-
What happened?
During a planned partial maintenance shutdown, two out of five cryogenic towers were put out of service.
The entrance pressure at the slug catcher rose from 1350psi to 1450psi, originating a major gas leak in a blind flange at a tie-in of a recently installed flowline (pressure safety valves (PSVs) were set to open at 1800psi).
A level 3 shutdown was activated, closing the remaining three operational towers in the facility.
The slug catcher area was depressurised, the blind flange was repaired, and safe working conditions were verified.
-
Why did it happen?
The high level (HL) trip was activated in the towers due to a false signal in a low-pressure switch (recently serviced). This activation closed the towers' discharge valves.
Delays in work execution caused separate tasks to overlap, resulting in too many people working in the same area simultaneously and operating the same electrical panels and circuits.
The different work crews were not aware of the complexity of the new electrical system or its impact on other areas of the plant.
The torque procedure and final torque verification report were not fully validated before start-up.
Some electrical components were not fully operational, nor tested when start-up of the facility took place.
There were not enough workers to complete all the tasks, and those present did not have the required experience.
-
What did they learn?
Transmitters are recommended for shutdown functions. Switches shouldn’t be used to detect process trip parameters.
Verify how the HL trips are set in the de-ethanization towers, including their alarms. Define a policy for alarms modification regarding users and access levels.
Ensure that work permits for signal panels include all signals (directly or indirectly) involved in the task being performed.
Communicate and verify compliance with the standard for commissioning of automation and control systems.
Examine and update the procedures for torque tasks (i.e. related to blind flanges) where necessary. Communicate any updates to all involved.
-
Ask yourself or your crew
What is the worst that could have happened here?
How can we prevent something similar from happening on our site?
Is the equipment you are working on integrated with other systems on-site? How do they interact/impact on each other?
Are you fully trained to perform your duties? What should you do if you, or another crew member require additional training?
What should we do if tasks take longer than expected, and more crews are in the same work area simultaneously?
Add to homescreen
Content name
Select existing category:
Content name
New collection
Edit collection
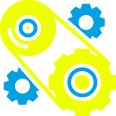
What happened?
During a planned partial maintenance shutdown, two out of five cryogenic towers were put out of service.
The entrance pressure at the slug catcher rose from 1350psi to 1450psi, originating a major gas leak in a blind flange at a tie-in of a recently installed flowline (pressure safety valves (PSVs) were set to open at 1800psi).
A level 3 shutdown was activated, closing the remaining three operational towers in the facility.
The slug catcher area was depressurised, the blind flange was repaired, and safe working conditions were verified.
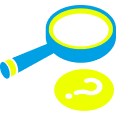
Why did it happen?
The high level (HL) trip was activated in the towers due to a false signal in a low-pressure switch (recently serviced). This activation closed the towers' discharge valves.
Delays in work execution caused separate tasks to overlap, resulting in too many people working in the same area simultaneously and operating the same electrical panels and circuits.
The different work crews were not aware of the complexity of the new electrical system or its impact on other areas of the plant.
The torque procedure and final torque verification report were not fully validated before start-up.
Some electrical components were not fully operational, nor tested when start-up of the facility took place.
There were not enough workers to complete all the tasks, and those present did not have the required experience.
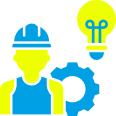
What did they learn?
Transmitters are recommended for shutdown functions. Switches shouldn’t be used to detect process trip parameters.
Verify how the HL trips are set in the de-ethanization towers, including their alarms. Define a policy for alarms modification regarding users and access levels.
Ensure that work permits for signal panels include all signals (directly or indirectly) involved in the task being performed.
Communicate and verify compliance with the standard for commissioning of automation and control systems.
Examine and update the procedures for torque tasks (i.e. related to blind flanges) where necessary. Communicate any updates to all involved.
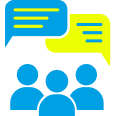
Ask yourself or your crew
What is the worst that could have happened here?
How can we prevent something similar from happening on our site?
Is the equipment you are working on integrated with other systems on-site? How do they interact/impact on each other?
Are you fully trained to perform your duties? What should you do if you, or another crew member require additional training?
What should we do if tasks take longer than expected, and more crews are in the same work area simultaneously?
During a planned partial maintenance shutdown, two out of five cryogenic towers were out of service. The entrance pressure at the slug catcher rose, originating a major gas leak in a blind flange at a tie-in of a recently installed flowline. A level 3 shutdown was activated, closing the remaining three operational towers in the facility.