-
What happened?
During the start-up of the gas injection compressor (GIC1), a Tier 1 gas leak occurred on the seal gas filter inside an enclosed module. Shutdown was initiated, and field personnel mustered without further consequences. The incident unfolded as follows:
- Seal gas preconditioning skid filter underwent planned maintenance, including O-ring replacement.
- Silicone grease was applied to some flanges to hold the O-ring in place due to difficulties during installation.
- Nitrogen (N2) leak test was conducted, but the test pressure (120 bar) was lower than the actual operating pressure (150 bar).
- Upon start-up of the gas injection compressor system (GIC1), a gas leak occurred inside an enclosed module.
- Operations personnel promptly initiated a shutdown of GIC1.
- Multiple gas detectors activated and initiated an ES2 (shutting down the main electrical bus to the module) but did not initiate GIC1 blowdown on confirmed gas.
- Field personnel mustered.
- GIC1 blowdown was manually initiated from the programmable logic controller (PLC).
- Gas was dispersed by the ventilation system without further consequences.
-
Why did it happen?
The skid configuration required significant manual handling of flanges during O-ring installation, leading to the application of silicone grease on some flanges. This likely contributed to O-ring extrusion and failure.
The N2 leak test was conducted at a lower pressure (120 bar) than the actual operating pressure (150 bar), which did not accurately simulate real-world conditions.
The Emergency Shutdown (ESD2) logic system failed to initiate the GIC1 compressor blowdown despite the confirmation of gas presence. Additionally, there was no capability to manually initiate blowdown from the distributed control system (DCS) and the logic had been modified since the system's initial startup.
-
What did they learn?
Ensure that clear and accessible procedures and instructions are provided for working on vendor packages.
Establish a quality control (QC) process to guarantee the use of correct spares and materials, and to ensure that work is carried out correctly.
Ensure that workers are competent to conduct the task, and adequate tools and resources are available for the job.
Verify that workers are qualified and confident to execute complex, non-routine activities (slowdowns, shutdowns, complex isolations, and de-isolations, etc.).
Thoroughly understand and execute equipment leak tests and pressure tests as required.
Familiarise yourself with the procedures in the event of a gas release or fire in the plant, and know the evacuation routes.
Be aware of the location of emergency shut down (ESD) buttons both in the field and in the control room.
-
Ask yourself or your crew
How can something like this happen here?
What precautions should be taken when applying silicone grease to flanges during O-ring installation? How do you prevent over-application or potential issues related to it?
Can you explain the importance of conducting leak tests at pressures that accurately simulate real-world operating conditions? How would you determine the appropriate test pressure for a specific component?
How familiar are you with the emergency shutdown (ESD2) logic system, and can you describe the steps involved in initiating a compressor blowdown in the event of a confirmed gas leak?
What measures do you take to verify the use of correct spares and materials during maintenance tasks, and how do you ensure that work is carried out according to specifications and procedures?
How do you stay informed about plant-specific emergency procedures, including responses to gas releases or fires, and are you familiar with evacuation routes in the event of an emergency?
Add to homescreen
Content name
Select existing category:
Content name
New collection
Edit collection
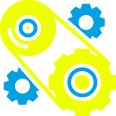
What happened?
During the start-up of the gas injection compressor (GIC1), a Tier 1 gas leak occurred on the seal gas filter inside an enclosed module. Shutdown was initiated, and field personnel mustered without further consequences. The incident unfolded as follows:
- Seal gas preconditioning skid filter underwent planned maintenance, including O-ring replacement.
- Silicone grease was applied to some flanges to hold the O-ring in place due to difficulties during installation.
- Nitrogen (N2) leak test was conducted, but the test pressure (120 bar) was lower than the actual operating pressure (150 bar).
- Upon start-up of the gas injection compressor system (GIC1), a gas leak occurred inside an enclosed module.
- Operations personnel promptly initiated a shutdown of GIC1.
- Multiple gas detectors activated and initiated an ES2 (shutting down the main electrical bus to the module) but did not initiate GIC1 blowdown on confirmed gas.
- Field personnel mustered.
- GIC1 blowdown was manually initiated from the programmable logic controller (PLC).
- Gas was dispersed by the ventilation system without further consequences.
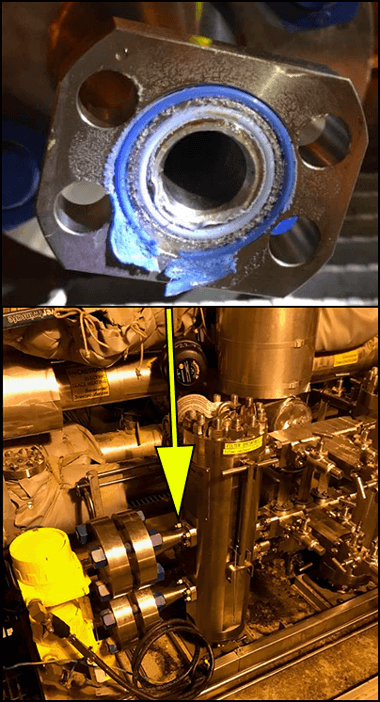
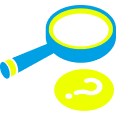
Why did it happen?
The skid configuration required significant manual handling of flanges during O-ring installation, leading to the application of silicone grease on some flanges. This likely contributed to O-ring extrusion and failure.
The N2 leak test was conducted at a lower pressure (120 bar) than the actual operating pressure (150 bar), which did not accurately simulate real-world conditions.
The Emergency Shutdown (ESD2) logic system failed to initiate the GIC1 compressor blowdown despite the confirmation of gas presence. Additionally, there was no capability to manually initiate blowdown from the distributed control system (DCS) and the logic had been modified since the system's initial startup.
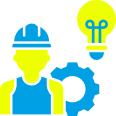
What did they learn?
Ensure that clear and accessible procedures and instructions are provided for working on vendor packages.
Establish a quality control (QC) process to guarantee the use of correct spares and materials, and to ensure that work is carried out correctly.
Ensure that workers are competent to conduct the task, and adequate tools and resources are available for the job.
Verify that workers are qualified and confident to execute complex, non-routine activities (slowdowns, shutdowns, complex isolations, and de-isolations, etc.).
Thoroughly understand and execute equipment leak tests and pressure tests as required.
Familiarise yourself with the procedures in the event of a gas release or fire in the plant, and know the evacuation routes.
Be aware of the location of emergency shut down (ESD) buttons both in the field and in the control room.
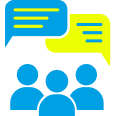
Ask yourself or your crew
How can something like this happen here?
What precautions should be taken when applying silicone grease to flanges during O-ring installation? How do you prevent over-application or potential issues related to it?
Can you explain the importance of conducting leak tests at pressures that accurately simulate real-world operating conditions? How would you determine the appropriate test pressure for a specific component?
How familiar are you with the emergency shutdown (ESD2) logic system, and can you describe the steps involved in initiating a compressor blowdown in the event of a confirmed gas leak?
What measures do you take to verify the use of correct spares and materials during maintenance tasks, and how do you ensure that work is carried out according to specifications and procedures?
How do you stay informed about plant-specific emergency procedures, including responses to gas releases or fires, and are you familiar with evacuation routes in the event of an emergency?
During the start-up of the gas injection compressor (GIC1), a Tier 1 gas leak occurred on the seal gas filter inside an enclosed module. Shutdown was initiated, and field personnel mustered without further consequences.