-
What happened?
A gas leak was identified from the bottom of the outlet flange on a valve in a gas regulator train.
Two days earlier the gas yard had been pressure tested and returned to service.
The leak was isolated within 30 minutes of being detected.
-
Why did it happen?
Compression damage to the gasket occurred during the equipment inspection process when ‘A’ spool in the regulator train was lifted and impacted ‘B’ spool’, resulting in movement to both the temporary support and the ‘B’ spool.
The changing process conditions of this equipment is suspected to have contributed to the flange face opening at the gasket sealing face.
-
What did they learn?
Ensure personnel are trained/competent and understand the “Stop and Re-Assess” step.
Ensure that disassembly risks to adjoining infrastructure are managed throughout the task.
Ensure that flange re-facing equipment and operators are onsite during intrusive flange opening works.
-
Ask yourself or your crew
Do you do intrusive flange opening works at your site? What controls do you have in place to identify hazards and manage the risks associated with this activity?
Do you stop and alert your supervisor if the job you are doing does not proceed as you had planned?
Do you check for leaks before, during, and after you reinstate equipment?
Add to homescreen
Content name
Select existing category:
Content name
New collection
Edit collection
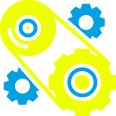
What happened?
A gas leak was identified from the bottom of the outlet flange on a valve in a gas regulator train.
Two days earlier the gas yard had been pressure tested and returned to service.
The leak was isolated within 30 minutes of being detected.
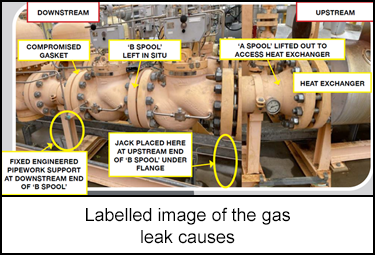
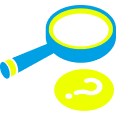
Why did it happen?
Compression damage to the gasket occurred during the equipment inspection process when ‘A’ spool in the regulator train was lifted and impacted ‘B’ spool’, resulting in movement to both the temporary support and the ‘B’ spool.
The changing process conditions of this equipment is suspected to have contributed to the flange face opening at the gasket sealing face.
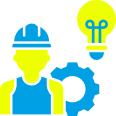
What did they learn?
Ensure personnel are trained/competent and understand the “Stop and Re-Assess” step.
Ensure that disassembly risks to adjoining infrastructure are managed throughout the task.
Ensure that flange re-facing equipment and operators are onsite during intrusive flange opening works.
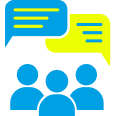
Ask yourself or your crew
Do you do intrusive flange opening works at your site? What controls do you have in place to identify hazards and manage the risks associated with this activity?
Do you stop and alert your supervisor if the job you are doing does not proceed as you had planned?
Do you check for leaks before, during, and after you reinstate equipment?
A gas leak was detected at the outlet flange of a valve in a gas regulator train, just two days after a pressure test. The leak was isolated within 30 minutes of detection.
Original material courtesy of Safer Together (Australia)
To access the PDF and PowerPoint versions, please visit https://www.safertogether.com.au/resources/sharing-library/operating-process-equipment-loss-of-containment-nov-2022