-
What happened?
The workers were processing slurry from a storage tank that was used to store shaker screen runoff.
A vac truck was used to direct feed the centrifuge through the centrifuge feed pump.
As the second load was finished, the centrifuge operator went to the PLC (programmable logic controller) controls to wind down the machine from its operating speed.
At this point, the centrifuge made a loud noise and began to vibrate. Immediately after the loud noise, the centrifuge back drive motor, gearbox and drive shaft were ejected from the centrifuge stand, falling to the ground.
-
Why did it happen?
It was determined that the most likely cause of failure was gradual and repetitive overloading of the conveyor drive as a result of a solids blockage at the solids end.
This overload and blockage produced sufficient axial loading that stretched the conical and the cylindrical section bolts, creating an uneven gap in the mating surfaces due to the ‘power screw’ forces shown at the solids end.
These forces can become large in magnitude and cause many components to overload, however, in this instance, it caused a significant imbalance of the conical section, causing the cascading failures of the centrifuge assembly.
-
What did they learn?
A storage tank is utilised to store shaker screen drill fluid runoff that collects in the cuttings tank, which is located directly underneath the shaker slide.
This fluid is later sucked out of the cuttings tank by a vac truck and stored in the storage tank until it is processed and added back into the main drilling fluid.
When the fluid/slurry is sucked out of the cuttings tank, it is common that drill cuttings and heavy solids are mixed in at that point.
Typically, the slurry from the storage tank is run over the shakers, which removes heavy solids, but that did not occur in this case.
-
Ask yourself or your crew
Could something like this happen on our worksite?
Have the fluids/slurry that are going to be processed through the centrifuge been screened?
Do the operators and the supervisors directing the use of centrifuges understand the need for screening slurry to protect the centrifuge?
Add to homescreen
Content name
Select existing category:
Content name
New collection
Edit collection
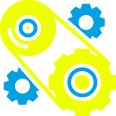
What happened?
The workers were processing slurry from a storage tank that was used to store shaker screen runoff.
A vac truck was used to direct feed the centrifuge through the centrifuge feed pump.
As the second load was finished, the centrifuge operator went to the PLC (programmable logic controller) controls to wind down the machine from its operating speed.
At this point, the centrifuge made a loud noise and began to vibrate. Immediately after the loud noise, the centrifuge back drive motor, gearbox and drive shaft were ejected from the centrifuge stand, falling to the ground.
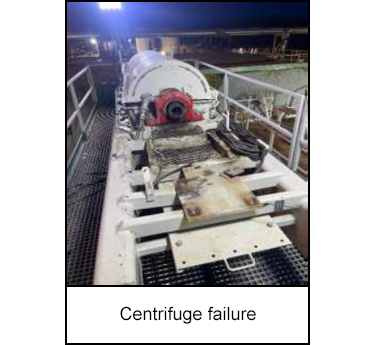
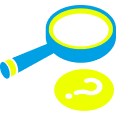
Why did it happen?
It was determined that the most likely cause of failure was gradual and repetitive overloading of the conveyor drive as a result of a solids blockage at the solids end.
This overload and blockage produced sufficient axial loading that stretched the conical and the cylindrical section bolts, creating an uneven gap in the mating surfaces due to the ‘power screw’ forces shown at the solids end.
These forces can become large in magnitude and cause many components to overload, however, in this instance, it caused a significant imbalance of the conical section, causing the cascading failures of the centrifuge assembly.
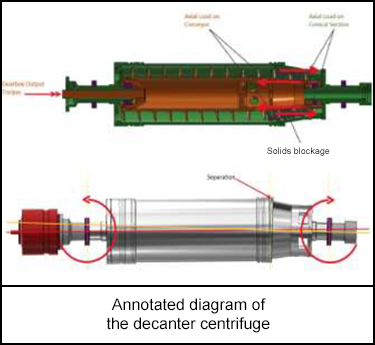
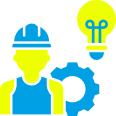
What did they learn?
A storage tank is utilised to store shaker screen drill fluid runoff that collects in the cuttings tank, which is located directly underneath the shaker slide.
This fluid is later sucked out of the cuttings tank by a vac truck and stored in the storage tank until it is processed and added back into the main drilling fluid.
When the fluid/slurry is sucked out of the cuttings tank, it is common that drill cuttings and heavy solids are mixed in at that point.
Typically, the slurry from the storage tank is run over the shakers, which removes heavy solids, but that did not occur in this case.
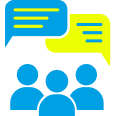
Ask yourself or your crew
Could something like this happen on our worksite?
Have the fluids/slurry that are going to be processed through the centrifuge been screened?
Do the operators and the supervisors directing the use of centrifuges understand the need for screening slurry to protect the centrifuge?
While processing slurry, the centrifuge experienced a loud noise and vibration, leading to the ejection of its back drive motor, gearbox, and drive shaft. The failure was attributed to repetitive overloading and a solids blockage, causing significant imbalance and cascading failures in the centrifuge assembly.
Original material courtesy of Energy Safety Canada