-
What happened?
An unknown person or persons entered a remote production facility during the night and proceeded to remove approximately 125m (about 410.1 ft) of #1-gauge copper cable.
The cable was designed to provide power to an electric drive compressor. The cable ran from a circuit breaker onto a cable tray and into the ground before reaching the compressor. The cable supplied approximately 440 volts to the electrical equipment.
When the compressor was identified as offline, an operator travelled to the site and assessed the situation. It was evident that the compressor's electrical cable had been removed.
The operator checked the main electrical control panel and discovered that the electrical breaker designed to protect and isolate the compressor was still energised.
-
Why did it happen?
Industrial metal theft is on the rise. The comparatively high commodity price and the relative ease of reselling and reusing copper have made it an attractive target for opportunistic thieves and organised criminal gangs.
Remote worksites and facilities are increasingly targeted by thieves because they pose a low risk of being caught and important industrial metals and equipment are highly valuable.
-
What did they learn?
To protect themselves, the thief or thieves appear to have isolated the electrical supply by switching off the breaker to the compressor before cutting and removing the section of copper cable.
After cutting the cable, the system was re-energised by switching the breaker back on. This created a significant electrical hazard, with the live end of the cut cable potentially causing serious injury or fatality to site employees and first responders.
The operator's knowledge of the site equipment and the potential for serious harm from high-voltage electrical systems enabled an effective response that isolated the power supplied to the cut cable.
Always assume that electrical cables (even cables that have been cut) and associated equipment are live or energised until you can confirm that power has been deactivated and any residual electricity has been discharged.
-
Ask yourself or your crew
Could something like this happen at our worksite or remote equipment locations?
Who has authorised access to your remote sites? Are they familiar with the energised systems and potential equipment damage or vandalism hazards?
What is your energy isolation process for defective, damaged or vandalised plant and equipment?
Do you have a safe shutdown procedure when equipment has been vandalised?
Do non-technical first responders (police, fire, medical, private security) understand the hazards present at your worksite?
Add to homescreen
Content name
Select existing category:
Content name
New collection
Edit collection
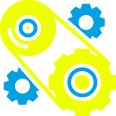
What happened?
An unknown person or persons entered a remote production facility during the night and proceeded to remove approximately 125m (about 410.1 ft) of #1-gauge copper cable.
The cable was designed to provide power to an electric drive compressor. The cable ran from a circuit breaker onto a cable tray and into the ground before reaching the compressor. The cable supplied approximately 440 volts to the electrical equipment.
When the compressor was identified as offline, an operator travelled to the site and assessed the situation. It was evident that the compressor's electrical cable had been removed.
The operator checked the main electrical control panel and discovered that the electrical breaker designed to protect and isolate the compressor was still energised.
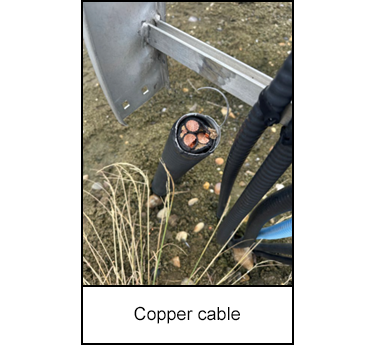
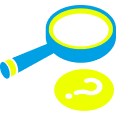
Why did it happen?
Industrial metal theft is on the rise. The comparatively high commodity price and the relative ease of reselling and reusing copper have made it an attractive target for opportunistic thieves and organised criminal gangs.
Remote worksites and facilities are increasingly targeted by thieves because they pose a low risk of being caught and important industrial metals and equipment are highly valuable.
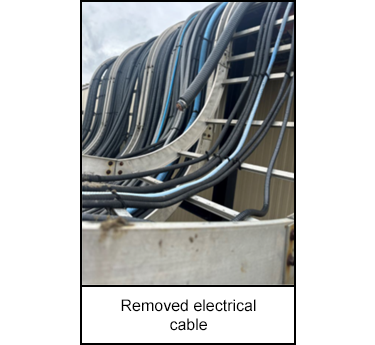
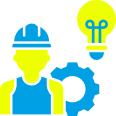
What did they learn?
To protect themselves, the thief or thieves appear to have isolated the electrical supply by switching off the breaker to the compressor before cutting and removing the section of copper cable.
After cutting the cable, the system was re-energised by switching the breaker back on. This created a significant electrical hazard, with the live end of the cut cable potentially causing serious injury or fatality to site employees and first responders.
The operator's knowledge of the site equipment and the potential for serious harm from high-voltage electrical systems enabled an effective response that isolated the power supplied to the cut cable.
Always assume that electrical cables (even cables that have been cut) and associated equipment are live or energised until you can confirm that power has been deactivated and any residual electricity has been discharged.
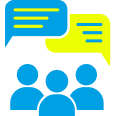
Ask yourself or your crew
Could something like this happen at our worksite or remote equipment locations?
Who has authorised access to your remote sites? Are they familiar with the energised systems and potential equipment damage or vandalism hazards?
What is your energy isolation process for defective, damaged or vandalised plant and equipment?
Do you have a safe shutdown procedure when equipment has been vandalised?
Do non-technical first responders (police, fire, medical, private security) understand the hazards present at your worksite?
An unknown individual(s) stole approximately 125 metres (410 feet) of copper cable from a remote production facility, causing an electric drive compressor to go offline. The operator checked the main electrical control panel and discovered that the electrical breaker designed to protect and isolate the compressor was still energised, presenting a significant electrical hazard.
Original material courtesy of Energy Safety Canada