-
What happened?
A Ruffneck-brand heater in a shack at a drilling work site experienced a static electricity rupture of the heat exchanger core. No one was injured because the crew had just completed their tasks for the day, but in slightly different circumstances crew members would have been present in the area where the explosion occurred.
The industry has reported several issues with Ruffneck heaters. In most cases, the root cause has been a lack of regular preventative maintenance.
-
Why did it happen?
- The pressure relief valve (PRV) had vented but had not been replaced or serviced as required.
- The PRV had a buildup of scale.
Contributing factors:
- Contact points on the contactor were welded together. As a result, the element and
motor were receiving constant power. - The use of “field gas” may have contributed to the buildup of scale.
- No preventive maintenance or inspections has been performed as per the original
equipment manufacturer (OEM).
-
What did they learn?
Ruffneck maintenance:
- Each owner’s manual has a maintenance checklist, and each heater should be regularly inspected and maintained. Maintenance should take place before every heating season.
- The heater is equipped with a single bimetal overtemperature high-limit. The heater should never be operated with the high-limit disabled or disconnected from the control circuit.
- Venting pressure of the PRV is factory-set; when it vents (pops) it must be removed from service and maintained.
- Do not tamper with or remove the warning label indicator on the PRV (see image).
General considerations:
- At minimum, ensure periodic maintenance is performed at the beginning each heating season.
- Look at pressure relief valves regularly to ensure there has been no venting. If you notice paper torn over the PRV, glycol on the heater or other deficiencies, take the heater out of service and replace the core.
- If you cannot locate the owner’s manual, you can download it from Ruffneck’s website.
-
Ask yourself or your crew
How can we prevent something like this from happening here?
What are other risks are associated with forklift operations? How can you mitigate those risks at your work site?
What safety recommendations should be included in the operational instructions?
How can we, as a company, implement a practical training plan that focuses on the job position, and make sure pedestrians are safer from forklifts in the future?
Add to homescreen
Content name
Select existing category:
Content name
New collection
Edit collection
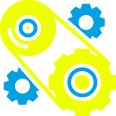
What happened?
A Ruffneck-brand heater in a shack at a drilling work site experienced a static electricity rupture of the heat exchanger core. No one was injured because the crew had just completed their tasks for the day, but in slightly different circumstances crew members would have been present in the area where the explosion occurred.
The industry has reported several issues with Ruffneck heaters. In most cases, the root cause has been a lack of regular preventative maintenance.

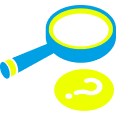
Why did it happen?
- The pressure relief valve (PRV) had vented but had not been replaced or serviced as required.
- The PRV had a buildup of scale.
Contributing factors:
- Contact points on the contactor were welded together. As a result, the element and
motor were receiving constant power. - The use of “field gas” may have contributed to the buildup of scale.
- No preventive maintenance or inspections has been performed as per the original
equipment manufacturer (OEM).
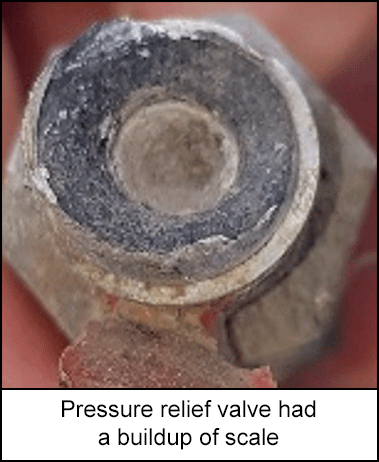
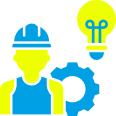
What did they learn?
Ruffneck maintenance:
- Each owner’s manual has a maintenance checklist, and each heater should be regularly inspected and maintained. Maintenance should take place before every heating season.
- The heater is equipped with a single bimetal overtemperature high-limit. The heater should never be operated with the high-limit disabled or disconnected from the control circuit.
- Venting pressure of the PRV is factory-set; when it vents (pops) it must be removed from service and maintained.
- Do not tamper with or remove the warning label indicator on the PRV (see image).
General considerations:
- At minimum, ensure periodic maintenance is performed at the beginning each heating season.
- Look at pressure relief valves regularly to ensure there has been no venting. If you notice paper torn over the PRV, glycol on the heater or other deficiencies, take the heater out of service and replace the core.
- If you cannot locate the owner’s manual, you can download it from Ruffneck’s website.
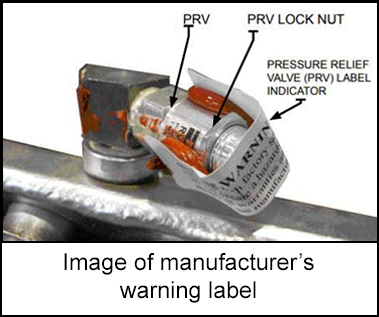
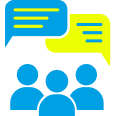
Ask yourself or your crew
How can we prevent something like this from happening here?
What are other risks are associated with forklift operations? How can you mitigate those risks at your work site?
What safety recommendations should be included in the operational instructions?
How can we, as a company, implement a practical training plan that focuses on the job position, and make sure pedestrians are safer from forklifts in the future?
A Ruffneck-brand heater in a shack at a drilling work site experienced a static electricity rupture of the heat exchanger core. No injuries as crew members had completed their tasks for the day. In other circumstances, crew members would have been present in the area where the explosion occurred. The industry as a whole has reported several issues with Ruffneck heaters. In most cases, the root cause has been lack of regular preventative maintenance.
Original material courtesy of Energy Safety Canada