-
What happened?
During operations, two heaters (A and B) were online and actively functioning, while a third heater (C) remained on standby. The fractionation plant encountered an increased demand for hot oil.
The heater outlet temperature fell below the set point and the control system increased its fuel gas supply pressure to the heater.
The panel operator increased the ethane content of fuel gas to increase the calorific value of fuel.
Operations mobilised to heaters and surveillance was conducted, which identified that two burners were behaving abnormally, firebox pressure was positive, and carbon monoxide was detected by personal gas badges.
Operations brought heater C online and shut-in the affected burners in heater A.
-
Why did it happen?
Heater flooding resulted in incomplete combustion due to insufficient air, which resulted in unburned fuel in the firebox, causing the potential for an explosion to take place.
The flooding hazard was not recognised or managed.
Training enhancements were required to prevent, identify, and respond to flooding.
The heater design does not include excess oxygen / combustible analysers, automatic fuel gas control, or manual natural draft control.
-
What did they learn?
Ensure that heater outlet temperature does not fall below set point.
Enhance training to ensure that staff are able to recognise and manage flooding hazards in order to prevent, identify, and respond to flooding.
Adjust the heater design so that it includes excess oxygen / combustible analysers, automatic fuel gas control, and manual natural draft control.
-
Ask yourself or your crew
How might the plant's operating modes lead us into situations that aren't safe for us?
What is the appropriate response is to a heater flooding event?
How can you ensure that process safety insights from other facilities / industry are effectively shared, understood and acted on?
How do you identify all the hazards associated with your operations and develop effective plans to manage the risks?
What improvements or changes should we make to the procedures, controls/barriers, or the way we work?
Add to homescreen
Content name
Select existing category:
Content name
New collection
Edit collection
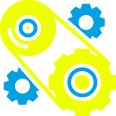
What happened?
During operations, two heaters (A and B) were online and actively functioning, while a third heater (C) remained on standby. The fractionation plant encountered an increased demand for hot oil.
The heater outlet temperature fell below the set point and the control system increased its fuel gas supply pressure to the heater.
The panel operator increased the ethane content of fuel gas to increase the calorific value of fuel.
Operations mobilised to heaters and surveillance was conducted, which identified that two burners were behaving abnormally, firebox pressure was positive, and carbon monoxide was detected by personal gas badges.
Operations brought heater C online and shut-in the affected burners in heater A.
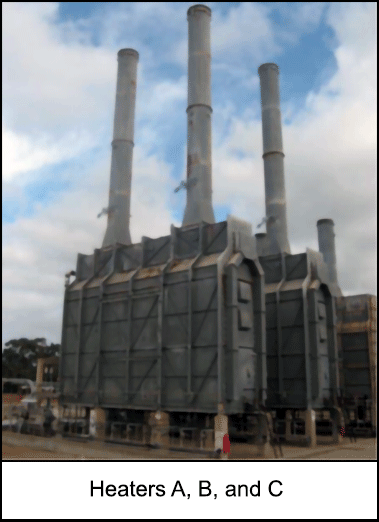
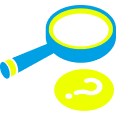
Why did it happen?
Heater flooding resulted in incomplete combustion due to insufficient air, which resulted in unburned fuel in the firebox, causing the potential for an explosion to take place.
The flooding hazard was not recognised or managed.
Training enhancements were required to prevent, identify, and respond to flooding.
The heater design does not include excess oxygen / combustible analysers, automatic fuel gas control, or manual natural draft control.
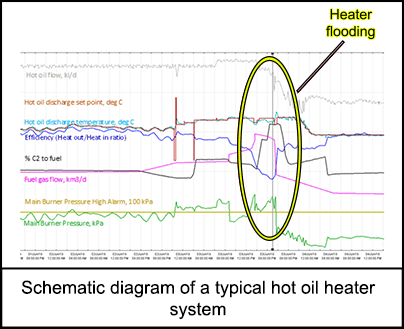
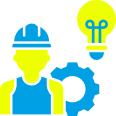
What did they learn?
Ensure that heater outlet temperature does not fall below set point.
Enhance training to ensure that staff are able to recognise and manage flooding hazards in order to prevent, identify, and respond to flooding.
Adjust the heater design so that it includes excess oxygen / combustible analysers, automatic fuel gas control, and manual natural draft control.
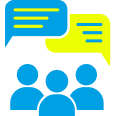
Ask yourself or your crew
How might the plant's operating modes lead us into situations that aren't safe for us?
What is the appropriate response is to a heater flooding event?
How can you ensure that process safety insights from other facilities / industry are effectively shared, understood and acted on?
How do you identify all the hazards associated with your operations and develop effective plans to manage the risks?
What improvements or changes should we make to the procedures, controls/barriers, or the way we work?
During operations, two heaters (A and B) were online and actively functioning, while a third heater (C) remained on standby. The fractionation plant encountered an increased demand for hot oil. Two heater burners were behaving abnormally, indicated by positive firebox pressure and detection of carbon monoxide detected by personal gas badges.