-
What happened?
On a wind turbine generator (WTG), a technician fell from the ladder between the nacelle and the yaw platform.
While descending, the technician missed a step that was removed for a cable pulling operation and fell to the side while holding the nacelle floor.
The nacelle hatch closed, and his right hand got trapped, causing injury to his upper hand.
The technician was always conscious and was able to leave the WTG by himself.
First aid was administered whilst waiting on evacuation of the technician by ambulance, to the closest hand clinic.
-
Why did it happen?
Step ladder design:
- The hazard of removing and reinserting steps was not properly evaluated at the design phase and was missing from procedural steps.
Communications/hand over process:
- There was no post-job review. The hazard of removing the step has become a familiar and accepted condition onsite without control measures. The workforce was only relying on the awareness of the missing step when coming down the ladder.
Pre-job briefing and last-minute risk assessment:
- Pre-job brief is not detailed enough to outlined hazards coming from previous operations and not all personnel on the team take part in it.
- Last minute risk assessments are not properly carried out.
Hatch design:
- The hatch is not fitted with damper (soft closing mechanism).
- The closure of the hatch does not protect from sharp edges.
-
What did they learn?
Hatch design must be thoroughly assessed at an early stage of the project, while taking into consideration:
- access/egress, falling/tripping and sharp edges hazards;
- a suitable soft-closing mechanism, and
- protection of sharp edges.
Permanent and temporary access means must always be maintained safely. When this cannot be achieved, access must be barriered off to prevent unsafe access.
Perform trial test / fit of installation methodology prior to validation of the method statement.
Ensure pre-job briefing, last minute risk assessment and hand-over processes are implemented and documented with attendance of the entire work team.
Promote reporting of unsafe situations and conditions.
-
Ask yourself or your crew
How do we ensure that temporary changes to access routes are clearly communicated and controlled?
What steps can we take to improve our pre-job briefings and ensure full team participation?
How do we verify that design changes or temporary modifications are safe before use?
What mechanisms do we have in place to identify and report unsafe conditions?
How can we improve the way we manage hand-over between teams or shifts?
Add to homescreen
Content name
Select existing category:
Content name
New collection
Edit collection
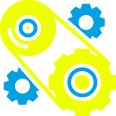
What happened?
On a wind turbine generator (WTG), a technician fell from the ladder between the nacelle and the yaw platform.
While descending, the technician missed a step that was removed for a cable pulling operation and fell to the side while holding the nacelle floor.
The nacelle hatch closed, and his right hand got trapped, causing injury to his upper hand.
The technician was always conscious and was able to leave the WTG by himself.
First aid was administered whilst waiting on evacuation of the technician by ambulance, to the closest hand clinic.
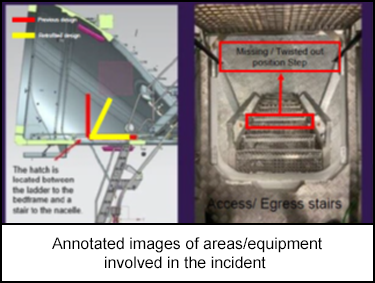
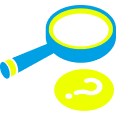
Why did it happen?
Step ladder design:
- The hazard of removing and reinserting steps was not properly evaluated at the design phase and was missing from procedural steps.
Communications/hand over process:
- There was no post-job review. The hazard of removing the step has become a familiar and accepted condition onsite without control measures. The workforce was only relying on the awareness of the missing step when coming down the ladder.
Pre-job briefing and last-minute risk assessment:
- Pre-job brief is not detailed enough to outlined hazards coming from previous operations and not all personnel on the team take part in it.
- Last minute risk assessments are not properly carried out.
Hatch design:
- The hatch is not fitted with damper (soft closing mechanism).
- The closure of the hatch does not protect from sharp edges.
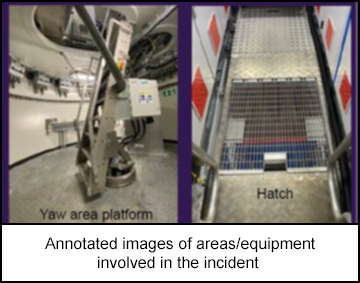
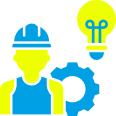
What did they learn?
Hatch design must be thoroughly assessed at an early stage of the project, while taking into consideration:
- access/egress, falling/tripping and sharp edges hazards;
- a suitable soft-closing mechanism, and
- protection of sharp edges.
Permanent and temporary access means must always be maintained safely. When this cannot be achieved, access must be barriered off to prevent unsafe access.
Perform trial test / fit of installation methodology prior to validation of the method statement.
Ensure pre-job briefing, last minute risk assessment and hand-over processes are implemented and documented with attendance of the entire work team.
Promote reporting of unsafe situations and conditions.
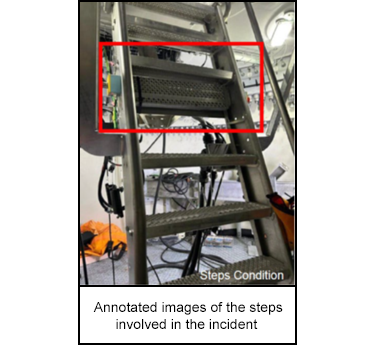
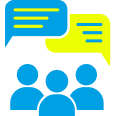
Ask yourself or your crew
How do we ensure that temporary changes to access routes are clearly communicated and controlled?
What steps can we take to improve our pre-job briefings and ensure full team participation?
How do we verify that design changes or temporary modifications are safe before use?
What mechanisms do we have in place to identify and report unsafe conditions?
How can we improve the way we manage hand-over between teams or shifts?
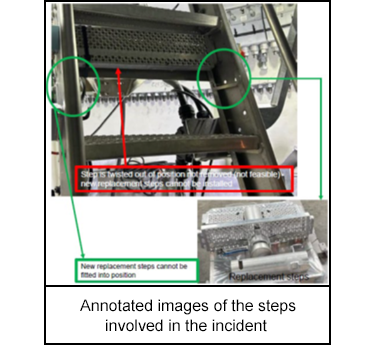
A technician suffered a hand injury after falling during ladder descent in a wind turbine. A missing step and hatch design contributed to the incident.