-
What happened?
In response to a manufacturer’s notification, a midstream company conducted an exposure assessment of hexavalent chromium in a previously unidentified location. This assessment identified the need for controls to prevent overexposure.
Chromium present in stainless steel may form as a residue on the exterior and sometimes interior engine or turbine components. This chromium is hexavalent (Cr6+), which is a carcinogen and a skin and respiratory sensitizer. It forms when metal in an oxidizing or corrosive environment is in contact with calcium oxide-containing materials, such as thread sealants or insulation. The generation of Cr6+ increases at elevated temperatures and often appears as a yellow or white residue on engine components and adjacent insulation surfaces.
-
Why did it happen?
- The presence of this residue and how it is produced was not known until the last few years.
- The residue may often be mistaken for sulfur and can be difficult to see with typical sodium lights.
- Exposure may occur if the residue is disturbed during tasks such as sampling, maintenance activities, or hot work like grinding and welding.
- Routes of exposure include inhalation, skin contact and ingestion.
- Cr6+ has very low airborne exposure limits such as 0.0002 mg/m3 or 0.01 mg/m3, depending on the jurisdiction.
-
What did they learn?
- Determine if stainless-steel components combined with calcium oxide-containing materials and elevated temperatures are present in your operations.
- Implement an exposure control plan (ECP) to protect personnel when suspected or confirmed Cr6+-containing residues may be present.
- Conduct visual inspections and testing (wipe sample or colorimetric swab) for presence of Cr6+.
- The use of a 10% citric or ascorbic acid water/soap mixture can transform (~15 minutes) the hexavalent chromium to its’ trivalent form (Cr3+), which is less toxic and, when wet, less likely to be airborne. Ensure the acid water/soap mixture is removed from the metal to avoid future chromium residue generation.
- When chromium residue may be disturbed, use personal protective equipment—such as respirators equipped with P100 filters, disposable suits, and nitrile gloves—combined with good hygiene practices.
-
Ask yourself or your crew
- How can something like this happen here (e.g. on our site)?
- What safety measures (i.e. procedures, controls/barriers) do we have in place to mitigate the risk?
- How do we know the risk controls/barriers are working?
- What improvements or changes should we make to the procedures, controls/barriers or the way we work?
Add to homescreen
Content name
Select existing category:
Content name
New collection
Edit collection
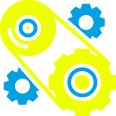
What happened?
In response to a manufacturer’s notification, a midstream company conducted an exposure assessment of hexavalent chromium in a previously unidentified location. This assessment identified the need for controls to prevent overexposure.
Chromium present in stainless steel may form as a residue on the exterior and sometimes interior engine or turbine components. This chromium is hexavalent (Cr6+), which is a carcinogen and a skin and respiratory sensitizer. It forms when metal in an oxidizing or corrosive environment is in contact with calcium oxide-containing materials, such as thread sealants or insulation. The generation of Cr6+ increases at elevated temperatures and often appears as a yellow or white residue on engine components and adjacent insulation surfaces.
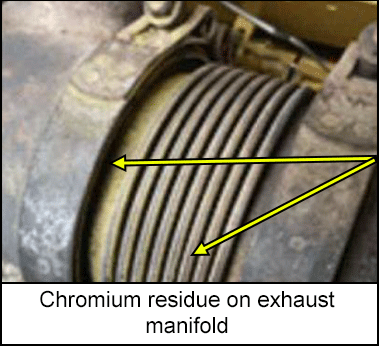
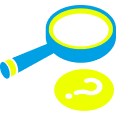
Why did it happen?
- The presence of this residue and how it is produced was not known until the last few years.
- The residue may often be mistaken for sulfur and can be difficult to see with typical sodium lights.
- Exposure may occur if the residue is disturbed during tasks such as sampling, maintenance activities, or hot work like grinding and welding.
- Routes of exposure include inhalation, skin contact and ingestion.
- Cr6+ has very low airborne exposure limits such as 0.0002 mg/m3 or 0.01 mg/m3, depending on the jurisdiction.
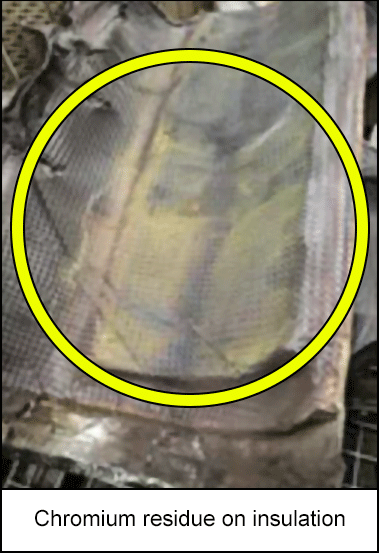
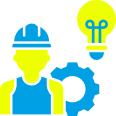
What did they learn?
- Determine if stainless-steel components combined with calcium oxide-containing materials and elevated temperatures are present in your operations.
- Implement an exposure control plan (ECP) to protect personnel when suspected or confirmed Cr6+-containing residues may be present.
- Conduct visual inspections and testing (wipe sample or colorimetric swab) for presence of Cr6+.
- The use of a 10% citric or ascorbic acid water/soap mixture can transform (~15 minutes) the hexavalent chromium to its’ trivalent form (Cr3+), which is less toxic and, when wet, less likely to be airborne. Ensure the acid water/soap mixture is removed from the metal to avoid future chromium residue generation.
- When chromium residue may be disturbed, use personal protective equipment—such as respirators equipped with P100 filters, disposable suits, and nitrile gloves—combined with good hygiene practices.
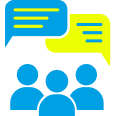
Ask yourself or your crew
- How can something like this happen here (e.g. on our site)?
- What safety measures (i.e. procedures, controls/barriers) do we have in place to mitigate the risk?
- How do we know the risk controls/barriers are working?
- What improvements or changes should we make to the procedures, controls/barriers or the way we work?
A midstream company conducted an exposure assessment of hexavalent chromium in a previously unidentified location. This assessment identified the need for controls to prevents overexposure. Chromium hexavalent (Cr6+) is a carcinogen and a skin and respiratory sensitizer. The generation of Cr6+ increases at elevated temperatures and often appears as a yellow or white residue on engine components and adjacent insulation surfaces.
Original material courtesy of Energy Safety Canada
Other resources:
Controlling Chemical Hazards Program
Developing an Exposure Control Plan Safety Bulletin
Fit for Duty Guideline
HRSG Forum, David Addison, Hexavalent Chromium in CCGT Plants - Presentation Video
Caterpillar Information Bulletin: Hexavalent Chromium on Engines
NIOSH Criteria for a Recommendation Standard for an Occupational Exposure to Hexavalent Chromium