-
What happened?
A truck mounted drilling rig was conducting operations to remove casing from the ground.
During operations, a section of stuck casing was encountered.
The rig operator attempted to pull on the stuck casing using a hoist on a truck equipped with a ½” (13mm) cable.
While under tension the ½” (13mm) hoist cable broke causing whiplash in the parted line which contacted the rig operator’s hard hat, resulting in an abrasion to operator’s forehead.
First aid treatment was provided for the injury sustained. However, the potential for serious injury to have occurred was present.
-
Why did it happen?
The manufacturer recommendation for raising stuck loads was not followed - the feed mechanism of the drill should have been used instead of the hoist.
The manufacturer’s recommended procedure for removing stuck casing was not clearly incorporated into the work practices.
Cables become frayed during normal operations, and are replaced regularly due to wear, as often as daily.
The frayed cables had become a normal occurrence and an accepted deviation.
The rig design required the operator to be positioned in the line of fire with no guards.
There was a lack of guards against rotating parts and the positioning of the rig operator within the exclusion zone was not addressed.
-
What did they learn?
Ensure that the manufacturer's recommended procedures are clearly documented, communicated, and incorporated into work instructions i.e. using the feed mechanism of the drill instead of the hoist for raising stuck loads.
Implement a robust inspection and maintenance program for cables. Frayed cables should not become an accepted norm, and their replacement frequency should be based on usage and wear analysis rather than routine schedules.
Redesign or modify equipment to ensure the operator is not in the line of fire. Install guards or barriers to protect operators from rotating parts and cable whiplash. This could include shields around the hoist area or redesigning the operator's control area to be outside the exclusion zone.
Enhance pre-job planning to include detailed discussions on potential hazards, such as line-of-fire risks, and ensure these are addressed before work begins.
Strengthen the "see-something-say-something" culture by encouraging workers to report unsafe conditions without fear of reprisal. Provide training on recognising and addressing hazards like frayed cables and improper operator positioning.
Conduct regular safety audits to ensure compliance with procedures and identify potential hazards before they lead to incidents.
-
Ask yourself or your crew
What should be done when excessive wear and tear is observed on equipment?
Are concerns for potential line of fire impacts routinely discussed in pre-job planning?
Is “see-something-say-something” supported in your work areas?
What steps are taken to implement appropriate corrections that drive safety improvements?
How are work procedures being followed when performing tasks? How frequently are these procedures reviewed and updated to capture improvement opportunities?
Add to homescreen
Content name
Select existing category:
Content name
New collection
Edit collection
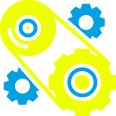
What happened?
A truck mounted drilling rig was conducting operations to remove casing from the ground.
During operations, a section of stuck casing was encountered.
The rig operator attempted to pull on the stuck casing using a hoist on a truck equipped with a ½” (13mm) cable.
While under tension the ½” (13mm) hoist cable broke causing whiplash in the parted line which contacted the rig operator’s hard hat, resulting in an abrasion to operator’s forehead.
First aid treatment was provided for the injury sustained. However, the potential for serious injury to have occurred was present.
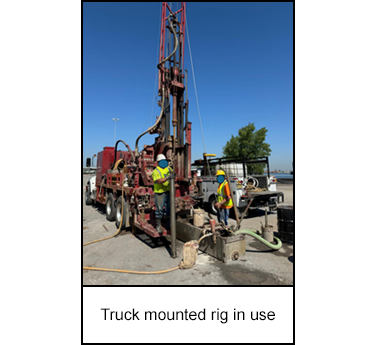
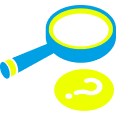
Why did it happen?
The manufacturer recommendation for raising stuck loads was not followed - the feed mechanism of the drill should have been used instead of the hoist.
The manufacturer’s recommended procedure for removing stuck casing was not clearly incorporated into the work practices.
Cables become frayed during normal operations, and are replaced regularly due to wear, as often as daily.
The frayed cables had become a normal occurrence and an accepted deviation.
The rig design required the operator to be positioned in the line of fire with no guards.
There was a lack of guards against rotating parts and the positioning of the rig operator within the exclusion zone was not addressed.
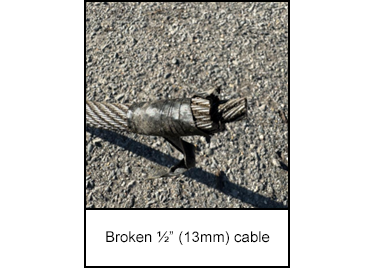
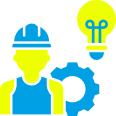
What did they learn?
Ensure that the manufacturer's recommended procedures are clearly documented, communicated, and incorporated into work instructions i.e. using the feed mechanism of the drill instead of the hoist for raising stuck loads.
Implement a robust inspection and maintenance program for cables. Frayed cables should not become an accepted norm, and their replacement frequency should be based on usage and wear analysis rather than routine schedules.
Redesign or modify equipment to ensure the operator is not in the line of fire. Install guards or barriers to protect operators from rotating parts and cable whiplash. This could include shields around the hoist area or redesigning the operator's control area to be outside the exclusion zone.
Enhance pre-job planning to include detailed discussions on potential hazards, such as line-of-fire risks, and ensure these are addressed before work begins.
Strengthen the "see-something-say-something" culture by encouraging workers to report unsafe conditions without fear of reprisal. Provide training on recognising and addressing hazards like frayed cables and improper operator positioning.
Conduct regular safety audits to ensure compliance with procedures and identify potential hazards before they lead to incidents.
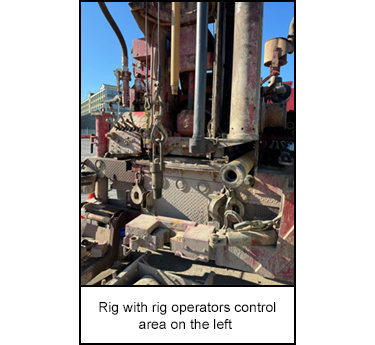
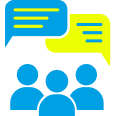
Ask yourself or your crew
What should be done when excessive wear and tear is observed on equipment?
Are concerns for potential line of fire impacts routinely discussed in pre-job planning?
Is “see-something-say-something” supported in your work areas?
What steps are taken to implement appropriate corrections that drive safety improvements?
How are work procedures being followed when performing tasks? How frequently are these procedures reviewed and updated to capture improvement opportunities?
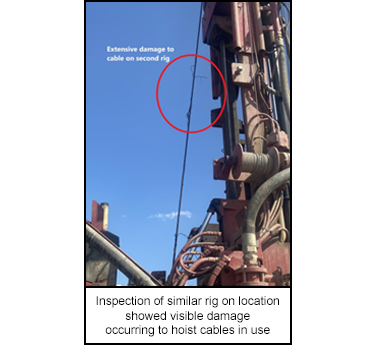
During casing removal operations, a truck-mounted drilling rig encountered stuck casing, and the hoist cable broke under tension, causing whiplash that injured the rig operator's forehead. First aid was administered, but the incident had the potential for more serious injury.