-
What happened?
A rig was preparing for jetting out the blow out preventor prior to running in hole with 7” (18cm) production casing.
A joint of 4” (10cm) heavy weight drill pipe was loaded onto to the catwalk and raised to the work floor for the jetting operation.
The connection to the pipe was made using the hydraulic elevators and a visual check of the elevators confirmed that they were secured correctly.
As the 4” (10cm) heavy weight drill pipe was lifted the joint came free of the elevators. It dropped 200mm (8”) onto the V-door rollers and came to rest on the catwalk.
Nobody was in close vicinity when the heavy weight drill pipe dropped and came to rest.
-
Why did it happen?
The elevators were fitted with incorrect inserts to lift the 4” (10cm) heavy weight drill pipe. 4½” (11cm) inserts were fitted instead of the correct 4” (10cm) inserts. This allowed the heavy weight drill pipe to slide through the elevators.
The tripping tubulars procedure identified the need to check the inserts. This was not done prior to the task.
Jetting was a non-routine task. It was only the second well where the crew had conducted jetting.
Assist and Assure (Step 7) was not conducted prior to performing the task.
The dropped pipe did not breach the exclusion zone that was established. The catwalk pipe rack pins prevented the pipe from rolling off the catwalk.
-
What did they learn?
Investigate the viability of removing the need to change elevator inserts. In this instance, it was proposed to change machining the 6 ¼” (15.9cm) drill collar slip recess from 4 1⁄2” (11.4cm) outside diameter (OD) to 4 3⁄16” (10.6cm) OD to eliminate the need to change elevator inserts when transitioning from drill collars to drill pipe.
Utilise Assist and Assure tools (e.g. Step 7) to ensure that crews are familiar with the task and have reviewed associated procedures.
-
Ask yourself or your crew
How does your crew ensure that the correct sized inserts are being used on elevators during drill pipe operations?
What can be done to reduce variance in equipment setup?
Are you familiar with your tripping tubulars procedure? When was the last time you read it?
Do you conduct a Step 7 check before each task?
Add to homescreen
Content name
Select existing category:
Content name
New collection
Edit collection
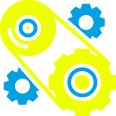
What happened?
A rig was preparing for jetting out the blow out preventor prior to running in hole with 7” (18cm) production casing.
A joint of 4” (10cm) heavy weight drill pipe was loaded onto to the catwalk and raised to the work floor for the jetting operation.
The connection to the pipe was made using the hydraulic elevators and a visual check of the elevators confirmed that they were secured correctly.
As the 4” (10cm) heavy weight drill pipe was lifted the joint came free of the elevators. It dropped 200mm (8”) onto the V-door rollers and came to rest on the catwalk.
Nobody was in close vicinity when the heavy weight drill pipe dropped and came to rest.
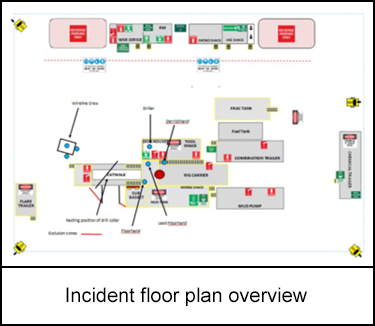
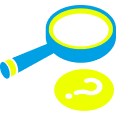
Why did it happen?
The elevators were fitted with incorrect inserts to lift the 4” (10cm) heavy weight drill pipe. 4½” (11cm) inserts were fitted instead of the correct 4” (10cm) inserts. This allowed the heavy weight drill pipe to slide through the elevators.
The tripping tubulars procedure identified the need to check the inserts. This was not done prior to the task.
Jetting was a non-routine task. It was only the second well where the crew had conducted jetting.
Assist and Assure (Step 7) was not conducted prior to performing the task.
The dropped pipe did not breach the exclusion zone that was established. The catwalk pipe rack pins prevented the pipe from rolling off the catwalk.
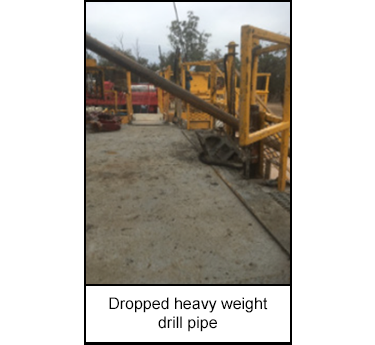
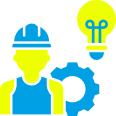
What did they learn?
Investigate the viability of removing the need to change elevator inserts. In this instance, it was proposed to change machining the 6 ¼” (15.9cm) drill collar slip recess from 4 1⁄2” (11.4cm) outside diameter (OD) to 4 3⁄16” (10.6cm) OD to eliminate the need to change elevator inserts when transitioning from drill collars to drill pipe.
Utilise Assist and Assure tools (e.g. Step 7) to ensure that crews are familiar with the task and have reviewed associated procedures.
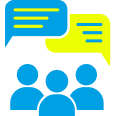
Ask yourself or your crew
How does your crew ensure that the correct sized inserts are being used on elevators during drill pipe operations?
What can be done to reduce variance in equipment setup?
Are you familiar with your tripping tubulars procedure? When was the last time you read it?
Do you conduct a Step 7 check before each task?
During a jetting operation, a 4" (10 cm) heavy weight drill pipe slipped from the hydraulic elevators due to incorrect inserts being used, causing the pipe to drop 200 mm (8") onto the V-door rollers and come to rest on the catwalk. Fortunately, no personnel were in the vicinity when the incident occurred.
Original material courtesy of Safer Together (Australia)
To access the PDF and PowerPoint versions, please visit https://www.safertogether.com.au/resources/sharing-library/drilling-completing-a-well-dropped-objects-learning-event-bulletin