-
What happened?
After completing an 8,000-hour service, the start sequence on a gas turbine was initiated.
During the purge cycle of the start sequence, while the turbine was being brought up to speed by the electric start motor and just prior to the fuel ignition sequence, the area operator opened the enclosure door of the turbine to conduct visual leak checks.
Upon opening the enclosure door, the area operator could hear the release of positive air pressure from combustion chamber #5 as the fuel injector was missing.
The enclosure door was promptly closed, and the local emergency stop button was activated.
-
Why did it happen?
The handover process was conducted in person, but the detail was not accurately handed over/understood by the oncoming Technician.
Not all steps in the service maintenance procedure had been signed off.
Isolations were removed and a major equipment return to service check sheet was completed without site confirmation. The missing fuel injector was not noticed.
It was assumed that the work had been completed as had been handed over the previous three-night shifts for other gas turbines, leading to oversights.
There was inconsistency in how service maintenance procedure steps were signed off.
-
What did they learn?
Update maintenance procedures and permit requirements to include verification of completed and signed.
Conduct training on service maintenance procedure usage, format, and usability for major equipment service.
Revise turbine enclosure entry operating documents to prohibit personnel access during start-up.
-
Ask yourself or your crew
Do we understand how work is really being done in the field versus how we think it gets done, including work by specialist contractors?
How can we ensure the barriers we take credit for every day are implemented and effective?
Do we identify critical controls in a task (what we can’t get wrong) to prevent life altering and/or environmental harm events we can’t recover from?
Add to homescreen
Content name
Select existing category:
Content name
New collection
Edit collection
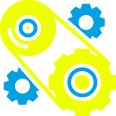
What happened?
After completing an 8,000-hour service, the start sequence on a gas turbine was initiated.
During the purge cycle of the start sequence, while the turbine was being brought up to speed by the electric start motor and just prior to the fuel ignition sequence, the area operator opened the enclosure door of the turbine to conduct visual leak checks.
Upon opening the enclosure door, the area operator could hear the release of positive air pressure from combustion chamber #5 as the fuel injector was missing.
The enclosure door was promptly closed, and the local emergency stop button was activated.
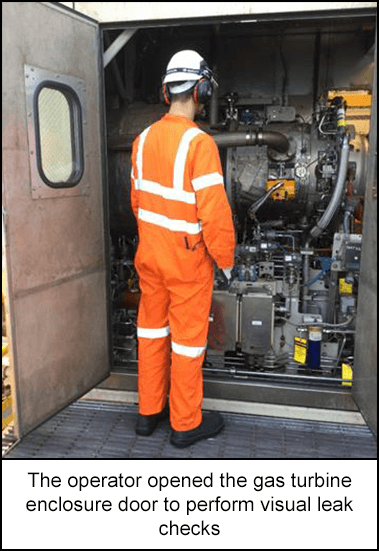
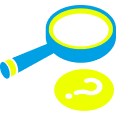
Why did it happen?
The handover process was conducted in person, but the detail was not accurately handed over/understood by the oncoming Technician.
Not all steps in the service maintenance procedure had been signed off.
Isolations were removed and a major equipment return to service check sheet was completed without site confirmation. The missing fuel injector was not noticed.
It was assumed that the work had been completed as had been handed over the previous three-night shifts for other gas turbines, leading to oversights.
There was inconsistency in how service maintenance procedure steps were signed off.
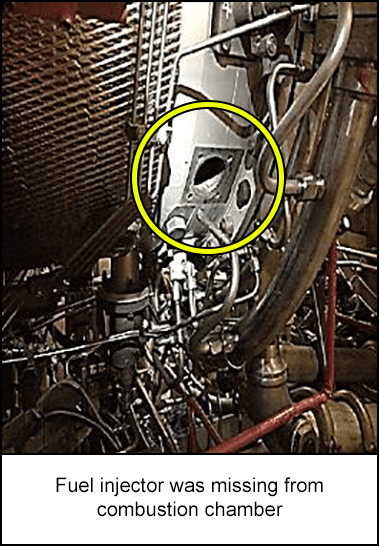
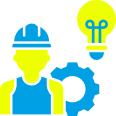
What did they learn?
Update maintenance procedures and permit requirements to include verification of completed and signed.
Conduct training on service maintenance procedure usage, format, and usability for major equipment service.
Revise turbine enclosure entry operating documents to prohibit personnel access during start-up.
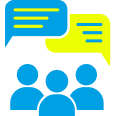
Ask yourself or your crew
Do we understand how work is really being done in the field versus how we think it gets done, including work by specialist contractors?
How can we ensure the barriers we take credit for every day are implemented and effective?
Do we identify critical controls in a task (what we can’t get wrong) to prevent life altering and/or environmental harm events we can’t recover from?
After completing an 8,000-hour service, the start sequence on a gas turbine was initiated. During the purge cycle of the start sequence, while the turbine was being brought up to speed and just prior to the fuel ignition sequence, the area operator opened the enclosure door of the turbine to conduct visual leak checks. The operator could hear the release of positive air pressure from the combustion chamber as the fuel injector was missing. The enclosure door was promptly closed, and the local emergency stop button was activated.