-
What happened?
During routine cementing operations prior to making up the cement head, the annulus casing packer (ACP) shut-off plug was ejected from the well.
It was ejected approximately 5m (16 feet) vertically from the hole and landed approximately 1m (3 feet) from the nearest crew member.
No injuries or damage resulted.
-
Why did it happen?
A high viscosity fluid was pumped downhole as part of a management of change on a well that had high losses and no returns expected on the annulus.
An air bubble was trapped under the high viscosity mud due to fluid levels equalising in the casing string and annulus. The air bubble migrated up the well and caused the ejection of the ACP shut-off plug.
The planning and execution phase failed to identify trapped air as a hazard. The casing was not conditioned (circulating fluid to remove trapped air) prior to installing the ACP shut-off plug.
-
What did they learn?
Ensure exclusion zones are established and personnel remain out of line of fire.
Reinforce the importance of hazard identification when changes to work activities occur during drilling and completions operations.
Confirm personnel are aware of and comply with standard drilling program and procedures.
-
Ask yourself or your crew
Is there any potential for trapped pressure in your cementing activities that could result in a similar incident?
Are you effectively using assist and assure (Transition to work and Step 7) to plan and execute your work?
Are you aware of your standard drilling program and procedures? Are you following them? How do you know? What do you do when a deviation occurs?
Add to homescreen
Content name
Select existing category:
Content name
New collection
Edit collection
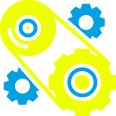
What happened?
During routine cementing operations prior to making up the cement head, the annulus casing packer (ACP) shut-off plug was ejected from the well.
It was ejected approximately 5m (16 feet) vertically from the hole and landed approximately 1m (3 feet) from the nearest crew member.
No injuries or damage resulted.
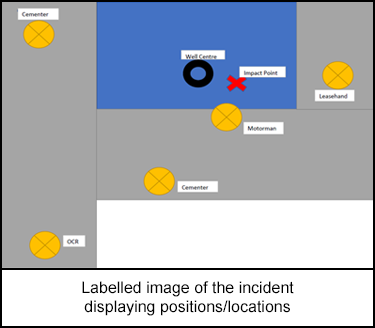
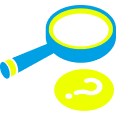
Why did it happen?
A high viscosity fluid was pumped downhole as part of a management of change on a well that had high losses and no returns expected on the annulus.
An air bubble was trapped under the high viscosity mud due to fluid levels equalising in the casing string and annulus. The air bubble migrated up the well and caused the ejection of the ACP shut-off plug.
The planning and execution phase failed to identify trapped air as a hazard. The casing was not conditioned (circulating fluid to remove trapped air) prior to installing the ACP shut-off plug.
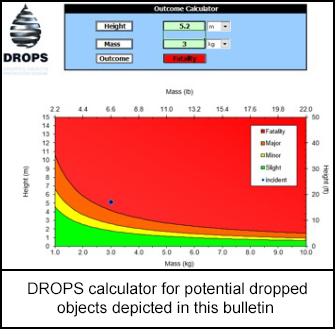
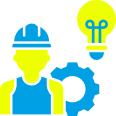
What did they learn?
Ensure exclusion zones are established and personnel remain out of line of fire.
Reinforce the importance of hazard identification when changes to work activities occur during drilling and completions operations.
Confirm personnel are aware of and comply with standard drilling program and procedures.
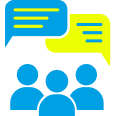
Ask yourself or your crew
Is there any potential for trapped pressure in your cementing activities that could result in a similar incident?
Are you effectively using assist and assure (Transition to work and Step 7) to plan and execute your work?
Are you aware of your standard drilling program and procedures? Are you following them? How do you know? What do you do when a deviation occurs?
During routine cementing operations, a shut-off plug was ejected from the well due to a trapped air bubble, landing close to a crew member but causing no injuries or damage. The incident was caused by a failure to identify and mitigate the hazard of trapped air during the planning and execution phases.
Original material courtesy of Safer Together (Australia)
To access the PDF and PowerPoint versions, please visit https://www.safertogether.com.au/resources/sharing-library/person-in-line-of-fire