-
What happened?
Production personnel were depressurising the main tubing of a water injection well prior to a rig move.
The well had been shut-in for several years due to connection with a production well in the reservoir. The well was depressurised from an initial shut-in pressure of 151 barg through a hard piped drain line to a seawater dump caisson.
Unknown to the personnel performing the activity, a gas cap had formed in the water injection well, and when the well was depressurised into the seawater dump caisson, a substantial quantity of hydrocarbon gas was released in at least 3 locations of the platform.
Gas detectors at various locations detected the release, leading to closing of the dampers, activation of the emergency shutdown and blowdown system, and a general platform alarm.
The released gas did not find an ignition source, partly due to the event occurring during the night shift and partly due to the equipment in the utility area being Ex rated.
-
Why did it happen?
Immediate causes:
- Gas in the well was depressurised to the sea water dump caisson.
- Sea water dump caisson was not designed for hydrocarbon service.
- 2 inch (5 cm) line at the inlet to the seawater dump caisson had cracks.
- Transient pressure in the 2 inch (5 cm) line.
- Previously applied temporary ‘repair’ did not contain pressure.
Root causes:
Hazards associated with the “routine” operation were not fully identified or assessed. The term ‘Routine’ confused with ‘low risk’.
- Relevant expertise not utilised in job preparation.
- Focus on methods of execution, over controlling associated hazards.
- Permit review & assurance process failed to identify weaknesses in the permit.
- Variances in application of Control of Work process.
- Critical activities not subject to written procedures.
Relevant expertise was not utilised in job preparation:
- Well Services expertise and information not utilised in task planning.
- Well Services Supervisor role not integrated into offshore leadership team.
Focus on methods of execution, over controlling associated hazards:
- Well Supervisor and Production Supervisor did not discuss well during rig move preparation.
Permit review & assurance process failed to identify weaknesses in the permit.
Variances in application of control of work process.
Critical activities not subject to written procedures:
- Approved depressurisation checklists did not exist.
Design issues:
- Original basis of design did not consider water injection well or water injection system as a hydrocarbon source.
- Hydrocarbon and utility system interface is inherent with the water injection drain design, yet there is no designated control mechanism such as ‘Locked Closed’ valve designation.
-
What did they learn?
Identify, assess and approve all unauthorised temporary repairs.
Perform job risk assessments for all activities.
Offshore installation managers (OIMs) need to approve all permits.
-
Ask yourself or your crew
How could something like this happen here?
What does ‘routine’ mean to us? How is this different to ‘low risk’?
How do we know we have the right expertise involved in this job?
What do you think we can learn from this incident?
Add to homescreen
Content name
Select existing category:
Content name
New collection
Edit collection
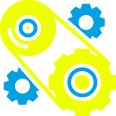
What happened?
Production personnel were depressurising the main tubing of a water injection well prior to a rig move.
The well had been shut-in for several years due to connection with a production well in the reservoir. The well was depressurised from an initial shut-in pressure of 151 barg through a hard piped drain line to a seawater dump caisson.
Unknown to the personnel performing the activity, a gas cap had formed in the water injection well, and when the well was depressurised into the seawater dump caisson, a substantial quantity of hydrocarbon gas was released in at least 3 locations of the platform.
Gas detectors at various locations detected the release, leading to closing of the dampers, activation of the emergency shutdown and blowdown system, and a general platform alarm.
The released gas did not find an ignition source, partly due to the event occurring during the night shift and partly due to the equipment in the utility area being Ex rated.
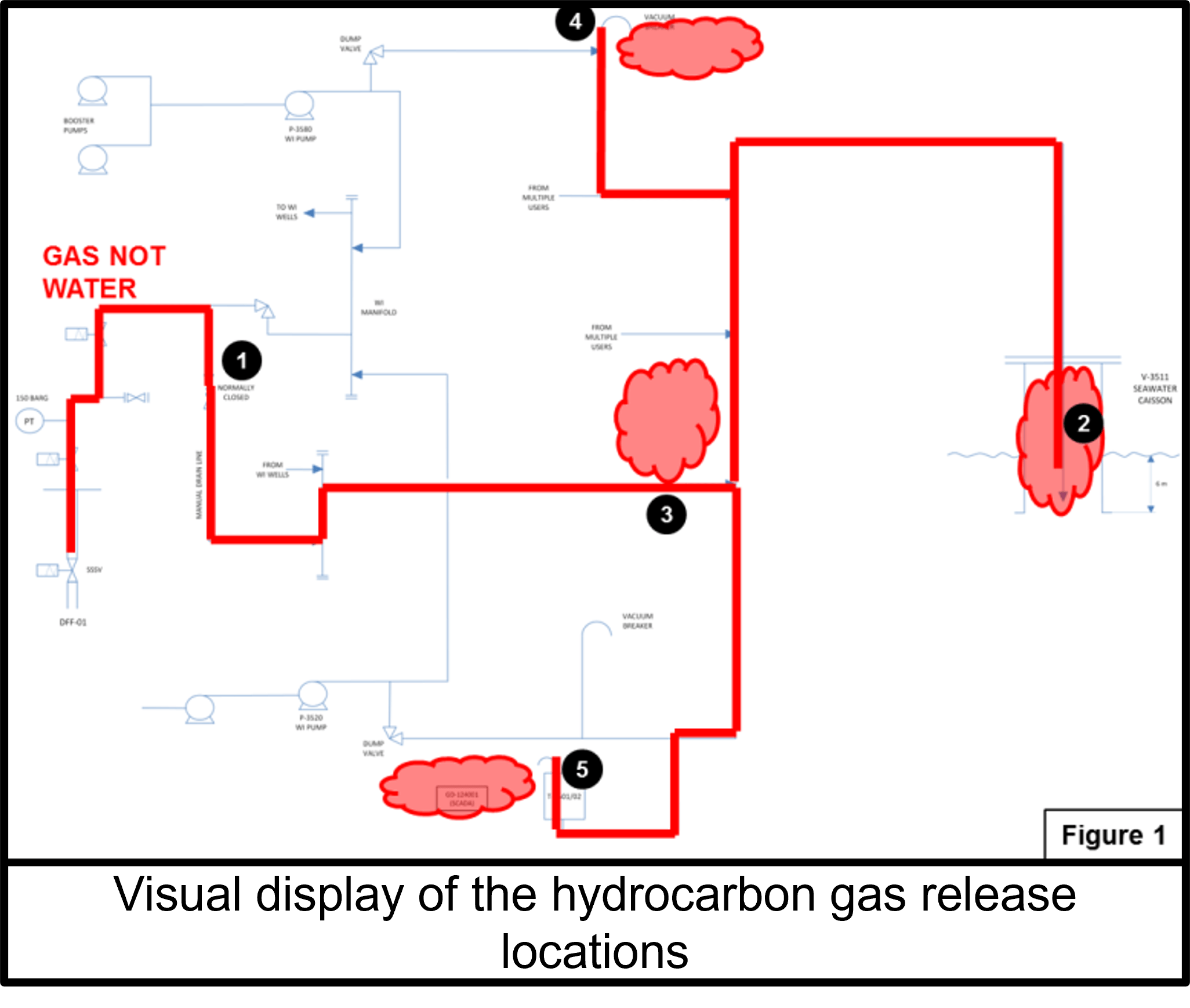
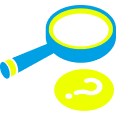
Why did it happen?
Immediate causes:
- Gas in the well was depressurised to the sea water dump caisson.
- Sea water dump caisson was not designed for hydrocarbon service.
- 2 inch (5 cm) line at the inlet to the seawater dump caisson had cracks.
- Transient pressure in the 2 inch (5 cm) line.
- Previously applied temporary ‘repair’ did not contain pressure.
Root causes:
Hazards associated with the “routine” operation were not fully identified or assessed. The term ‘Routine’ confused with ‘low risk’.
- Relevant expertise not utilised in job preparation.
- Focus on methods of execution, over controlling associated hazards.
- Permit review & assurance process failed to identify weaknesses in the permit.
- Variances in application of Control of Work process.
- Critical activities not subject to written procedures.
Relevant expertise was not utilised in job preparation:
- Well Services expertise and information not utilised in task planning.
- Well Services Supervisor role not integrated into offshore leadership team.
Focus on methods of execution, over controlling associated hazards:
- Well Supervisor and Production Supervisor did not discuss well during rig move preparation.
Permit review & assurance process failed to identify weaknesses in the permit.
Variances in application of control of work process.
Critical activities not subject to written procedures:
- Approved depressurisation checklists did not exist.
Design issues:
- Original basis of design did not consider water injection well or water injection system as a hydrocarbon source.
- Hydrocarbon and utility system interface is inherent with the water injection drain design, yet there is no designated control mechanism such as ‘Locked Closed’ valve designation.
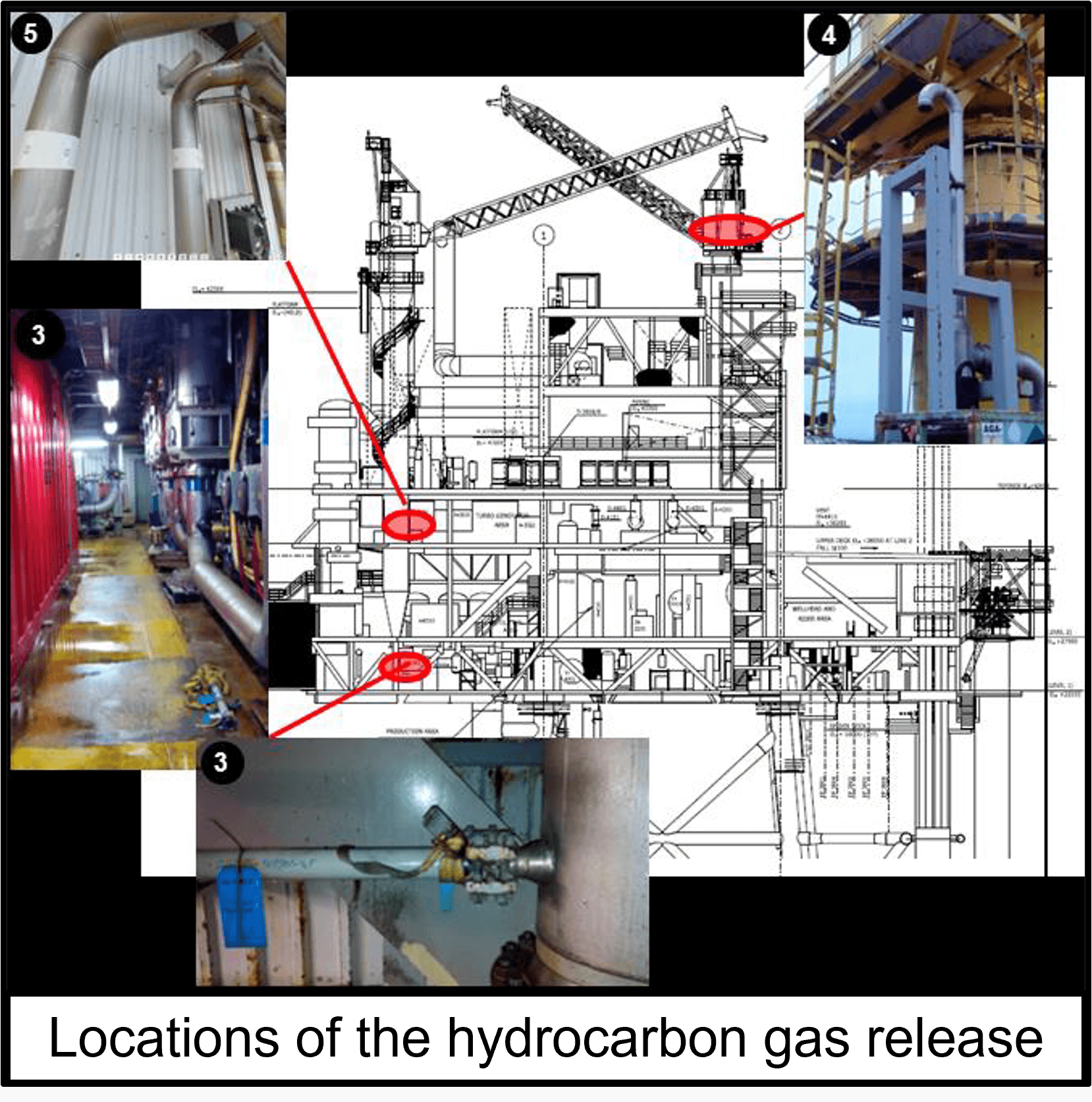
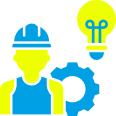
What did they learn?
Identify, assess and approve all unauthorised temporary repairs.
Perform job risk assessments for all activities.
Offshore installation managers (OIMs) need to approve all permits.
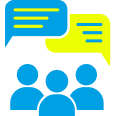
Ask yourself or your crew
How could something like this happen here?
What does ‘routine’ mean to us? How is this different to ‘low risk’?
How do we know we have the right expertise involved in this job?
What do you think we can learn from this incident?
Production personnel were depressurising the main tubing of a water injection well prior to a rig more. An undetected gas cap had formed in the well and when it was depressurised, a significant quantity of flammable hydrocarbon gas was released in at least three locations of the platform.