-
What happened?
A coil tubing crew was running a fibre optic string into a production well.
While placing the coil tubing into the well, the blowout preventor (BOP) separated from the wellhead.
This resulted in damage to the coil tubing and loss of well control protection.
-
Why did it happen?
A connector that mated the BOP with the coil tubing riding valve was worn. In addition, because of its design using a ring, the connector was subject to a specific failure mode leading to separation.
The crane hook holding the injector was excessively pulling up (i.e., too much hook weight) on the injector and stack, causing the injector and BOP to jump off the stack when the connection failed.
-
What did they learn?
- The connection type that uses a ring was replaced with a new design that is not subject to the same failure mode.
- Load cells were installed on all cranes to monitor hook weight during all lifts and when holding equipment on wellheads. The procedure was modified accordingly to define allowable hook weights.
- The inspection procedure was updated to require visual inspection of all threaded and flanged connections in the stack prior to being placed on the wellhead.
-
Ask yourself or your crew
- How can something like this happen here (e.g. on our site)?
- What safety measures (i.e. procedures, controls/barriers) do we have in place to mitigate the risk?
- How do we know the risk controls/barriers are working?
- What improvements or changes should we make to the procedures, controls/barriers or the way we work?
Add to homescreen
If you want to add this app to home screen tap and then ‘Add to Home Screen’.
Content name
Select existing category:
Content name
New collection
Edit collection
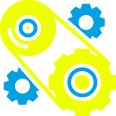
What happened?
A coil tubing crew was running a fibre optic string into a production well.
While placing the coil tubing into the well, the blowout preventor (BOP) separated from the wellhead.
This resulted in damage to the coil tubing and loss of well control protection.
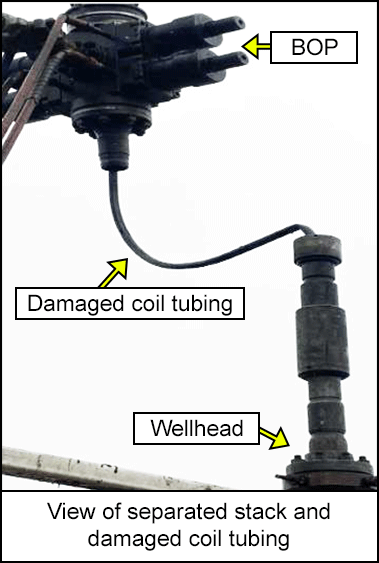
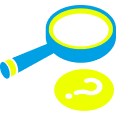
Why did it happen?
A connector that mated the BOP with the coil tubing riding valve was worn. In addition, because of its design using a ring, the connector was subject to a specific failure mode leading to separation.
The crane hook holding the injector was excessively pulling up (i.e., too much hook weight) on the injector and stack, causing the injector and BOP to jump off the stack when the connection failed.
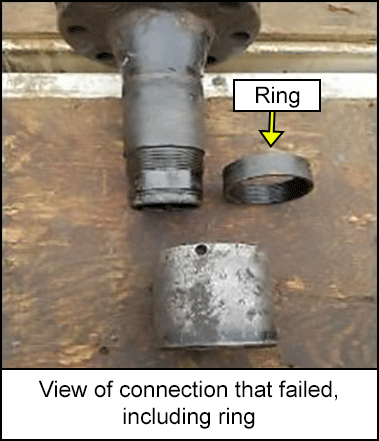
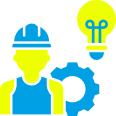
What did they learn?
- The connection type that uses a ring was replaced with a new design that is not subject to the same failure mode.
- Load cells were installed on all cranes to monitor hook weight during all lifts and when holding equipment on wellheads. The procedure was modified accordingly to define allowable hook weights.
- The inspection procedure was updated to require visual inspection of all threaded and flanged connections in the stack prior to being placed on the wellhead.
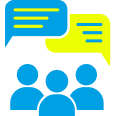
Ask yourself or your crew
- How can something like this happen here (e.g. on our site)?
- What safety measures (i.e. procedures, controls/barriers) do we have in place to mitigate the risk?
- How do we know the risk controls/barriers are working?
- What improvements or changes should we make to the procedures, controls/barriers or the way we work?
Published on 08/06/23
1663 Views
A coil tubing crew was running a fibre optic string into a production well. While placing the coil tubing into the well, the blowout preventer (BOP) separated from the wellhead. This resulted in damage to the coil tubing and loss of well control protection.
Original material courtesy of Energy Safety Canada
Other industry resources:
DACC IRP Volume #21 – Coiled Tubing Operations
Process Safety: A Barrier Focused Approach
Process Safety Posters