-
What happened?
A two-person truck crew was loading a rig mat onto a Texas bed truck.
An initial loading attempt was unsuccessful due to misalignment between the position of the truck and the rig mat. This contributed to the rig mat contacting a deck pin on the truck bed during the lift. The rig mat was lowered so the winch line could be repositioned.
During the second load attempt, the driver engaged the winch while the other crew member was still handling the winch line/deck chains.
The crew member’s fingers were trapped between the winch line and truck bed roller.
The injured crew member suffered serious injuries to their index and middle fingers.
-
Why did it happen?
The truck’s initial position was not centred with the load.
During the second loading attempt, the driver saw another worker from the same company with similar coveralls walking away from the rear of the truck and mistakenly thought his assistant was clear of the load and winch line.
The winch was controlled from inside the truck cab with no clear line of sight to the rear of the
vehicle.
The winch was engaged without any visual or verbal communication between the crew members.
-
What did they learn?
Accurate vehicle positioning is important for safe and effective loading operations.
Review winch truck training orientation and identify safety critical tasks.
Confirm all employees are trained and competent to perform assigned duties.
Verify all personnel are in a safe zone before lifting or winching operations begin.
-
Ask yourself or your crew
How could something like this happen here?
What other actions could have been taken?
How do crew members communicate during lifting and winching operations?
How do you confirm everyone is in a safe zone before lifting?
Where is the safe zone?
Add to homescreen
Content name
Select existing category:
Content name
New collection
Edit collection
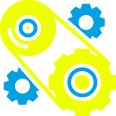
What happened?
A two-person truck crew was loading a rig mat onto a Texas bed truck.
An initial loading attempt was unsuccessful due to misalignment between the position of the truck and the rig mat. This contributed to the rig mat contacting a deck pin on the truck bed during the lift. The rig mat was lowered so the winch line could be repositioned.
During the second load attempt, the driver engaged the winch while the other crew member was still handling the winch line/deck chains.
The crew member’s fingers were trapped between the winch line and truck bed roller.
The injured crew member suffered serious injuries to their index and middle fingers.
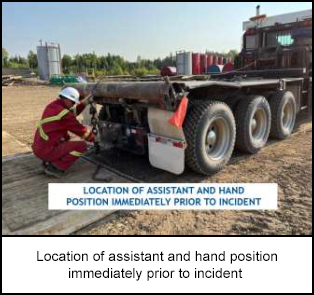
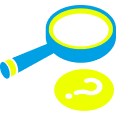
Why did it happen?
The truck’s initial position was not centred with the load.
During the second loading attempt, the driver saw another worker from the same company with similar coveralls walking away from the rear of the truck and mistakenly thought his assistant was clear of the load and winch line.
The winch was controlled from inside the truck cab with no clear line of sight to the rear of the
vehicle.
The winch was engaged without any visual or verbal communication between the crew members.
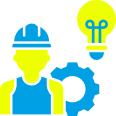
What did they learn?
Accurate vehicle positioning is important for safe and effective loading operations.
Review winch truck training orientation and identify safety critical tasks.
Confirm all employees are trained and competent to perform assigned duties.
Verify all personnel are in a safe zone before lifting or winching operations begin.
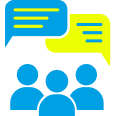
Ask yourself or your crew
How could something like this happen here?
What other actions could have been taken?
How do crew members communicate during lifting and winching operations?
How do you confirm everyone is in a safe zone before lifting?
Where is the safe zone?
A truck crew member's fingers were seriously injured during a loading operation when the winch was engaged while they were handling the winch line. Misalignment and miscommunication contributed to the incident.
Original material courtesy of Energy Safety Canada