-
What happened?
When operators entered the pipeline delivery station to a liquefied natural gas (LNG) plant for training and familiarisation, they could hear a gas leak.
They found a braided flexible hose was leaking on a sample line tubing to sampling probe on the metering skid.
The leak was visible with a gas cloud extending about 2m3 (71 cubic feet) from the sample line tubing.
The leak rate was estimated to be 60kg/hr (132lbs/hr). The total volume of the leak is unknown.
Operators notified the control room and leadership team. The area was isolated immediately and vented to zero making the work area safe.
-
Why did it happen?
The retractable probe design required use of flexible hoses in high pressure service.
Material used for retractable probe flexible hose (304 stainless steel) was susceptible to chloride pitting. Moisture accumulating in the insulation material resulted in corrosion and failure of external braiding of the flexible hose.
The maintenance regime of flexible hoses installed on retractable probes only included minor pressure testing and replacement of O-rings and seals. External insulation of flexible hoses restricted visual inspection.
Flexible hoses on retractable probes had been in service for up to 6 years without replacement.
Unavailability of acoustic gas detector data restricted the capability to identify the start time of the leak.
Difficulty in accessing pipeline delivery station information, including availability of emergency equipment, resulted in a minor delay in commencing depressurisation.
-
What did they learn?
Review processes for design, inspection and maintenance of flexible hoses in high pressure service to ensure that they consider the risk of failure due to chloride pitting.
-
Ask yourself or your crew
Do you have flexible hoses in high pressure service at your workplace? Are you involved in designing flexible hose assemblies, or in inspecting and maintaining them? Have you adequately considered the risk of failure due to chloride pitting?
Is there a flexible hose management plan in place at your workplace? Does it adequately address the risk of failure due to chloride pitting?
How do you check the integrity of flexible hoses in high pressure service? How would you report any integrity concerns that you identified?
How would you know if a flexible hose is leaking? How would you respond if you noticed a leak?
Add to homescreen
Content name
Select existing category:
Content name
New collection
Edit collection
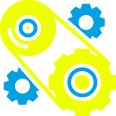
What happened?
When operators entered the pipeline delivery station to a liquefied natural gas (LNG) plant for training and familiarisation, they could hear a gas leak.
They found a braided flexible hose was leaking on a sample line tubing to sampling probe on the metering skid.
The leak was visible with a gas cloud extending about 2m3 (71 cubic feet) from the sample line tubing.
The leak rate was estimated to be 60kg/hr (132lbs/hr). The total volume of the leak is unknown.
Operators notified the control room and leadership team. The area was isolated immediately and vented to zero making the work area safe.
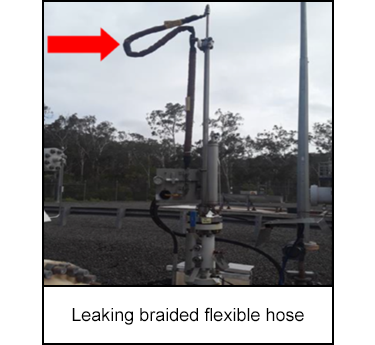
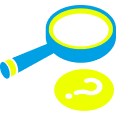
Why did it happen?
The retractable probe design required use of flexible hoses in high pressure service.
Material used for retractable probe flexible hose (304 stainless steel) was susceptible to chloride pitting. Moisture accumulating in the insulation material resulted in corrosion and failure of external braiding of the flexible hose.
The maintenance regime of flexible hoses installed on retractable probes only included minor pressure testing and replacement of O-rings and seals. External insulation of flexible hoses restricted visual inspection.
Flexible hoses on retractable probes had been in service for up to 6 years without replacement.
Unavailability of acoustic gas detector data restricted the capability to identify the start time of the leak.
Difficulty in accessing pipeline delivery station information, including availability of emergency equipment, resulted in a minor delay in commencing depressurisation.
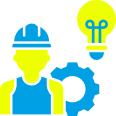
What did they learn?
Review processes for design, inspection and maintenance of flexible hoses in high pressure service to ensure that they consider the risk of failure due to chloride pitting.
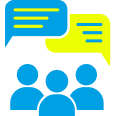
Ask yourself or your crew
Do you have flexible hoses in high pressure service at your workplace? Are you involved in designing flexible hose assemblies, or in inspecting and maintaining them? Have you adequately considered the risk of failure due to chloride pitting?
Is there a flexible hose management plan in place at your workplace? Does it adequately address the risk of failure due to chloride pitting?
How do you check the integrity of flexible hoses in high pressure service? How would you report any integrity concerns that you identified?
How would you know if a flexible hose is leaking? How would you respond if you noticed a leak?
During a training session at a pipeline delivery station for a liquefied natural gas (LNG) plant, operators detected a gas leak from a flexible hose on a sample line. The area was promptly isolated and vented to ensure safety, with the leak rate estimated at 60kg/hr (132lbs/hr) and a visible gas cloud extending about 2m³ (71 cubic feet).
Original material courtesy of Safer Together (Australia)
To access the PDF and PowerPoint versions, please visit https://www.safertogether.com.au/resources/sharing-library/operating-process-equipment-loss-of-containment-may-2023