-
What happened?
A compounding line was stopped for cleaning, which was carried out by two assigned technicians. They used a water hose for spraying water inside the hopper to remove residual fines prior to grade change.
Technician A proceeded to clean the bottom hopper and technician B the top hopper.
As part of the cleaning process, technician A opened the box covers for magnetic filter and slide valve of the bottom hopper.
Technician A sprayed water using the water hose, and when technician B stopped and removed the hose, the slide valve suddenly closed.
As a result, technician A’s ring finger was caught in between the slide valve and approximately 1.5 cm (0.6 inch) of the first phalanx was severed.
The injured technician was treated by the company doctor and sent to the hospital for further treatment. He was discharged on the same day and given 3 days of medical leave.
-
Why did it happen?
Immediate causes:
- failure to follow the practices;
- failure to identify hazard.
Root causes:
- inadequate work procedure;
- inadequate hazard identification and risk assessment;
- lack of situational awareness.
Notes:
Technician A claimed to be wearing gloves during the incident.
Technician A had been working with the company or approximately 10 years in the compounding section and had done this cleaning operation approximately 100 times by their reckoning.
-
What did they learn?
Install signage at magnetic filters and slide valve boxes to caution people from opening unless authorised by operations manager and/or health, safety, environment, and quality (HSEQ) manager.
Personnel should always adhere to established safety guidelines and regulations by wearing the necessary personal protective equipment (PPE) suitable for the tasks they are performing.
Consider updating work procedures to enhance safety.
Review risk assessment to ensure inclusion of Lock-Out-Tag-Out (LOTO) procedure for pneumatic energy.
Communicate work procedure, hazard, and risk control measures to all concerned.
Identify and address similar risks in other areas of the plant.
-
Ask yourself or your crew
How can something like this happen here?
When performing maintenance or cleaning tasks, how do you know which technical manuals and procedures you should refer to when carrying out maintenance/cleaning tasks?
What specific actions can you and your team take to improve hazard identification and risk assessment processes in our work environment?
What measures do we have in place to prevent similar incidents on our site? What else can we do to enhance safety in your workplace?
Add to homescreen
Content name
Select existing category:
Content name
New collection
Edit collection
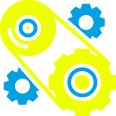
What happened?
A compounding line was stopped for cleaning, which was carried out by two assigned technicians. They used a water hose for spraying water inside the hopper to remove residual fines prior to grade change.
Technician A proceeded to clean the bottom hopper and technician B the top hopper.
As part of the cleaning process, technician A opened the box covers for magnetic filter and slide valve of the bottom hopper.
Technician A sprayed water using the water hose, and when technician B stopped and removed the hose, the slide valve suddenly closed.
As a result, technician A’s ring finger was caught in between the slide valve and approximately 1.5 cm (0.6 inch) of the first phalanx was severed.
The injured technician was treated by the company doctor and sent to the hospital for further treatment. He was discharged on the same day and given 3 days of medical leave.
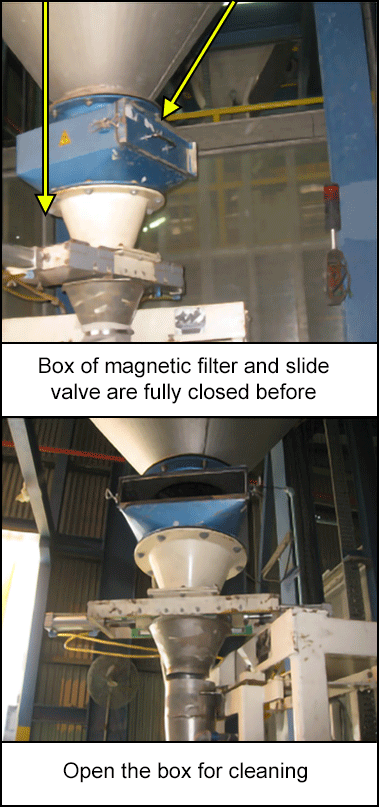
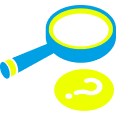
Why did it happen?
Immediate causes:
- failure to follow the practices;
- failure to identify hazard.
Root causes:
- inadequate work procedure;
- inadequate hazard identification and risk assessment;
- lack of situational awareness.
Notes:
Technician A claimed to be wearing gloves during the incident.
Technician A had been working with the company or approximately 10 years in the compounding section and had done this cleaning operation approximately 100 times by their reckoning.
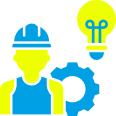
What did they learn?
Install signage at magnetic filters and slide valve boxes to caution people from opening unless authorised by operations manager and/or health, safety, environment, and quality (HSEQ) manager.
Personnel should always adhere to established safety guidelines and regulations by wearing the necessary personal protective equipment (PPE) suitable for the tasks they are performing.
Consider updating work procedures to enhance safety.
Review risk assessment to ensure inclusion of Lock-Out-Tag-Out (LOTO) procedure for pneumatic energy.
Communicate work procedure, hazard, and risk control measures to all concerned.
Identify and address similar risks in other areas of the plant.
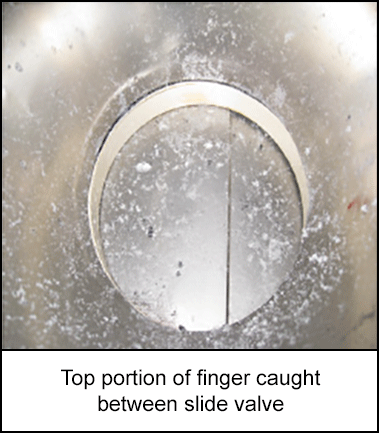
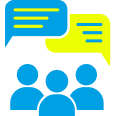
Ask yourself or your crew
How can something like this happen here?
When performing maintenance or cleaning tasks, how do you know which technical manuals and procedures you should refer to when carrying out maintenance/cleaning tasks?
What specific actions can you and your team take to improve hazard identification and risk assessment processes in our work environment?
What measures do we have in place to prevent similar incidents on our site? What else can we do to enhance safety in your workplace?
A technician was cleaning a compounding line and, after removing the water hose, the slide valve suddenly closed. The technician’s ring finger was caught in between the slide valve and approximately 1.5 cm (0.6 inch) of the first phalanx was severed.