-
What happened?
A polyurethane foam bumper end stop from a maintenance crane was found on the deck of an offshore facility.
The bumper weighed about 5 kg (11 lbs) and had fallen approximately 9 metres (30 feet) from the work basket guide rails of the crane.
Subsequent inspections revealed that a second a second bumper on the aft side of the same guide rail was also missing.
Dropped object prevention scheme (DROPS) calculations indicate this incident could have had a fatal consequence.
-
Why did it happen?
The bumper had remained in-situ and out of service since it was installed in 2017.
The fallen bumper had become brittle due to prolonged exposure to the sun (ultraviolet light).
The strength of the bumper material was degraded and insufficient to resist the bumper’s own weight, resulting in detachment from the assembly plate.
Strong winds may have contributed to detachment.
A decision note prepared in 2019 to decommission the crane by 2023 included recommended actions to make the crane safe in the interim period.
Actions to inspect the crane for any loose objects were outstanding.
-
What did they learn?
Proposed actions from the crane decommissioning decision note could not be traced to a structured maintenance program or executable work order.
Technical recommendations need to be translated into execution actions.
Existing risk-based inspections or pre-start-up inspection programs do not mandate the inspection of equipment that is not scheduled for commissioning.
These inspections are focused on safety critical lifting & hoisting equipment, or equipment that will be commissioned.
-
Ask yourself or your crew
Do you have unused equipment awaiting decommissioning at your site / facility? How long is it since the equipment was last used? Does your maintenance program include inspection of equipment awaiting decommissioning to confirm its structural integrity?
What risks exist for overhead equipment that has not been commissioned, or is awaiting decommissioning, that can result in a dropped object event? How are these risks managed?
What processes are in place at your site / facility to translate identified technical recommendations into executable actions?
When a potential dropped object is identified, do you and your work mates discuss the “what if” question? (e.g. What if that falls – could it hit people or plant? What is the worst outcome if it did?).
Add to homescreen
Content name
Select existing category:
Content name
New collection
Edit collection
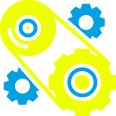
What happened?
A polyurethane foam bumper end stop from a maintenance crane was found on the deck of an offshore facility.
The bumper weighed about 5 kg (11 lbs) and had fallen approximately 9 metres (30 feet) from the work basket guide rails of the crane.
Subsequent inspections revealed that a second a second bumper on the aft side of the same guide rail was also missing.
Dropped object prevention scheme (DROPS) calculations indicate this incident could have had a fatal consequence.
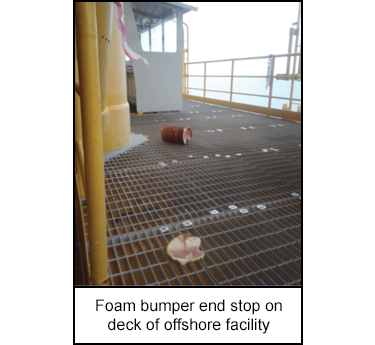
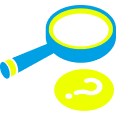
Why did it happen?
The bumper had remained in-situ and out of service since it was installed in 2017.
The fallen bumper had become brittle due to prolonged exposure to the sun (ultraviolet light).
The strength of the bumper material was degraded and insufficient to resist the bumper’s own weight, resulting in detachment from the assembly plate.
Strong winds may have contributed to detachment.
A decision note prepared in 2019 to decommission the crane by 2023 included recommended actions to make the crane safe in the interim period.
Actions to inspect the crane for any loose objects were outstanding.
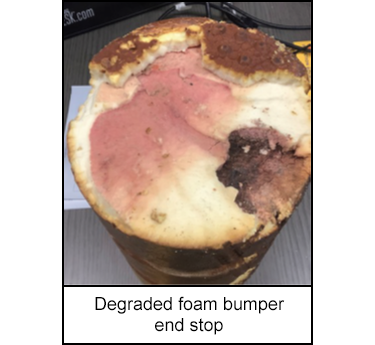
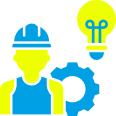
What did they learn?
Proposed actions from the crane decommissioning decision note could not be traced to a structured maintenance program or executable work order.
Technical recommendations need to be translated into execution actions.
Existing risk-based inspections or pre-start-up inspection programs do not mandate the inspection of equipment that is not scheduled for commissioning.
These inspections are focused on safety critical lifting & hoisting equipment, or equipment that will be commissioned.
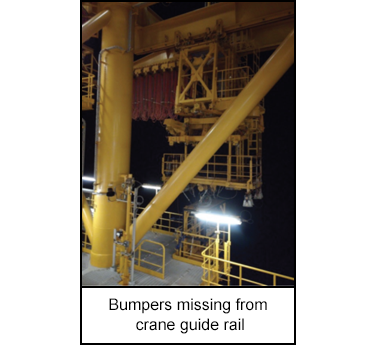
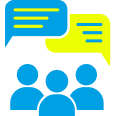
Ask yourself or your crew
Do you have unused equipment awaiting decommissioning at your site / facility? How long is it since the equipment was last used? Does your maintenance program include inspection of equipment awaiting decommissioning to confirm its structural integrity?
What risks exist for overhead equipment that has not been commissioned, or is awaiting decommissioning, that can result in a dropped object event? How are these risks managed?
What processes are in place at your site / facility to translate identified technical recommendations into executable actions?
When a potential dropped object is identified, do you and your work mates discuss the “what if” question? (e.g. What if that falls – could it hit people or plant? What is the worst outcome if it did?).
A 5 kg (11 lbs) polyurethane foam bumper end stop fell approximately 9 metres (30 feet) from a maintenance crane's work basket guide rails on an offshore facility. Subsequent inspections revealed another bumper was also missing, and DROPS calculations indicated the incident could have had fatal consequences.
Original material courtesy of Safer Together (Australia)
To access the PDF and PowerPoint versions, please visit https://www.safertogether.com.au/resources/sharing-library/working-on-near-fixed-equipment-person-in-line-of-fire