-
What happened?
During light workover for through tubing plug and abandon (P&A), the moored vessel moved, resulting in the rupture of flange bolts beneath the workover blowout preventer (BOP).
The intervention was conducted with a moored rig on a production well that had been abandoned since 2010.
An unplanned movement of the rig caused the rupture of flange bolts connecting the workover BOP to the tree running tool.
The well was overbalanced with brine above a standing valve acting as the primary barrier.
After the event, a remotely operated vehicle (ROV) was used to close the wet X-Mas tree (XMT) swab valves to re-establish the secondary barrier envelope, as the valves were in override due to malfunction.
-
Why did it happen?
The immediate cause was the unplanned movement of the moored vessel, which led to the rupture of the flange bolts.
The underlying cause includes the use of a moored rig on a well that had been abandoned since 2010, which may have contributed to the instability.
The well was overbalanced with brine, which prevented a blowout, but if it had been underbalanced, a blowout could have occurred.
The malfunctioning of the wet XMT swab valves, which were in override, necessitated the use of an ROV to re-establish the secondary barrier.
-
What did they learn?
Map special scenarios where to apply riser analysis with anchored rig.
Implement new anchored rig position philosophy (reduce rig bridge team monitoring from 10% to 2% of water depth) + increase bull’s eyes frequency monitoring (from each 2 days to each 12 hours).
Create moored rig well specific operating guidelines, and propose actions for each operational state (advisory, yellow and red alert status).
-
Ask yourself or your crew
How can something like this happen here (e.g. on our site)?
What safety measures (i.e. procedures, controls/barriers) do we have in place to mitigate the risk?
How do we know the risk controls/barriers are working?
What improvements or changes should we make to the procedures, controls/barriers, or the way we work?
Add to homescreen
Content name
Select existing category:
Content name
New collection
Edit collection
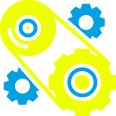
What happened?
During light workover for through tubing plug and abandon (P&A), the moored vessel moved, resulting in the rupture of flange bolts beneath the workover blowout preventer (BOP).
The intervention was conducted with a moored rig on a production well that had been abandoned since 2010.
An unplanned movement of the rig caused the rupture of flange bolts connecting the workover BOP to the tree running tool.
The well was overbalanced with brine above a standing valve acting as the primary barrier.
After the event, a remotely operated vehicle (ROV) was used to close the wet X-Mas tree (XMT) swab valves to re-establish the secondary barrier envelope, as the valves were in override due to malfunction.
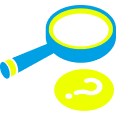
Why did it happen?
The immediate cause was the unplanned movement of the moored vessel, which led to the rupture of the flange bolts.
The underlying cause includes the use of a moored rig on a well that had been abandoned since 2010, which may have contributed to the instability.
The well was overbalanced with brine, which prevented a blowout, but if it had been underbalanced, a blowout could have occurred.
The malfunctioning of the wet XMT swab valves, which were in override, necessitated the use of an ROV to re-establish the secondary barrier.
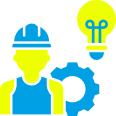
What did they learn?
Map special scenarios where to apply riser analysis with anchored rig.
Implement new anchored rig position philosophy (reduce rig bridge team monitoring from 10% to 2% of water depth) + increase bull’s eyes frequency monitoring (from each 2 days to each 12 hours).
Create moored rig well specific operating guidelines, and propose actions for each operational state (advisory, yellow and red alert status).
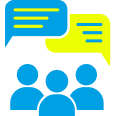
Ask yourself or your crew
How can something like this happen here (e.g. on our site)?
What safety measures (i.e. procedures, controls/barriers) do we have in place to mitigate the risk?
How do we know the risk controls/barriers are working?
What improvements or changes should we make to the procedures, controls/barriers, or the way we work?
During a light workover for through tubing plug and abandon (P&A) on an offshore production well, an unplanned movement of the moored rig caused a rupture in the flange bolts beneath the workover blowout preventer (BOP), risking a blowout if the well had been underbalanced. The incident was mitigated by using a remotely operated vehicle (ROV) to close malfunctioning swab valves and re-establish the secondary barrier.