-
What happened?
A contract projects team was preparing to tie a gas lift injection line from the gas lift regulator skid to a new remote triple pad, when a welder performed a hot cut into a pressurised, un-isolated line, causing an ignited gas release at the work site.
The flames were quickly extinguished, and the line was isolated.
Fortunately, there were no injuries. There was a substantial potential for a more severe incident if an upstream compressor had been operational.
-
Why did it happen?
Tie in points for the 2 foot gas lift line were not provided as part of the initial design (unlike the oil line tie in design), requiring hot work to connect to energised process equipment.
There was poor isolation management. Deficiencies included:
- a poor isolation scheme development and selection of long-term isolations;
- no independent isolation scheme approval or verification;
- inadequate verification of isolations on site prior to starting work, and
- lockout/tagout (LOTO) training and competency gaps.
Work planning and scheduling practices resulted in limited time and resources for isolation planning and simultaneous operations (SIMOPS) management with operations and other stakeholders.
It is essential to proactively monitor and remain sensitive to ‘how work gets done’, and routinely assess the effectiveness of critical controls, which may degrade over time and as a result of efficiency initiatives.
-
What did they learn?
Make tie-in arrangements for new wells into existing facilities inherently safer.
Improve procedures, technical documentation, and governance for brownfield isolation management.
Define isolation roles and responsibilities between ops and projects (SIMOPS, hand-over, communications).
Enhance lockout/tagout (LOTO) training and competency for key roles with isolation responsibilities.
Strengthen project planning and execution processes and define interfaces with operations.
-
Ask yourself or your crew
How can something similar happen on our site?
How do you currently verify and ensure proper isolation before starting work on process equipment, and do you believe there are any gaps or challenges in this process?
What are some common challenges you face in managing simultaneous operations (SIMOPS) and coordinating work with other stakeholders? Are there any specific instances where this has been difficult?
In your day-to-day work, what critical controls do you rely on to ensure safety, and how do you monitor and assess the effectiveness of these controls over time?
What improvements or changes should we make to the procedures, controls/barriers or the way we work?
Add to homescreen
Content name
Select existing category:
Content name
New collection
Edit collection
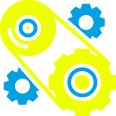
What happened?
A contract projects team was preparing to tie a gas lift injection line from the gas lift regulator skid to a new remote triple pad, when a welder performed a hot cut into a pressurised, un-isolated line, causing an ignited gas release at the work site.
The flames were quickly extinguished, and the line was isolated.
Fortunately, there were no injuries. There was a substantial potential for a more severe incident if an upstream compressor had been operational.
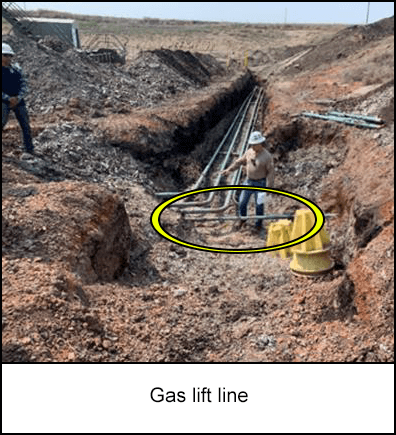
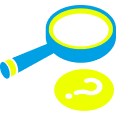
Why did it happen?
Tie in points for the 2 foot gas lift line were not provided as part of the initial design (unlike the oil line tie in design), requiring hot work to connect to energised process equipment.
There was poor isolation management. Deficiencies included:
- a poor isolation scheme development and selection of long-term isolations;
- no independent isolation scheme approval or verification;
- inadequate verification of isolations on site prior to starting work, and
- lockout/tagout (LOTO) training and competency gaps.
Work planning and scheduling practices resulted in limited time and resources for isolation planning and simultaneous operations (SIMOPS) management with operations and other stakeholders.
It is essential to proactively monitor and remain sensitive to ‘how work gets done’, and routinely assess the effectiveness of critical controls, which may degrade over time and as a result of efficiency initiatives.
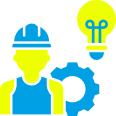
What did they learn?
Make tie-in arrangements for new wells into existing facilities inherently safer.
Improve procedures, technical documentation, and governance for brownfield isolation management.
Define isolation roles and responsibilities between ops and projects (SIMOPS, hand-over, communications).
Enhance lockout/tagout (LOTO) training and competency for key roles with isolation responsibilities.
Strengthen project planning and execution processes and define interfaces with operations.
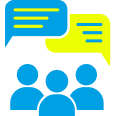
Ask yourself or your crew
How can something similar happen on our site?
How do you currently verify and ensure proper isolation before starting work on process equipment, and do you believe there are any gaps or challenges in this process?
What are some common challenges you face in managing simultaneous operations (SIMOPS) and coordinating work with other stakeholders? Are there any specific instances where this has been difficult?
In your day-to-day work, what critical controls do you rely on to ensure safety, and how do you monitor and assess the effectiveness of these controls over time?
What improvements or changes should we make to the procedures, controls/barriers or the way we work?
A contract projects team was preparing to tie a gas lift injection line from the gas lift regulator skid to a new remote triple pad, when a welder performed a hot cut into a pressurised, un-isolated line, causing an ignited gas release at the work site.