an installation emergency management team enabled a timely and coordinated response to repairs and communication.
Regular updates were effective in keeping the workforce informed of the facility condition and the safeguards implemented to mitigate escalation.
An established relationship with the safety regulator plus timely and transparent reporting of the event lead to the regulator expressing satisfaction with our response in the media and determining no regulator investigation was necessary.
-
What did they learn?
Consistent application of safeguards:
- LRPs are a common industry safeguard for use within the first minutes after a leak is discovered, to assure leaks are safely responded to and mitigated. They prompt immediate notification and evaluation to decide how the leak should be addressed before approaching.
- Facilities should have LRPs in place and utilised.
Administrative safeguards effectiveness:
- LRPs should be customised to each facility’s risks and needs.
- Frontline workers and contractors should be familiar with and use LRPs. If contractors identify leaks, they should also be familiar with and follow LRPs.
- Recurring training and exercises should be in place to sustain LRP competency.
- Lookbacks should be conducted after LRPs are used, with updates/improvements made based on each incident. Examples include:
- Added safeguards for responding to pyrophoric fire risk
- Added insulation removal requirements
- Added exclusion zone identification
- Updated contact list
- Implementing a LRP database as a system of record
-
Ask yourself or your crew
How do we ensure our leak response protocols are understood and ready to use?
What safeguards do we have in place to detect and respond to leaks early?
How do we tailor our response procedures to the specific risks of our facility?
What training or exercises do we conduct to maintain LRP competency?
Add to homescreen
Content name
Select existing category:
Content name
New collection
Edit collection
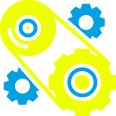
What happened?
During routine rounds, an operator observed a hydrocarbon leak from the fuel gas system pipeline, downstream from a condensate flash vessel (40 bar).
While investigating the leak, the operator’s personal gas monitor alarmed.
The operator immediately left the area and informed their supervisor.
All work was suspended, and the workforce was mustered in living quarters behind the blast wall until the risk could be further understood.
The leak response protocol (LRP) was applied, and the decision was made to commence a controlled shutdown of the facility.
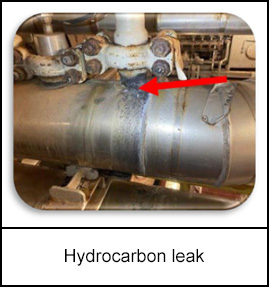
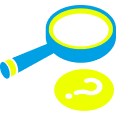
Why did it happen?
By performing routine operator duties diligently, an operator detected a pinhole leak early.
A personal gas monitor was an effective safeguard to alert an operator of a hazard in the work area.
Implementation of the Leak response and loss prevention process provided the Operations team with a risk-based framework to assess and respond to the leak.
Good operational excellence leadership and culture provided the foundation for open engagement to understand potential risk escalation and support an aligned decision to initiate a controlled shutdown.
Stand-up of an installation emergency management team enabled a timely and coordinated response to repairs and communication.
Regular updates were effective in keeping the workforce informed of the facility condition and the safeguards implemented to mitigate escalation.
An established relationship with the safety regulator plus timely and transparent reporting of the event lead to the regulator expressing satisfaction with our response in the media and determining no regulator investigation was necessary.
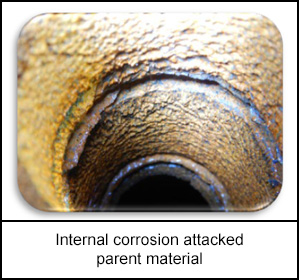
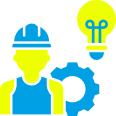
What did they learn?
Consistent application of safeguards:
- LRPs are a common industry safeguard for use within the first minutes after a leak is discovered, to assure leaks are safely responded to and mitigated. They prompt immediate notification and evaluation to decide how the leak should be addressed before approaching.
- Facilities should have LRPs in place and utilised.
Administrative safeguards effectiveness:
- LRPs should be customised to each facility’s risks and needs.
- Frontline workers and contractors should be familiar with and use LRPs. If contractors identify leaks, they should also be familiar with and follow LRPs.
- Recurring training and exercises should be in place to sustain LRP competency.
- Lookbacks should be conducted after LRPs are used, with updates/improvements made based on each incident. Examples include:
- Added safeguards for responding to pyrophoric fire risk
- Added insulation removal requirements
- Added exclusion zone identification
- Updated contact list
- Implementing a LRP database as a system of record
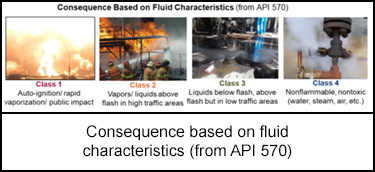
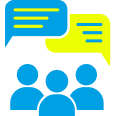
Ask yourself or your crew
How do we ensure our leak response protocols are understood and ready to use?
What safeguards do we have in place to detect and respond to leaks early?
How do we tailor our response procedures to the specific risks of our facility?
What training or exercises do we conduct to maintain LRP competency?
A hydrocarbon leak was detected during routine inspection. The facility was safely shut down using leak response protocols, preventing escalation and harm.