-
What happened?
Work crews were relocating two shipping containers. The job plan and work permit involved loading the containers onto a trailer using a crane.
During work execution, the containers were winched onto a flatbed trailer. The first container was loaded without any incidents.
During winching operations, the second container snagged the grouser bars on the trailer putting extra tension on the rigging.
The chain rigging failed, propelling the winch cable forward towards the worker operating the controls and striking him in the head.
The worker received sutures to his forehead and was released to work without restrictions.
-
Why did it happen?
The executed work scope did not align with the scope on the work permit. The risk assessment did not adequately cover the work performed and a last-minute decision led to the wrong equipment being used.
The rigging was not used for its intended purpose, was not inspected, and the load weight exceeded the rigging capacity prior to accounting for the friction caused by pulling the container.
The activities were outlined on a 30-day permit for general approval that covered a range of activities. Generally, the permitting process had grown too broad, covering all activities instead of specific activities.
Visual confirmation by a supervisor was not done effectively.
Contractors worked outside of the client’s HSE management processes, even though they carried out high-risk activities.
HSE content and role and responsibilities were not reviewed during kick-off meetings.
-
What did they learn?
Operators should remain out of the line of fire during winching activities. Introduce defences or consider the implementation of physical barriers for worker protection.
Ensure you know and follow all established work control procedures and guidelines for your tasks. Seek assistance when needed.
Ensure that tasks are appropriately sized for safe execution, that you have the necessary work permits, and that you understand and adhere to the scope of work outlined in the permits. Seek clarification if needed.
Encourage the use of planning tools for making informed decisions about task supervision.
Stay updated on any changes in standards, especially concerning chain use and winching, and update as necessary. Include allowable and/or banned chain use activities and defences for winching.
Define and communicate the healthy and safety management systems expectations for contractors, specifying which management system they are operating under. Additionally, ensure that the subcontractor management processes are well-assured.
-
Ask yourself or your crew
How can something like this happen here?
How do you ensure that the equipment you use for lifting and hoisting is appropriate for the task?
Can you walk me through your process for inspecting rigging before use, especially when dealing with heavy loads?
How do you handle situations where the equipment or rigging seems to be inadequate or unsuitable for the task?
What safety measures (i.e. procedures, controls/barriers) do we have in place to mitigate the risk?
What improvements or changes should we make to the procedures, controls/barriers or the way we work to make our operations safer?
Add to homescreen
Content name
Select existing category:
Content name
New collection
Edit collection
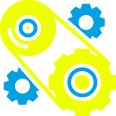
What happened?
Work crews were relocating two shipping containers. The job plan and work permit involved loading the containers onto a trailer using a crane.
During work execution, the containers were winched onto a flatbed trailer. The first container was loaded without any incidents.
During winching operations, the second container snagged the grouser bars on the trailer putting extra tension on the rigging.
The chain rigging failed, propelling the winch cable forward towards the worker operating the controls and striking him in the head.
The worker received sutures to his forehead and was released to work without restrictions.
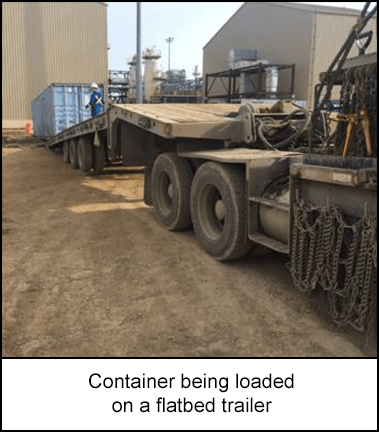
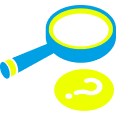
Why did it happen?
The executed work scope did not align with the scope on the work permit. The risk assessment did not adequately cover the work performed and a last-minute decision led to the wrong equipment being used.
The rigging was not used for its intended purpose, was not inspected, and the load weight exceeded the rigging capacity prior to accounting for the friction caused by pulling the container.
The activities were outlined on a 30-day permit for general approval that covered a range of activities. Generally, the permitting process had grown too broad, covering all activities instead of specific activities.
Visual confirmation by a supervisor was not done effectively.
Contractors worked outside of the client’s HSE management processes, even though they carried out high-risk activities.
HSE content and role and responsibilities were not reviewed during kick-off meetings.
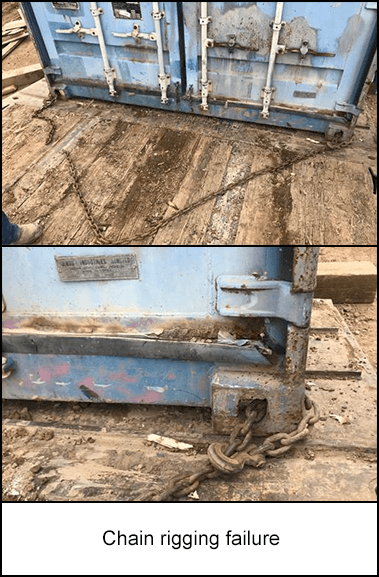
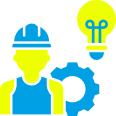
What did they learn?
Operators should remain out of the line of fire during winching activities. Introduce defences or consider the implementation of physical barriers for worker protection.
Ensure you know and follow all established work control procedures and guidelines for your tasks. Seek assistance when needed.
Ensure that tasks are appropriately sized for safe execution, that you have the necessary work permits, and that you understand and adhere to the scope of work outlined in the permits. Seek clarification if needed.
Encourage the use of planning tools for making informed decisions about task supervision.
Stay updated on any changes in standards, especially concerning chain use and winching, and update as necessary. Include allowable and/or banned chain use activities and defences for winching.
Define and communicate the healthy and safety management systems expectations for contractors, specifying which management system they are operating under. Additionally, ensure that the subcontractor management processes are well-assured.
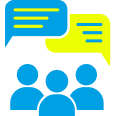
Ask yourself or your crew
How can something like this happen here?
How do you ensure that the equipment you use for lifting and hoisting is appropriate for the task?
Can you walk me through your process for inspecting rigging before use, especially when dealing with heavy loads?
How do you handle situations where the equipment or rigging seems to be inadequate or unsuitable for the task?
What safety measures (i.e. procedures, controls/barriers) do we have in place to mitigate the risk?
What improvements or changes should we make to the procedures, controls/barriers or the way we work to make our operations safer?
Using a crane, work crews were tasked with relocating two containers. The first container was loaded without incident, however while loading the second container, the chain rigging failed propelling the winch cable forward towards the worker operating the controls, striking him in the head.