-
What happened?
A team of technicians were in the process of replacing the main bearing following the prescribed method statement. After successfully rebuilding the main bearing, they were preparing to install the hub.
During the preparation to lift the hub into position from the jack-up deck, an authorized technician (AT) inside the nacelle noticed that the low-speed locking pin was engaged. The AT advised that the locking pin needed to be disengaged before proceeding with the hub installation.
While removing the low-speed locking pin, the plate on the left-hand side slipped from its position, causing an impact on the nacelle floor. As a result, the floor gave way, and the 300kg plate fell a considerable distance of 80 metres (262 feet) to the seafloor bed.
Initial observations revealed that the four M12 bolts securing the plate were sheared. The other two plates on the main bearing remained unaffected and in place.
Following the incident, the area was secured, and all team members left the nacelle safely, returning to the barge.
-
Why did it happen?
The low-speed locking pin was engaged, contrary to the standard practice where it should not be engaged.
There was no written instruction or procedure specifying the check of the low-speed locking pin's engagement status, which is the root cause of the issue.
Technicians activated the hydraulics without noticing that the low-speed locking pin was engaged.
The method statement did not include a safety-critical check regarding the status of the locking pins before engaging the hydraulics, which is an essential step.
The procedure for checking if the low-speed locking pin was disengaged was not covered, pointing to an incorrect procedure and another root cause.
A technician removed the engaged low-speed locking pin, addressing the immediate cause of the accident.
The method statement lacked coverage for situations where the locking pin is engaged, which is another root cause.
The quality check process for received and shipped goods did not include a procedure or detailed process to identify safety-critical checks that should be verified at key stages.
-
What did they learn?
Incorporate in the method statement and risk assessment:
- Check that bolts are installed before main bearing removal.
- Conduct a visual inspection to ensure low-speed locks are removed.
Update the company's lift plan to include additional steps to ensure low-speed locks are disengaged during lifting operations.
Establish a robust activity management plan that includes:
- proactive monitoring of work activities;
- regular auditing to ensure strict adherence to safety procedures.
-
Ask yourself or your crew
What safety-critical checks should be included in your work activities to prevent similar accidents from happening on our site?
How do you typically check the low-speed locking pin's engagement status before proceeding with a hub installation? Are there any challenges or limitations in performing this check?
What changes or improvements could be made to the existing lift plan to ensure the disengagement of low-speed locks during lifting operations?
What improvements or changes should we make to the procedures, controls/barriers or the way we work?
Add to homescreen
Content name
Select existing category:
Content name
New collection
Edit collection
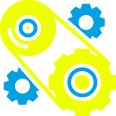
What happened?
A team of technicians were in the process of replacing the main bearing following the prescribed method statement. After successfully rebuilding the main bearing, they were preparing to install the hub.
During the preparation to lift the hub into position from the jack-up deck, an authorized technician (AT) inside the nacelle noticed that the low-speed locking pin was engaged. The AT advised that the locking pin needed to be disengaged before proceeding with the hub installation.
While removing the low-speed locking pin, the plate on the left-hand side slipped from its position, causing an impact on the nacelle floor. As a result, the floor gave way, and the 300kg plate fell a considerable distance of 80 metres (262 feet) to the seafloor bed.
Initial observations revealed that the four M12 bolts securing the plate were sheared. The other two plates on the main bearing remained unaffected and in place.
Following the incident, the area was secured, and all team members left the nacelle safely, returning to the barge.
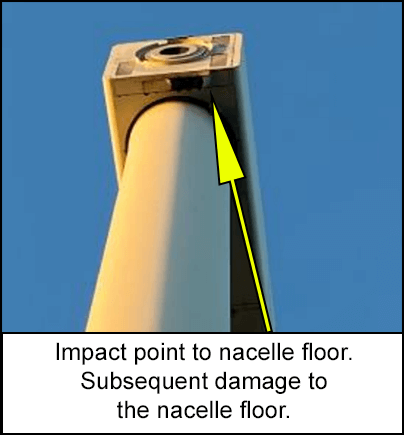
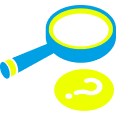
Why did it happen?
The low-speed locking pin was engaged, contrary to the standard practice where it should not be engaged.
There was no written instruction or procedure specifying the check of the low-speed locking pin's engagement status, which is the root cause of the issue.
Technicians activated the hydraulics without noticing that the low-speed locking pin was engaged.
The method statement did not include a safety-critical check regarding the status of the locking pins before engaging the hydraulics, which is an essential step.
The procedure for checking if the low-speed locking pin was disengaged was not covered, pointing to an incorrect procedure and another root cause.
A technician removed the engaged low-speed locking pin, addressing the immediate cause of the accident.
The method statement lacked coverage for situations where the locking pin is engaged, which is another root cause.
The quality check process for received and shipped goods did not include a procedure or detailed process to identify safety-critical checks that should be verified at key stages.
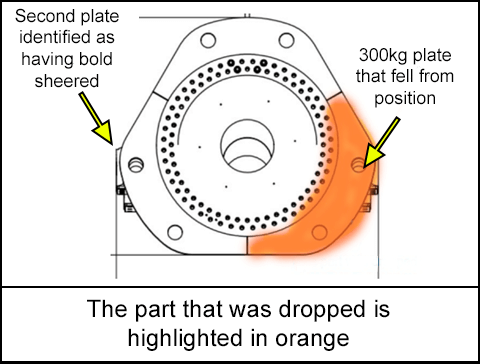
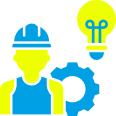
What did they learn?
Incorporate in the method statement and risk assessment:
- Check that bolts are installed before main bearing removal.
- Conduct a visual inspection to ensure low-speed locks are removed.
Update the company's lift plan to include additional steps to ensure low-speed locks are disengaged during lifting operations.
Establish a robust activity management plan that includes:
- proactive monitoring of work activities;
- regular auditing to ensure strict adherence to safety procedures.
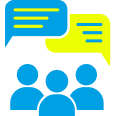
Ask yourself or your crew
What safety-critical checks should be included in your work activities to prevent similar accidents from happening on our site?
How do you typically check the low-speed locking pin's engagement status before proceeding with a hub installation? Are there any challenges or limitations in performing this check?
What changes or improvements could be made to the existing lift plan to ensure the disengagement of low-speed locks during lifting operations?
What improvements or changes should we make to the procedures, controls/barriers or the way we work?
During a routine bearing replacement, an incident occurred when a 300 kg (621 lbs) plate fell 80 metres (262 feet) due to an engaged low-speed locking pin. Uncover the root causes and key safety lessons for enhanced maintenance procedures.