-
What happened?
A compressor was shut down for pressure safety valves (PSV) recertification.
After the restart, the PSV activated at a pressure lower than the intended set pressure of 5800 pounds per square inch gauge (psig).
The typical operating pressure is 5000 psig, but at the time of the incident, it was much lower at 2000 psig.
After the PSV recertification, there were difficulties in putting it back into place because the pipes were not properly aligned.
The piping for the pressure relief valve failed, and the isolation valve body (rated at ANSI 150) also split into two pieces.
When the PSV activated, there was a loud noise that the plant operator heard, followed by the release of a gas cloud.
The 3-foot-long piping that connects to the PSV broke at a 16-foot-long header connection. This happened due to forces acting in the opposite direction.
The failed piping assembly travelled about 6 metres (19.5 feet) before hitting a structural beam. impacting a vertical structural beam.
After these events, personnel promptly activated the emergency shutdown.
-
Why did it happen?
The pressure was 3000psig less than normal operating pressure, indicating a potential issue with the PSV's functionality or calibration.
The PSV discharge valve was suspected to be in a closed position. This indicates a failure in safety procedures.
The car seal tags (crucial for indicating the status of PSV isolation valves) were absent from PSV isolation valves.
-
What did they learn?
Verify the effectiveness of car seals to assure the availability of a relief path.
Ensure that PSV recertifications are executed effectively and that quality standards are followed during the process.
Establish and follow a Quality Assurance/Quality Control (QA/QC) process for PSV recertification and installation to prevent similar incidents from happening.
-
Ask yourself or your crew
How can something like this happen here?
How can you verify:
- the effectiveness of car seals to assure their relief path availability?
- that the PSV discharge valve is in the correct position before operation?
How can we enhance our monitoring and verification processes to prevent misalignment issues during PSV reinstallation?
Are there any additional measures we should consider ensuring that PSV discharge valves are in the correct position before startup?
Can you describe the current quality assurance and quality control (QA/QC) process in place for PSV recertification and installation? Are there any gaps or areas that need improvement in this process?
Add to homescreen
Content name
Select existing category:
Content name
New collection
Edit collection
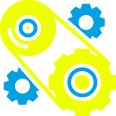
What happened?
A compressor was shut down for pressure safety valves (PSV) recertification.
After the restart, the PSV activated at a pressure lower than the intended set pressure of 5800 pounds per square inch gauge (psig).
The typical operating pressure is 5000 psig, but at the time of the incident, it was much lower at 2000 psig.
After the PSV recertification, there were difficulties in putting it back into place because the pipes were not properly aligned.
The piping for the pressure relief valve failed, and the isolation valve body (rated at ANSI 150) also split into two pieces.
When the PSV activated, there was a loud noise that the plant operator heard, followed by the release of a gas cloud.
The 3-foot-long piping that connects to the PSV broke at a 16-foot-long header connection. This happened due to forces acting in the opposite direction.
The failed piping assembly travelled about 6 metres (19.5 feet) before hitting a structural beam. impacting a vertical structural beam.
After these events, personnel promptly activated the emergency shutdown.
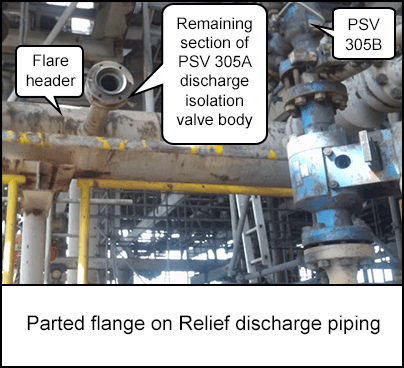
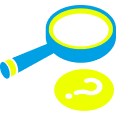
Why did it happen?
The pressure was 3000psig less than normal operating pressure, indicating a potential issue with the PSV's functionality or calibration.
The PSV discharge valve was suspected to be in a closed position. This indicates a failure in safety procedures.
The car seal tags (crucial for indicating the status of PSV isolation valves) were absent from PSV isolation valves.
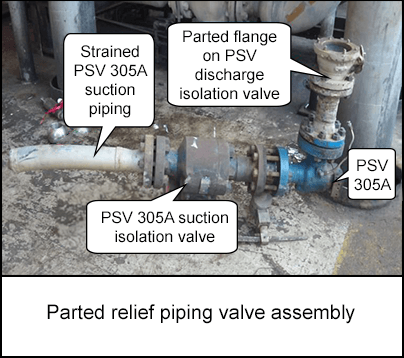
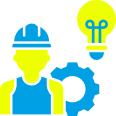
What did they learn?
Verify the effectiveness of car seals to assure the availability of a relief path.
Ensure that PSV recertifications are executed effectively and that quality standards are followed during the process.
Establish and follow a Quality Assurance/Quality Control (QA/QC) process for PSV recertification and installation to prevent similar incidents from happening.
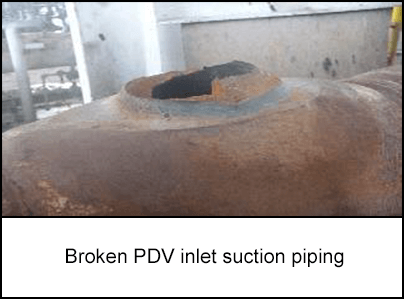
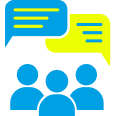
Ask yourself or your crew
How can something like this happen here?
How can you verify:
- the effectiveness of car seals to assure their relief path availability?
- that the PSV discharge valve is in the correct position before operation?
How can we enhance our monitoring and verification processes to prevent misalignment issues during PSV reinstallation?
Are there any additional measures we should consider ensuring that PSV discharge valves are in the correct position before startup?
Can you describe the current quality assurance and quality control (QA/QC) process in place for PSV recertification and installation? Are there any gaps or areas that need improvement in this process?
During a compressor shutdown for pressure safety valve (PSV) recertification, the PSV activated at a lower pressure than intended (2000 psig instead of 5800 psig). This was due to misaligned pipes, leading to the failure of the relief valve piping assembly and the isolation valve body. The incident resulted in a loud noise, a gas release, and prompted the emergency shutdown process.