-
What happened?
While changing over triethylene glycol (TEG) circulation pumps at a gas processing facility, a reverse flow of gas occurred through the standby pump recycle line, dislodging a 12kg (26lbs) screen pot from the top of the column. This resulted in:
- The screen pot falling to the ground from a height of about 10m (33 feet), coming to rest approximately 3m (10 feet) from where an operator was standing.
- A Tier 2 loss of containment of methane gas from the reflux condenser column. Gas continued to vent through the top of the column for several minutes until operators remotely shutdown the TEG unit, isolating and depressurising it.
-
Why did it happen?
Uncontrolled reverse flow of high pressure methane gas from top of TEG contactor to still column.
TEG skid was operating with a screen pot that was sitting loose since it was constructed.
-
What did they learn?
Ensure transient / abnormal operations that are considered routine operations are reviewed during process hazard analysis (PHA) studies to manage loss of containment risks to as low as reasonably practicable (ALARP).
Review maintenance documentation during the management of work process, and the pre-start safety review process prior to recommissioning /restarting assets.
Rehearsing operator frontline responses is key to enabling safe behaviours during process emergencies.
A robust management of change process during projects is a critical control to ensure newly introduced hazards are identified and risks are managed to ALARP post-design stage.
-
Ask yourself or your crew
Do you have columns with screen pots at your worksite? Have you checked that screen pots are securely fastened?
Are you involved in conducting process hazard analysis (PHA) studies? Do you identify and review transient operations when conducting PHAs?
Do you review maintenance documentation in the pre-start safety review process prior to recommissioning / restarting assets?
Do you conduct regular emergency drills at your workplace to confirm your readiness to respond safely to a process emergency?
Add to homescreen
Content name
Select existing category:
Content name
New collection
Edit collection
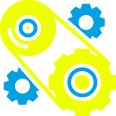
What happened?
While changing over triethylene glycol (TEG) circulation pumps at a gas processing facility, a reverse flow of gas occurred through the standby pump recycle line, dislodging a 12kg (26lbs) screen pot from the top of the column. This resulted in:
- The screen pot falling to the ground from a height of about 10m (33 feet), coming to rest approximately 3m (10 feet) from where an operator was standing.
- A Tier 2 loss of containment of methane gas from the reflux condenser column. Gas continued to vent through the top of the column for several minutes until operators remotely shutdown the TEG unit, isolating and depressurising it.
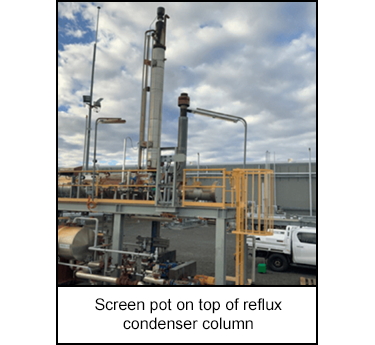
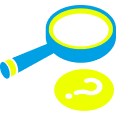
Why did it happen?
Uncontrolled reverse flow of high pressure methane gas from top of TEG contactor to still column.
TEG skid was operating with a screen pot that was sitting loose since it was constructed.
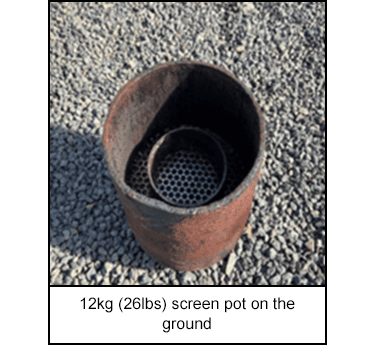
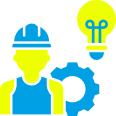
What did they learn?
Ensure transient / abnormal operations that are considered routine operations are reviewed during process hazard analysis (PHA) studies to manage loss of containment risks to as low as reasonably practicable (ALARP).
Review maintenance documentation during the management of work process, and the pre-start safety review process prior to recommissioning /restarting assets.
Rehearsing operator frontline responses is key to enabling safe behaviours during process emergencies.
A robust management of change process during projects is a critical control to ensure newly introduced hazards are identified and risks are managed to ALARP post-design stage.
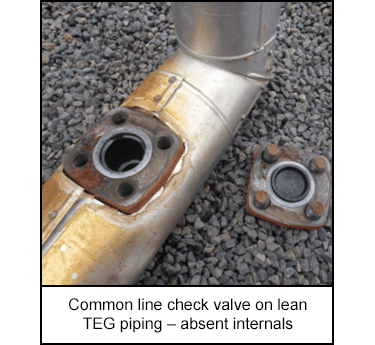
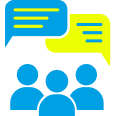
Ask yourself or your crew
Do you have columns with screen pots at your worksite? Have you checked that screen pots are securely fastened?
Are you involved in conducting process hazard analysis (PHA) studies? Do you identify and review transient operations when conducting PHAs?
Do you review maintenance documentation in the pre-start safety review process prior to recommissioning / restarting assets?
Do you conduct regular emergency drills at your workplace to confirm your readiness to respond safely to a process emergency?
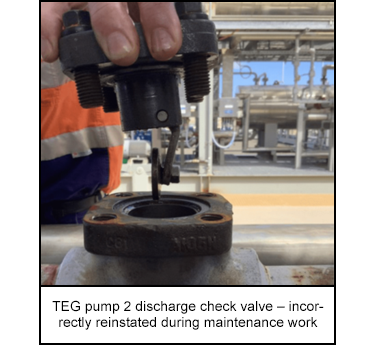
During a pump changeover at a gas processing facility, a reverse gas flow dislodged a 12kg (26lbs) screen pot, which fell 10m (33 feet) and landed 3m (10 feet) from an operator. This incident also caused a Tier 2 methane gas leak, which was controlled after operators shut down and depressurised the unit.
Original material courtesy of Safer Together (Australia)
To access the PDF and PowerPoint versions, please visit https://www.safertogether.com.au/resources/sharing-library/maintaining-process-equipment-loss-of-containment-leb-toolbox