-
What happened?
Setting plate on 40-ton MYT elevator found to be broken after string fell 8m. As a result of rapid lifting before the slips were fully set, the pipe collar was dropped onto the slip setting ring, and the full weight of the pipe damaged the elevators.
While only equipment was damaged, this incident could have potentially caused serious injury to rig personnel and damage other equipment.
-
Why did it happen?
- Slip dies heavily impacted with debris/ice/foreign material.
- Rapid lifting prior to the slips being fully set may have resulted in the pipe being dropped onto the slip setting ring with the full weight of the stand or string impacting the elevator.
Contributing factors:
- Lifting string without the slips being fully engaged can transfer weight to setting plate causing the setting ring to fail.
- Overloading or overpulling (example jarring operations); exceeding working load rating; or operations that have induced elevators to high accelerations; or high impact loads could have impact. The elevators should have been pulled out of service as soon as the elevator dies were shown to be worn.
- Y series elevators are to be used with a slip-setting ring in place and correctly sized for the tubular to achieve depression of the slip segments. Using the elevator with an incorrectly sized setting ring or no setting ring can result in damaging the elevator and could result in the pipe being dropped. The slips of Y series elevators will set when the elevator is raised against the tool joint, Collar Box upset, External upset end or load rated lift nubbin which pushes down on the slip-setting ring.
-
What did they learn?
Corrective actions:
- Make sure all slip segments are free in the “up” position when latching the elevator. If any of the segments are stuck in the down position, the elevator may not close properly.
- Make sure the elevator and slip bodies are used with the correct size tubular (per API specification). Oversized pipe will cause difficulties such as latching partially or not at all. Undersized or oversized pipe could cause uneven stress distribution, inadequate load bearing area, and possible wedging in the slip setting ring.
- Inspections, for both end user and service company, be conducted as outlined in CAODC Recommended Practice 4.0 Inspection and Certification of Overhead Equipment.
Third-party equipment corrective actions:
- Inspect and ensure all third-party equipment is complete and in good running conditions before sending them out.
- Qualified inspection personnel are to perform non-destructive testing. Load testing may be required as per original equipment manufacturer requirements. Elevators are produced from cast alloy heat-treated steel and must not be welded in the field. Improper welding can cause cracks and brittleness in heat-affected areas which can result in dramatic weakening of the part and possible failure.
- Equipment rental company developed notice to be sent with "Y" series elevators (rental or purchase) as part of the QA/QC certification documentation package. Outlined the importance of care/maintenance and warning against excessive running speeds.
-
Ask yourself or your crew
- How can something like this happen here (e.g. on our site)?
- What safety measures (i.e. procedures, controls/barriers) do we have in place to mitigate the risk?
- How do we know the risk controls/barriers are working?
- What improvements or changes should we make to the procedures, controls/barriers or the way we work?
Add to homescreen
If you want to add this app to home screen tap and then ‘Add to Home Screen’.
Content name
Select existing category:
Content name
New collection
Edit collection
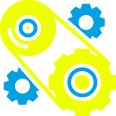
What happened?
Setting plate on 40-ton MYT elevator found to be broken after string fell 8m. As a result of rapid lifting before the slips were fully set, the pipe collar was dropped onto the slip setting ring, and the full weight of the pipe damaged the elevators.
While only equipment was damaged, this incident could have potentially caused serious injury to rig personnel and damage other equipment.
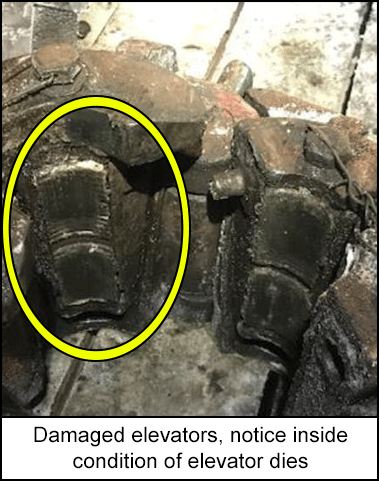
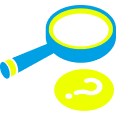
Why did it happen?
- Slip dies heavily impacted with debris/ice/foreign material.
- Rapid lifting prior to the slips being fully set may have resulted in the pipe being dropped onto the slip setting ring with the full weight of the stand or string impacting the elevator.
Contributing factors:
- Lifting string without the slips being fully engaged can transfer weight to setting plate causing the setting ring to fail.
- Overloading or overpulling (example jarring operations); exceeding working load rating; or operations that have induced elevators to high accelerations; or high impact loads could have impact. The elevators should have been pulled out of service as soon as the elevator dies were shown to be worn.
- Y series elevators are to be used with a slip-setting ring in place and correctly sized for the tubular to achieve depression of the slip segments. Using the elevator with an incorrectly sized setting ring or no setting ring can result in damaging the elevator and could result in the pipe being dropped. The slips of Y series elevators will set when the elevator is raised against the tool joint, Collar Box upset, External upset end or load rated lift nubbin which pushes down on the slip-setting ring.
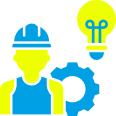
What did they learn?
Corrective actions:
- Make sure all slip segments are free in the “up” position when latching the elevator. If any of the segments are stuck in the down position, the elevator may not close properly.
- Make sure the elevator and slip bodies are used with the correct size tubular (per API specification). Oversized pipe will cause difficulties such as latching partially or not at all. Undersized or oversized pipe could cause uneven stress distribution, inadequate load bearing area, and possible wedging in the slip setting ring.
- Inspections, for both end user and service company, be conducted as outlined in CAODC Recommended Practice 4.0 Inspection and Certification of Overhead Equipment.
Third-party equipment corrective actions:
- Inspect and ensure all third-party equipment is complete and in good running conditions before sending them out.
- Qualified inspection personnel are to perform non-destructive testing. Load testing may be required as per original equipment manufacturer requirements. Elevators are produced from cast alloy heat-treated steel and must not be welded in the field. Improper welding can cause cracks and brittleness in heat-affected areas which can result in dramatic weakening of the part and possible failure.
- Equipment rental company developed notice to be sent with "Y" series elevators (rental or purchase) as part of the QA/QC certification documentation package. Outlined the importance of care/maintenance and warning against excessive running speeds.
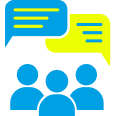
Ask yourself or your crew
- How can something like this happen here (e.g. on our site)?
- What safety measures (i.e. procedures, controls/barriers) do we have in place to mitigate the risk?
- How do we know the risk controls/barriers are working?
- What improvements or changes should we make to the procedures, controls/barriers or the way we work?
Published on 12/06/23
1108 Views
A 40-ton MYT elevator's setting plate broke after an 8-meter string fall. As a result of rapid lifting before the slips were fully set, the pipe collar damaged the elevators. Although no injuries occurred, the incident had the potential for serious harm to personnel and other equipment.
Original material courtesy of Energy Safety Canada