-
What happened?
During an ongoing jacket level survey in an offshore location, a levelling tool encountered a failure. The tool was installed on the top of the jacket pile and connected with grommets and shackles to the jacket legs on both sides.
The pins in the right assembly slipped, causing the grommet, right-side link plate, and lower pin weighing 600 kg (1323 lbs.) to fall into the sea. It landed on the jacket mud mat.
The event led to the area around the levelling tool being restricted, and immediate safety measures were taken to avoid any personnel being in the line of fire during the activity.
-
Why did it happen?
The failure occurred due to the levelling system's design, which did not permit perfect alignment of the link plate with the shackle, resulting in lateral forces.
The engineering design did not account for the possibility of misalignment with the proposed configuration, leading to lateral force on the safety pin.
-
What did they learn?
Review installation procedures: Add a dedicated section to check alignment before commencing the operation. Revise the drawing according to the modified configuration for jacket levelling completion.
Prioritise safety during operations: Consider the line of fire and the positions of personnel throughout the process to ensure safety.
Consider safety pin design: The safety pin design of the levelling tool equipment should account for potential lateral forces. Welding of washers/bolts on the pin should not be considered a possible solution due to the risk of cold cracks.
Consider replacing the link plate and pin with a heavy shackle to rectify inadequate design and ensure safe completion of jacket operations.
Consider using the levelling system with link plates when directly connected to the pad eyes. If not possible, the revised solution with the shackle instead of the link plates should be preferred, as the shackle would have sustained a portion of the horizontal load.
Share lessons learned: Emphasise the importance of sharing lessons with all project and area personnel, particularly regarding system misalignments and the presence of lateral forces.
-
Ask yourself or your crew
How can something like this happen here (e.g. on our site)?
What safety measures (i.e. procedures, controls/barriers) do we have in place to mitigate the risk?
How do we know the risk controls/barriers are working?
What improvements or changes should we make to the procedures, controls/barriers or the way we work?
Add to homescreen
Content name
Select existing category:
Content name
New collection
Edit collection
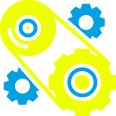
What happened?
During an ongoing jacket level survey in an offshore location, a levelling tool encountered a failure. The tool was installed on the top of the jacket pile and connected with grommets and shackles to the jacket legs on both sides.
The pins in the right assembly slipped, causing the grommet, right-side link plate, and lower pin weighing 600 kg (1323 lbs.) to fall into the sea. It landed on the jacket mud mat.
The event led to the area around the levelling tool being restricted, and immediate safety measures were taken to avoid any personnel being in the line of fire during the activity.
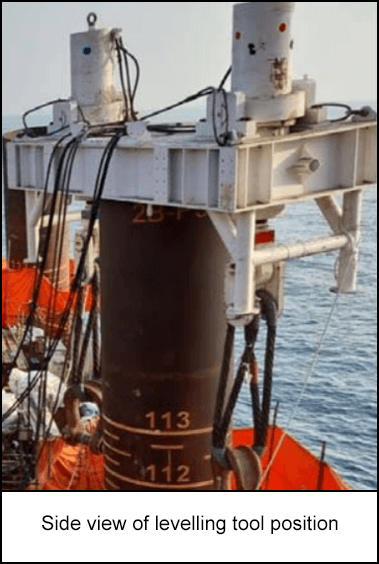
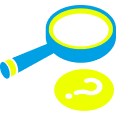
Why did it happen?
The failure occurred due to the levelling system's design, which did not permit perfect alignment of the link plate with the shackle, resulting in lateral forces.
The engineering design did not account for the possibility of misalignment with the proposed configuration, leading to lateral force on the safety pin.
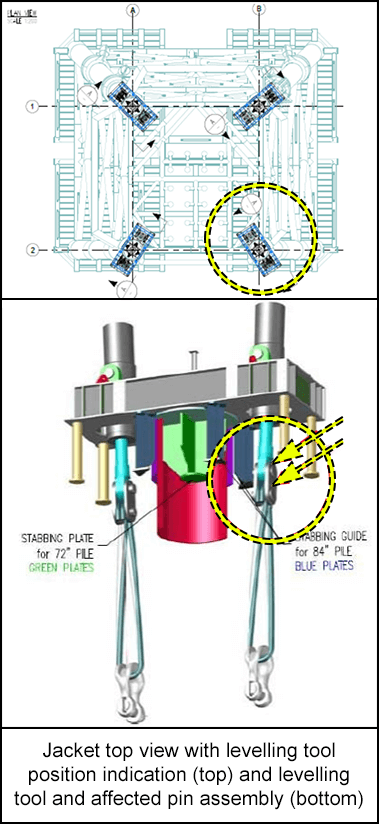
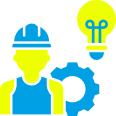
What did they learn?
Review installation procedures: Add a dedicated section to check alignment before commencing the operation. Revise the drawing according to the modified configuration for jacket levelling completion.
Prioritise safety during operations: Consider the line of fire and the positions of personnel throughout the process to ensure safety.
Consider safety pin design: The safety pin design of the levelling tool equipment should account for potential lateral forces. Welding of washers/bolts on the pin should not be considered a possible solution due to the risk of cold cracks.
Consider replacing the link plate and pin with a heavy shackle to rectify inadequate design and ensure safe completion of jacket operations.
Consider using the levelling system with link plates when directly connected to the pad eyes. If not possible, the revised solution with the shackle instead of the link plates should be preferred, as the shackle would have sustained a portion of the horizontal load.
Share lessons learned: Emphasise the importance of sharing lessons with all project and area personnel, particularly regarding system misalignments and the presence of lateral forces.
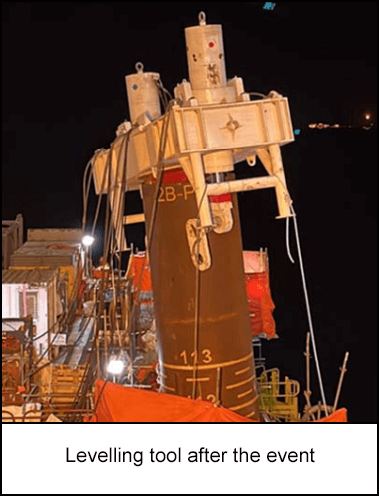
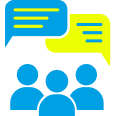
Ask yourself or your crew
How can something like this happen here (e.g. on our site)?
What safety measures (i.e. procedures, controls/barriers) do we have in place to mitigate the risk?
How do we know the risk controls/barriers are working?
What improvements or changes should we make to the procedures, controls/barriers or the way we work?
During an ongoing jacket level survey in an offshore location, a levelling tool encountered a failure. The tool was installed on the top of the jacket pile and connected with grommets and shackles to the jacket legs on both sides. The pins in the right assembly slipped, causing the grommet, right-side link plate, and lower pin weighing 600 kg (1323 lbs.) to fall into the sea and landed on the jacket mud mat.