-
What happened?
During routine operation on a floating production storage and offtake (FPSO) facility, a technician heard an unusual noise from the compressor module.
Control room operators identified a single gas detector with inconsistent readings.
Site investigation found hydrocarbon gas leaking from a valve on the seal gas filter of the online compressor.
Three bolts on the double block and bleed valve, attached to the seal gas filter had failed.
-
Why did it happen?
The seal gas system was routinely operating at a temperature above 80°C (176°F).
The bolts on the double block and bleed valve were made of SS316 grade stainless steel.
SS316 is susceptible to chloride external stress corrosion cracking at temperatures above 50-60°C (122-140°F) in marine environments / chlorides present.
SS316 is not the correct material for this service.
This had not been identified during design or subsequent operation.
-
What did they learn?
Ensure engineering design does not specify SS316 in conditions that are vulnerable to chloride external stress corrosion cracking (i.e. operating temperatures above 50-60°C (122-140°F) in marine environments / chlorides present).
Check that pressure-containing equipment in conditions that are vulnerable to chloride external stress corrosion cracking does not contain SS316.
Establish assurance processes to ensure that materials supplied on vendor packages during projects do not contain SS316 for equipment in services that are vulnerable to chloride external stress corrosion cracking.
-
Ask yourself or your crew
Do you have pressure containing equipment operating in conditions vulnerable to chloride external stress corrosion cracking (i.e. operating temperatures above 50-60°C (122-140°F) in marine environments / chlorides present)? Is any of this equipment made from SS316? How would you know? What would you do if you identified equipment made from SS316 operating in these conditions?
Do your inspection processes check for the presence of SS316 in equipment operating in conditions vulnerable to chloride external stress corrosion cracking? Are competent personnel reviewing and inspecting this type of equipment?
Do your engineering designs ensure that SS316 is not specified in conditions that are vulnerable to chloride external stress corrosion cracking? Are adequate quality systems in place to ensure the correct materials are delivered and installed on your facility?
Add to homescreen
Content name
Select existing category:
Content name
New collection
Edit collection
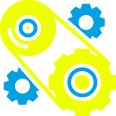
What happened?
During routine operation on a floating production storage and offtake (FPSO) facility, a technician heard an unusual noise from the compressor module.
Control room operators identified a single gas detector with inconsistent readings.
Site investigation found hydrocarbon gas leaking from a valve on the seal gas filter of the online compressor.
Three bolts on the double block and bleed valve, attached to the seal gas filter had failed.
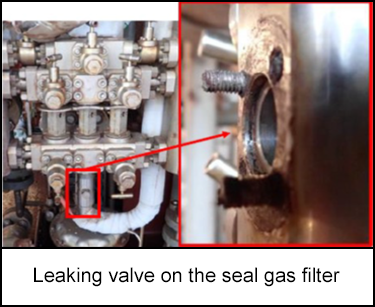
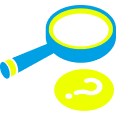
Why did it happen?
The seal gas system was routinely operating at a temperature above 80°C (176°F).
The bolts on the double block and bleed valve were made of SS316 grade stainless steel.
SS316 is susceptible to chloride external stress corrosion cracking at temperatures above 50-60°C (122-140°F) in marine environments / chlorides present.
SS316 is not the correct material for this service.
This had not been identified during design or subsequent operation.
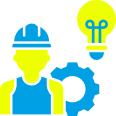
What did they learn?
Ensure engineering design does not specify SS316 in conditions that are vulnerable to chloride external stress corrosion cracking (i.e. operating temperatures above 50-60°C (122-140°F) in marine environments / chlorides present).
Check that pressure-containing equipment in conditions that are vulnerable to chloride external stress corrosion cracking does not contain SS316.
Establish assurance processes to ensure that materials supplied on vendor packages during projects do not contain SS316 for equipment in services that are vulnerable to chloride external stress corrosion cracking.
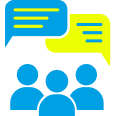
Ask yourself or your crew
Do you have pressure containing equipment operating in conditions vulnerable to chloride external stress corrosion cracking (i.e. operating temperatures above 50-60°C (122-140°F) in marine environments / chlorides present)? Is any of this equipment made from SS316? How would you know? What would you do if you identified equipment made from SS316 operating in these conditions?
Do your inspection processes check for the presence of SS316 in equipment operating in conditions vulnerable to chloride external stress corrosion cracking? Are competent personnel reviewing and inspecting this type of equipment?
Do your engineering designs ensure that SS316 is not specified in conditions that are vulnerable to chloride external stress corrosion cracking? Are adequate quality systems in place to ensure the correct materials are delivered and installed on your facility?
During routine operations on a floating production storage and offtake (FPSO) facility, a technician detected an unusual noise from the compressor module. Subsequent investigation revealed a hydrocarbon gas leak from a valve on the seal gas filter, caused by the failure of three bolts on the double block and bleed valve.
Original material courtesy of Safer Together (Australia)
To access the PDF and PowerPoint versions, please visit https://www.safertogether.com.au/resources/sharing-library/operating-process-equipment-loss-of-containment-aug-2024