-
What happened?
A coil tubing crew were in the process of pulling out of the hole.
After the bottom hole assembly (BHA) reached 150 metres (500 ft) below surface, the coil tubing unit (CTU) operator received a phone call from his supervisor and began other activities while monitoring the BHA depth.
The BHA reached surface at 90 ft/min and pulled into the CTU injector head with 8000 lbs. of overpull, causing the coil tubing pipe to forcibly disconnect from the BHA.
This resulted in an uncontrolled 24 metres (80 ft) section of coil tubing pipe to strike the coil unit tractor and equipment, narrowly missing a worker.
The well bore pressure (2300psi) caused 38 litres (10 gallons) of well injection fluid to be released.
Blowout preventer well control contingencies were promptly initiated, and the well was secured.
-
Why did it happen?
Critical well intervention equipment failed:
- The coil saver feature was not set at the correct values, and therefore the electronic intervention did not function.
- The stripper brass bushing was slightly out of tolerance, which allowed the logging BHA to pass through the stripper brass bushing and into the CTU injector head.
The phone call received by the CTU operator impacted his ability to focus on the critical task of monitoring the BHA depth and reducing the pull out of hole speed as the BHA travelled closer to the surface.
-
What did they learn?
Conduct analytical tolerance inspections on all CTU stripper brass bushings.
Incorporate a CTU “end of pipe warning” in the coil operating parameter system that is like the system currently in place with coil tubing drilling system rigs.
Develop a reference page for CTU operators to establish alarm settings at specified depths.
Adopt or modify existing electronic communication device policy during critical stages of work.
Establish and discuss exclusion zones during job tasks that have a high potential for pressure, dropped objects, and objects in motion hazards.
-
Ask yourself or your crew
- How can something like this happen here (e.g. on our site)?
- What safety measures (i.e. procedures, controls/barriers) do we have in place to mitigate the risk?
- How do we know the risk controls/barriers are working?
- What improvements or changes should we make to the procedures, controls/barriers or the way we work?
Add to homescreen
Content name
Select existing category:
Content name
New collection
Edit collection
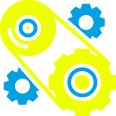
What happened?
A coil tubing crew were in the process of pulling out of the hole.
After the bottom hole assembly (BHA) reached 150 metres (500 ft) below surface, the coil tubing unit (CTU) operator received a phone call from his supervisor and began other activities while monitoring the BHA depth.
The BHA reached surface at 90 ft/min and pulled into the CTU injector head with 8000 lbs. of overpull, causing the coil tubing pipe to forcibly disconnect from the BHA.
This resulted in an uncontrolled 24 metres (80 ft) section of coil tubing pipe to strike the coil unit tractor and equipment, narrowly missing a worker.
The well bore pressure (2300psi) caused 38 litres (10 gallons) of well injection fluid to be released.
Blowout preventer well control contingencies were promptly initiated, and the well was secured.
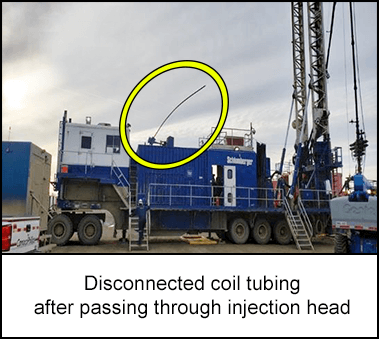
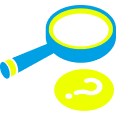
Why did it happen?
Critical well intervention equipment failed:
- The coil saver feature was not set at the correct values, and therefore the electronic intervention did not function.
- The stripper brass bushing was slightly out of tolerance, which allowed the logging BHA to pass through the stripper brass bushing and into the CTU injector head.
The phone call received by the CTU operator impacted his ability to focus on the critical task of monitoring the BHA depth and reducing the pull out of hole speed as the BHA travelled closer to the surface.
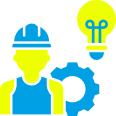
What did they learn?
Conduct analytical tolerance inspections on all CTU stripper brass bushings.
Incorporate a CTU “end of pipe warning” in the coil operating parameter system that is like the system currently in place with coil tubing drilling system rigs.
Develop a reference page for CTU operators to establish alarm settings at specified depths.
Adopt or modify existing electronic communication device policy during critical stages of work.
Establish and discuss exclusion zones during job tasks that have a high potential for pressure, dropped objects, and objects in motion hazards.
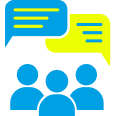
Ask yourself or your crew
- How can something like this happen here (e.g. on our site)?
- What safety measures (i.e. procedures, controls/barriers) do we have in place to mitigate the risk?
- How do we know the risk controls/barriers are working?
- What improvements or changes should we make to the procedures, controls/barriers or the way we work?
During the extraction process, after the equipment reached a depth of 150 metres (500 ft) below the surface, the coil tubing operator received a call, diverting their attention. This led to a rapid and uncontrolled extraction, resulting in a section of pipe disconnecting, narrowly avoiding harm to a worker and causing a release of well fluid due to high pressure. The team quickly implemented well control measures, securing the well.