-
What happened?
While drilling offshore in the 12 ¼” (30.48 cm) hole section at 4,174 metres (2.6 miles) measured depth below rotary table (MDRT) using 1.63 specific gravity (sg) synthetic-based mud (SBM), a sudden 7 barrel (bbl) gain was observed.
Drilling operations were halted, but circulation continued to maintain bottom hole pressure, (BHP) with managed pressure drilling (MPD) in ’flow control’ mode.
Subsequently, the surface back pressure (SBP) increased from 90 to 500 pounds per square inch (psi) (621 to 3,447 kPa), leading to an additional influx.
The total influx volume exceeded the 10 bbl (353 gallons) MPD limit (11 bbl / 389 gallons gain detected). The well was shut-in at the upper annular.
Shut-in casing pressure (SICP) and shut-in drill pipe pressure (SIDP) were recorded at 350 psi (2414 kPa). A well kill was performed using 1.71 sg kill weight mud while maintaining constant BHP via MPD in ’pump at depth’ (P@D) mode.
This incident highlights the importance of accurate pore pressure estimation during well planning and proper MPD mode selection during drilling and kick scenarios.
-
Why did it happen?
The pore pressure exceeded the critical condition prognosis.
The incorrect MPD mode was selected. Instead of using the proper ‘surface pump pressure (SPP) mode’ (which maintains pumping pressure constant), the wrong mode (‘flow control’) was chosen during MPD.
There was confusion in making decisions while handling the influx.
This incident occurred during the rig’s first experience with MPD.
-
What did they learn?
Ensure use of effective pore pressure prediction methods and ensure alignment with actual well conditions.
Ensure hand over between conventional WC and MPD operations.
-
Ask yourself or your crew
How can something like this happen here?
What are we doing / can we do to avoid a similar incident occurring here?
How do/can we ensure proper mode selection during drilling operations?
How can we enhance decision-making processes during influx management? Are there clear guidelines for handling unexpected situations?
How effective are our communication channels during critical moments? Can we streamline communication to prevent confusion?
Add to homescreen
Content name
Select existing category:
Content name
New collection
Edit collection
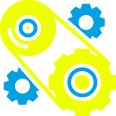
What happened?
While drilling offshore in the 12 ¼” (30.48 cm) hole section at 4,174 metres (2.6 miles) measured depth below rotary table (MDRT) using 1.63 specific gravity (sg) synthetic-based mud (SBM), a sudden 7 barrel (bbl) gain was observed.
Drilling operations were halted, but circulation continued to maintain bottom hole pressure, (BHP) with managed pressure drilling (MPD) in ’flow control’ mode.
Subsequently, the surface back pressure (SBP) increased from 90 to 500 pounds per square inch (psi) (621 to 3,447 kPa), leading to an additional influx.
The total influx volume exceeded the 10 bbl (353 gallons) MPD limit (11 bbl / 389 gallons gain detected). The well was shut-in at the upper annular.
Shut-in casing pressure (SICP) and shut-in drill pipe pressure (SIDP) were recorded at 350 psi (2414 kPa). A well kill was performed using 1.71 sg kill weight mud while maintaining constant BHP via MPD in ’pump at depth’ (P@D) mode.
This incident highlights the importance of accurate pore pressure estimation during well planning and proper MPD mode selection during drilling and kick scenarios.
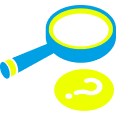
Why did it happen?
The pore pressure exceeded the critical condition prognosis.
The incorrect MPD mode was selected. Instead of using the proper ‘surface pump pressure (SPP) mode’ (which maintains pumping pressure constant), the wrong mode (‘flow control’) was chosen during MPD.
There was confusion in making decisions while handling the influx.
This incident occurred during the rig’s first experience with MPD.
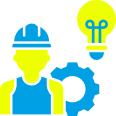
What did they learn?
Ensure use of effective pore pressure prediction methods and ensure alignment with actual well conditions.
Ensure hand over between conventional WC and MPD operations.
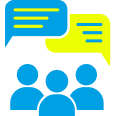
Ask yourself or your crew
How can something like this happen here?
What are we doing / can we do to avoid a similar incident occurring here?
How do/can we ensure proper mode selection during drilling operations?
How can we enhance decision-making processes during influx management? Are there clear guidelines for handling unexpected situations?
How effective are our communication channels during critical moments? Can we streamline communication to prevent confusion?
During offshore drilling in the 12 ¼-inch hole section at 4,174 meters measured depth below rotary table (MDRT) using 1.63 specific gravity synthetic-based mud (SBM), a sudden 7-barrel influx occurred. The surface back pressure (SBP) increased from 90 to 500 psi (621 to 3,447 kPa), exceeding the 10-barrel MPD limit (11-barrel gain detected). Shut-in casing pressure (SICP) and shut-in drill pipe pressure (SIDP) were recorded at 350 psi (2,414 kPa). Accurate pore pressure estimation and proper MPD mode selection are crucial for safe operations.